If Murphy’s Law ever applied to anything it is cords and hoses. And straight edges. Those things hate me. If they had thumbs, they would do real damage to me. As a result of my issues with those things, I have a bevy of cordless tools. My latest acquisition is a cordless router. No, don’t laugh, I did buy one and the quick answer is - Yes it really does work. And I did buy it for this project. Straight edges, I’ll come to that...
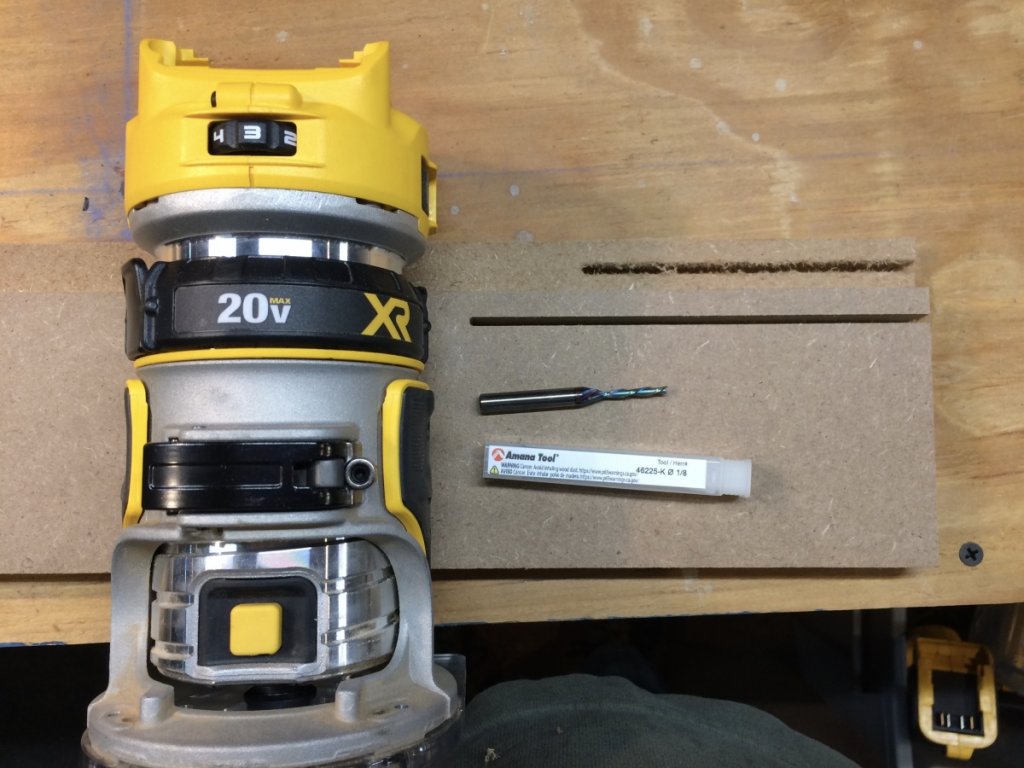
There is a lot to be said for this little thing... First: no cord. Second: it has power
There is a spiral, down cut bit in the picture. The idea for getting this came from from the bits used to make holes in drywall. My thought was this will help to control dust.
In the picture you can see 2 cuts that I made. The really clean one is with the carbide bit in the picture. The nasty looking cut is from a cutter used for drywall. Ya, doesn’t work too well on MDF...
If you look closely at the picture, you will see that the MDF has a relief routed into to it. That is a 3/4”x3/8” routing that I did in a single pass with this router.
The router has speed control; you can see the speed setting dial in the picture. I think the range is something like 16,000 to 24,000 rpm. And it is a real speed control. This thing will hold that speed setting no matter what. No bogging down. It just goes. The downside to that... the 3/4” router bit, doing a 3/8” deep cut will suck a 2 amp-hr battery to zero in about 3 feet of cutting. So, this will be a case of using the right tool for the job. I will likely be using a corded router for these heavier cuts.
However, for using the 1/8” bit in it... I am loving it. It has been used to make the 4 foot long cuts in the MDF with no sweat. I get about 12 linear ft of cutting with that same 2 amp-hr battery.
For cutting I ended up trying two straight edges:
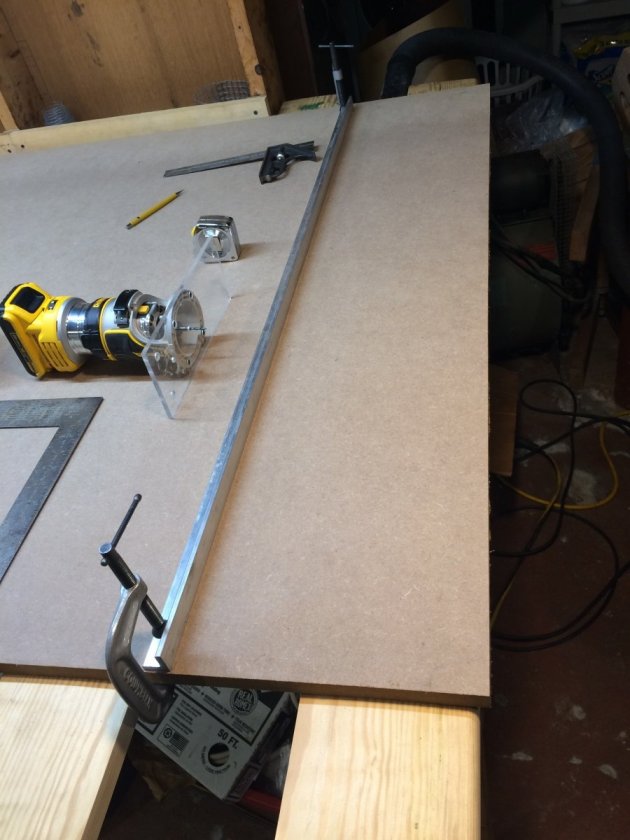
This worked really well. It was really stiff and guided the router nicely. It is a 4’ long piece of 3/16x1x1 aluminum angle. It worked great until I found it was bent and I was on my way to making a bowed version of these speakers. And they would have been bowed to the side, not front to back, which might have been interesting. This isn’t the first time I have had non-straight straight edges. You would think I would have learned my lessen and not just pick something out of the “miscellaneous pile” and use it just because it looks right...

I was able to recover and cut those pieces in to smaller parts.

My second attempt at making straight cuts worked much better... It really is straight
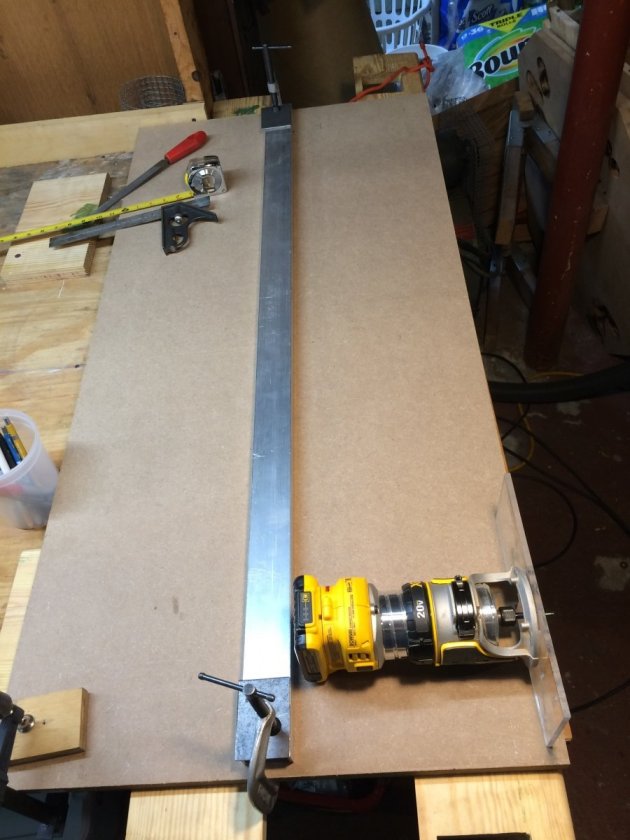
I placed the MDF on sever 5/4 board which raised it up enough to put a shop vac hose attachment under the MDF and in the channel created by the 5/4 boards. This did really well at gathering and controlling dust.
There is a little left over feathering on bottom edge of the cut, which is easily taken care of with a bit of light sanding. Also, the cutter leaves slight bump as it exits the piece at the end of the cut. This I take care of with a coarse file, but if left behind can cause issues with making right angle cuts if it comes into contact with the straight edge of the cutter or layout.