I have finally started my construction of OB-5's. The design of the speakers will be a bit different than the usual and will incorporate curved sides. I thought about curving the braces and then wrapping thin MDF in several bands around them, but decided on actually cutting curved sides out of 1⅛" MDF (that is some heavy stuff). So of course, this required building a jig to cut the curve.
Well, I was going to add some photos here but can't see how I get the photos from my album to post here??? Okay, figured it out. Thanks for the help ebag4.

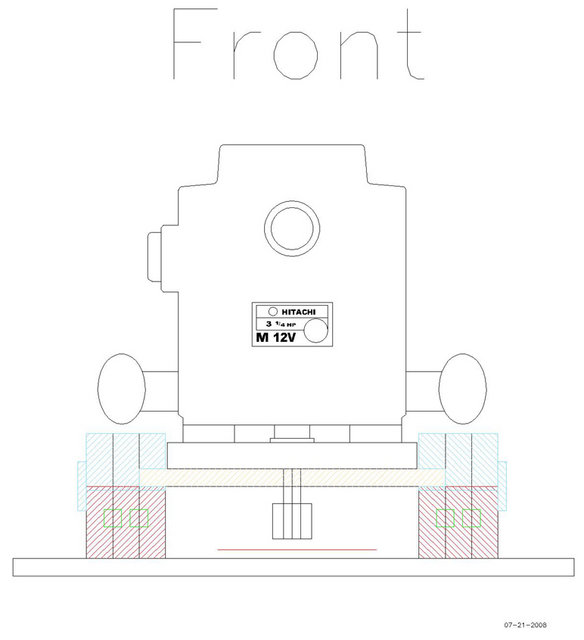
I drew this up using AutoCad 2004 so I could get a good idea of what was needed and the dimensions necessary to make things fit.
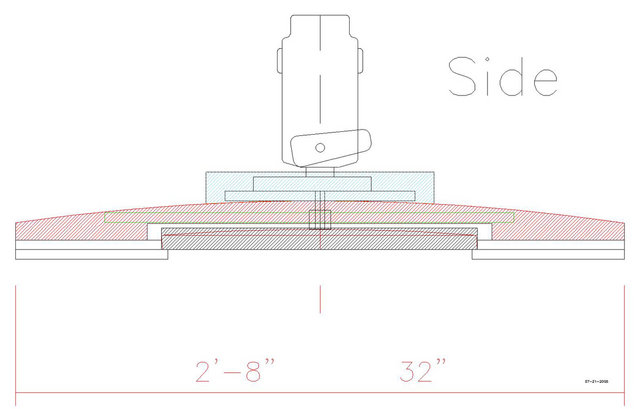
Side view of curved-side cutting jig. This will make a 9' radius cut.
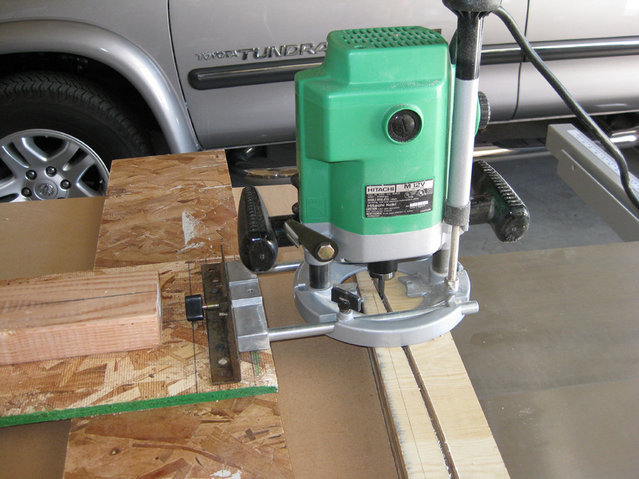
The first task was to accurately cut the bottom rail and top carriage runners at a 9'1.77" radius. This required a lot of preparation.
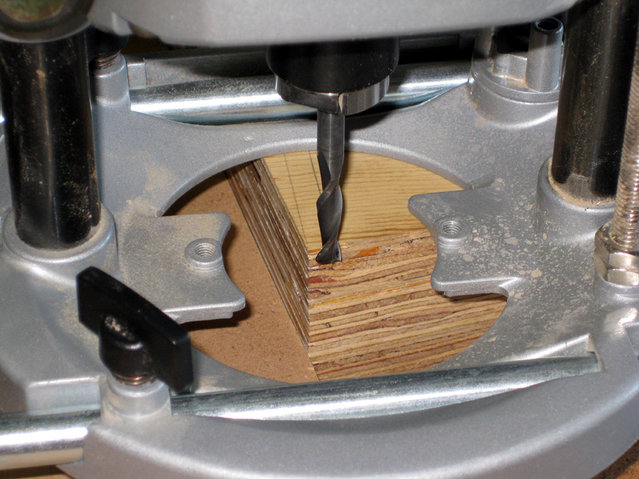
The cutting bit is a BOSCH micro solid carbide, upcut, end mill. ¼" cut ¼" shank, 2½" OAL.
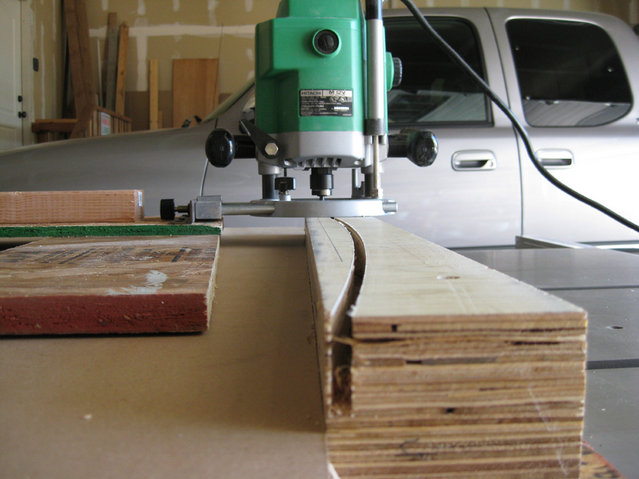
The cut had to be perfect at 90 degrees. Each pass would cut about ⅛" (2mm) off.
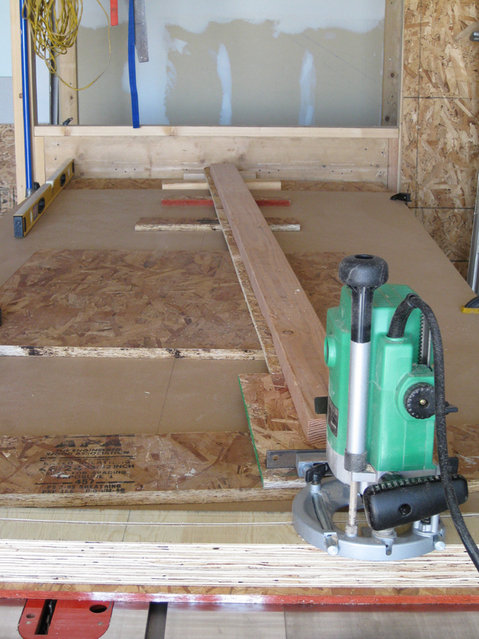
Here is the 9' extension to hold the router.
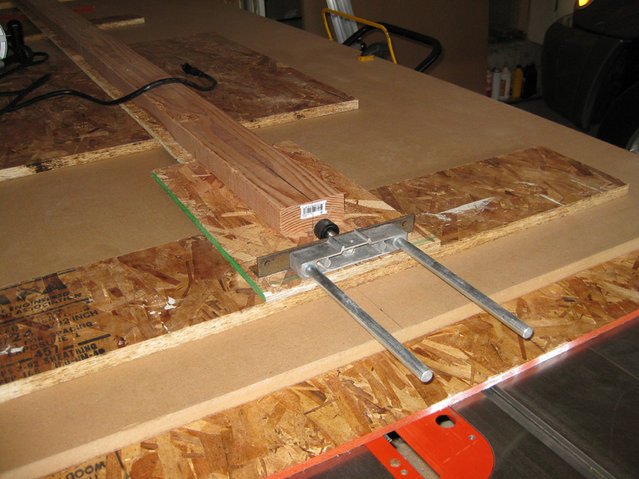
The edge guide that came with the router made the perfect connection piece.
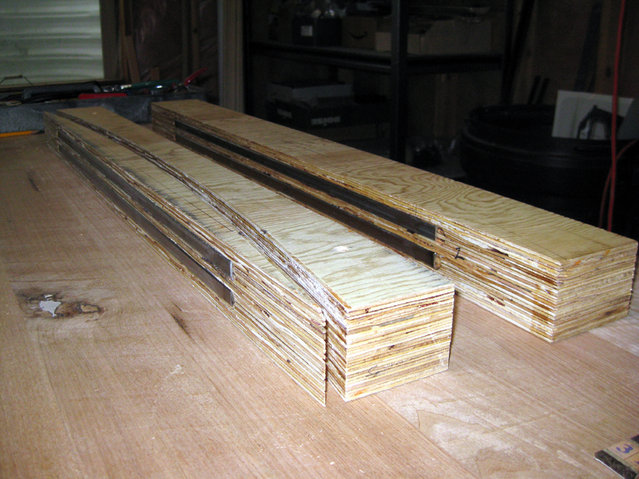
Here is one side of the guide rails cut. I've embedded two ½" rectangular steel tubes into the bottom of the rails to help support the weight of the router.
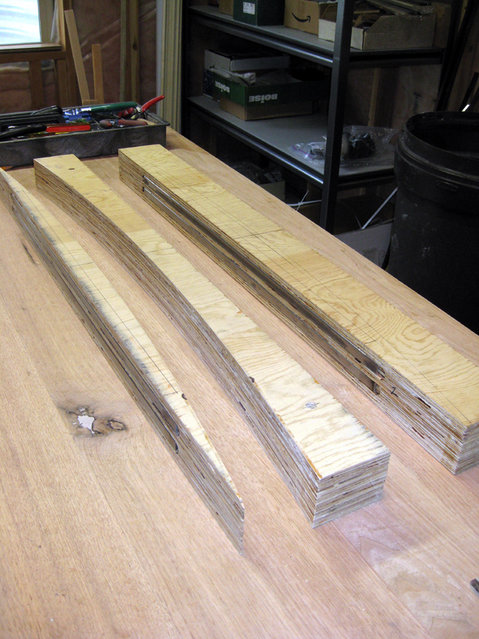
The top parts of this will be the carriage for the router and the bottom are the rails.
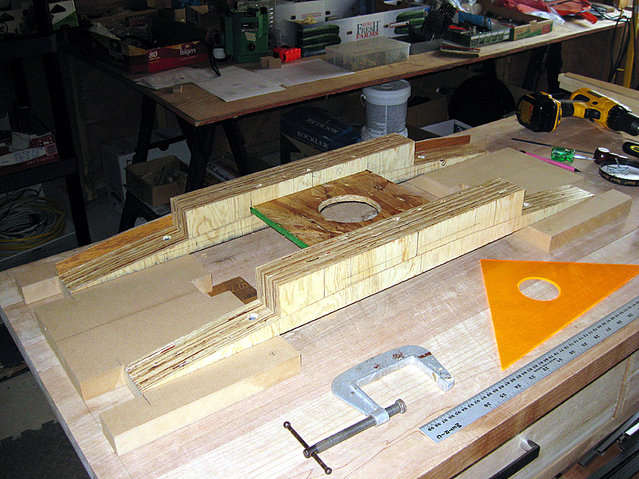
The first test fit of the jig with one edge guide attached.
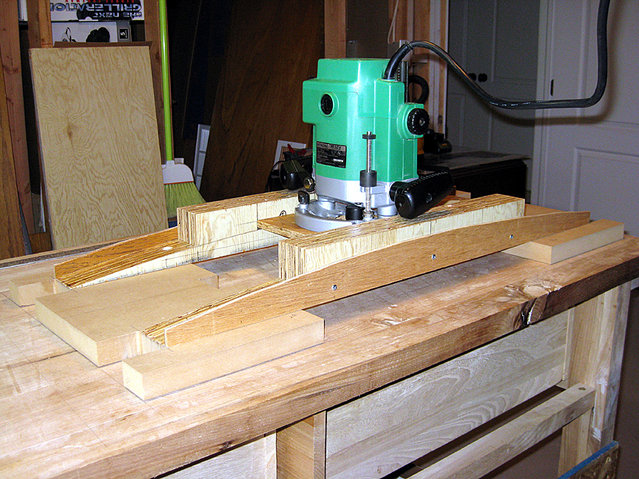
With router attached and all mating surfaces sprayed with lacquer and waxed. It slides very well back and forth.
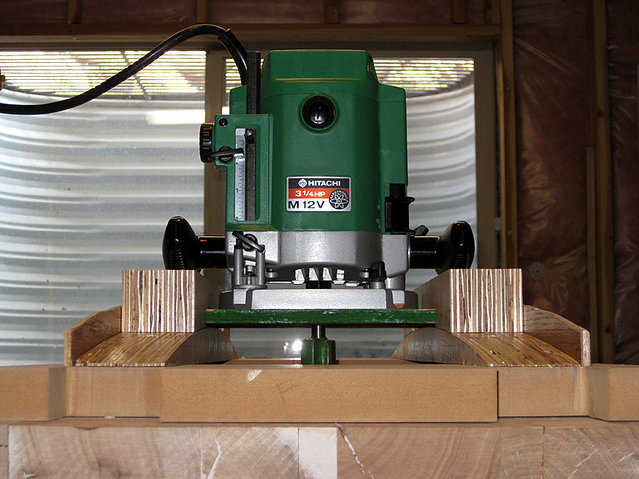
The router is the venerable Hitachi M12V at 15A, 3¼HP. It will accept a ¼" or ½" shaft bit and weighs in at 12.4lbs. The bit is a Grizzly double fluted straight bit, ½" shank, 1¼" cutter diameter and 2⅝" OAL.
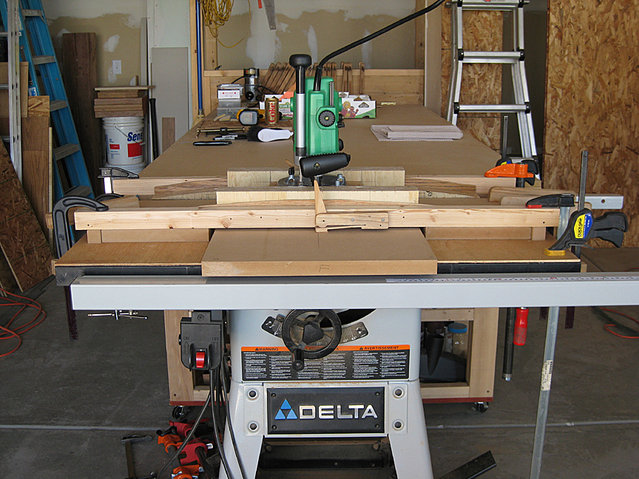
This was a test layout of the jig setup on the table saw. I used the table saw because it has a perfectly flat surface to keep things all on the same plane.
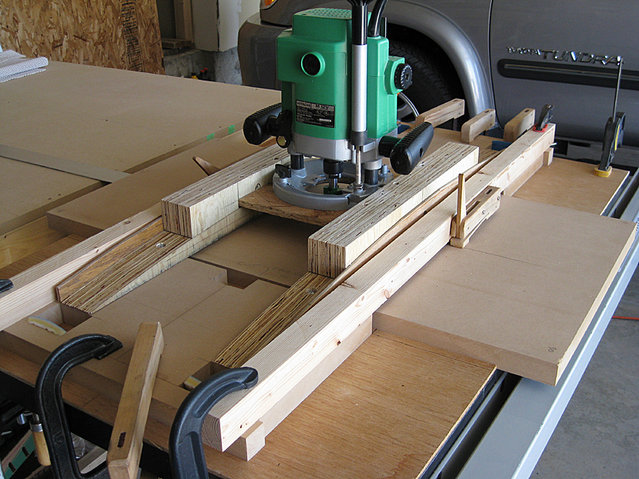
As the router is slid back and forth, the side being cut will be pushed under the router. I used the top half of some cam clamps to act as hold-downs to the side piece.
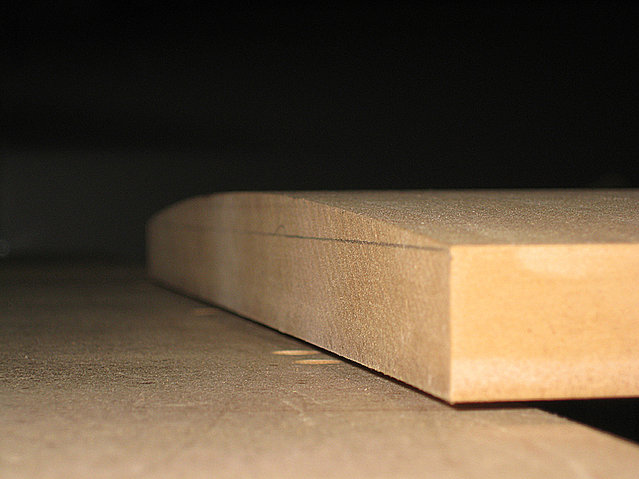
It produced a beautiful 9 ft. radius curve. The material is 1⅛" MDF. I removed about 1mm from the apex and that left a ¾" edge.
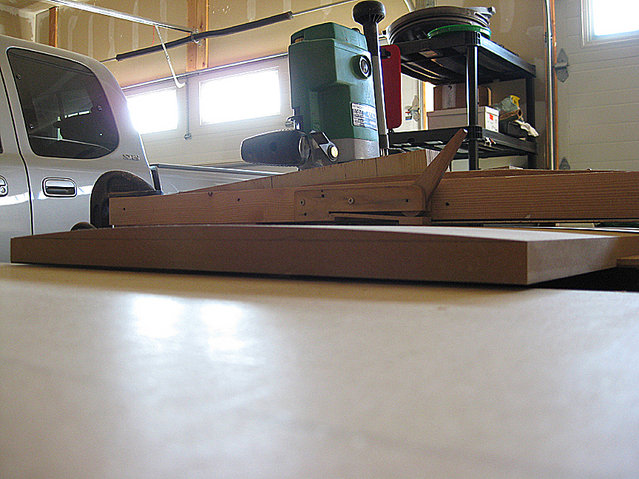
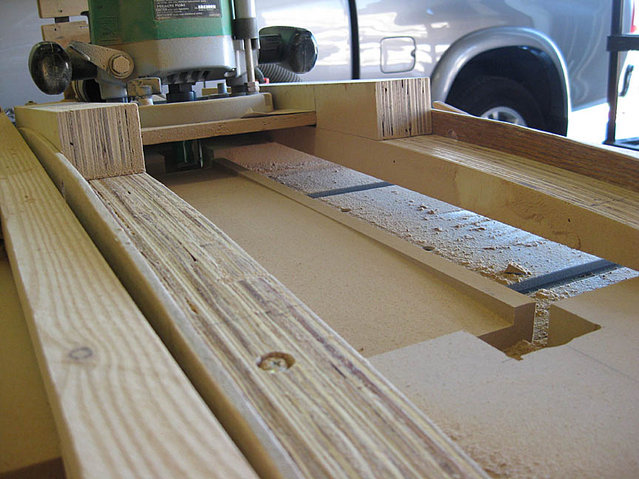
The last ½" still to cut.
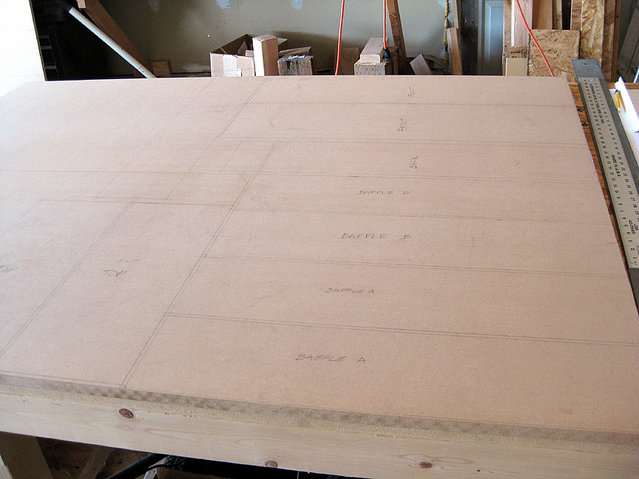
Layout of the pieces on ¾" MDF. I bought the ¾" and 1⅛" MDF from a local lumber yard and not one of the "big box" stores. I don't think the MDF from the "big box" stores is of very good quality.