I was going to start this thread after getting a little farther, but thought I'd get some first steps down along with the two photos I have so far.
Quick synopsis:
Building a pair of X-MTMs and a X-CS for our downstairs tv room. Rather than doing the flat packs I'm building both cabinets from scratch for a few reasons:
- The MTM's need to be a little higher due to our listening height
- I want to use this as a means of getting better at woodworking
- It's an excuse to buy more tools
I ordered the parts from Danny a couple weeks ago and, like a lot of you, just waiting on some back-ordered parts.
My skills:
I'm not afraid of tools and using my hands. I spent much of my life doing small boat repair (dinghys, racing shells and such), so I know my way around a sander, carbon, and epoxy. I've also taken on a few amateur carpentry projects around the house for things that we're fine with being not quite professional. Woodworking is a different animal, however, so I'll need to muddle through it.
My plan for the cabinets are to dado and rabbet most of the joints except the front baffle which will be a butt joint with dowels (I'll get into the reason for that later). The dado's and rabbets will be a new challenge, but I think the increased cabinet strength and easier assembly (fingers crossed) will make it worthwhile. Accuracy will be everything. I've pored over the plans countless times and drawn it out in Sketchup to make sure I have a good understanding of how the pieces are going to fit together. This may be old hat for the accomplished woodworkers in this forum, but it will be new territory for me and I'm a little nervous about it.
After watching some of Peter's videos, I was pretty selective with my choice of MDF and had to call around to multiple lumber yards to find high quality stuff to use. They even had 4'x10' sheets which allowed me to use two sheets rather than three. After spending even just a little time with it, I can see why MDF quality important and I can honestly vouch for it. It's true 3/4" thick, cut 1" over on both axes (49"x97"), tough, and great to work with (clean cuts with minimal tear out). Downsides, it's even heavier than box store MDF and I actually cut myself on one of the dado'd corners because it was so sharp. At $45 for a 4x8 sheet, it's not really that much more expensive than the cheap stuff, and the 4x10 sheet was only $10 more at $55.
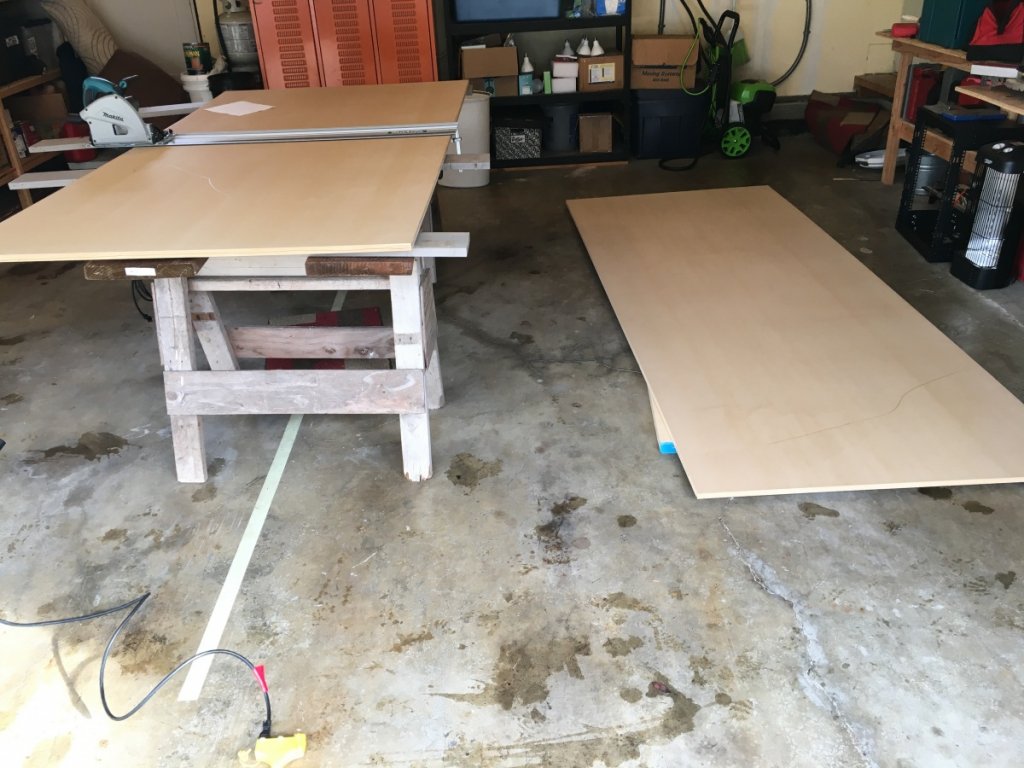
My steps so far:
- Cut down the panels to usable size
- Rout out the dados and rabbets before trimming out the parts.
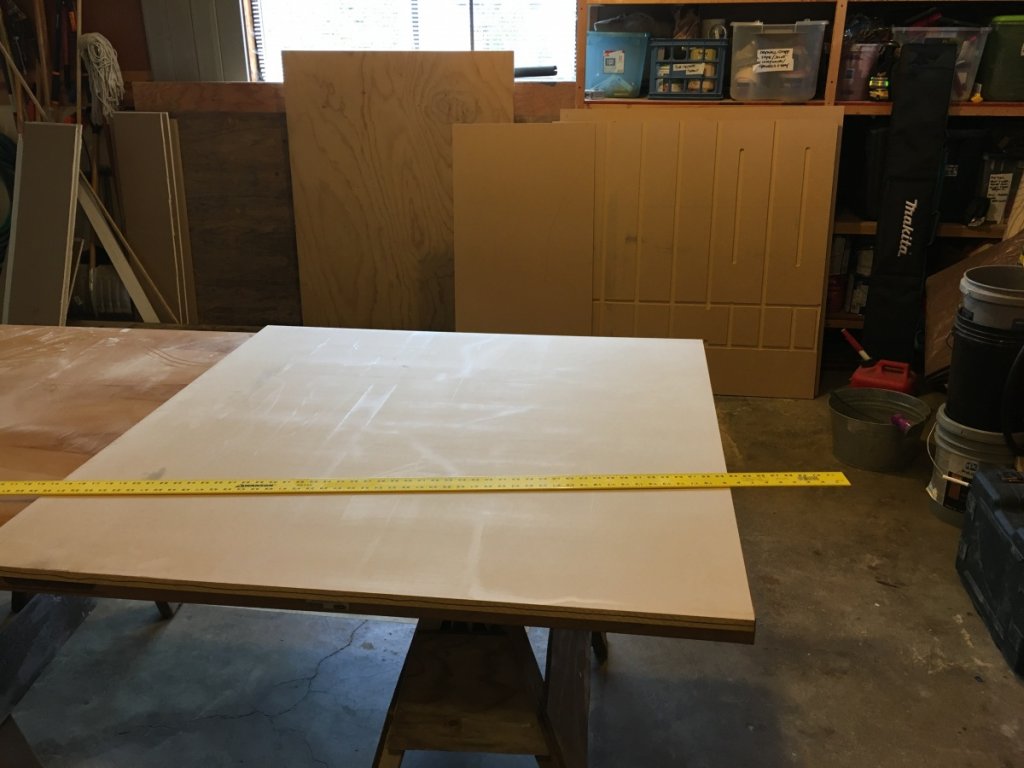
Pic above shows one sheet that has the front, back, and sides of one MTM. The sheet on the table is about to get the same treatment for the other speaker. Top and bottoms will be rabbeted and cut out of the panel leaning in front of the first piece. The braces and X-CS will be cut out of the sheets behind the dadoed sheet.
I didn't get nearly as far as I wanted over the first weekend, but a couple early mistakes made me slow down a lot to make sure that each and every cut and router pass was dead on.
Things I learned/opportunities for improvement/screw ups:
- When doing my initial breakdown of the sheets I wrote down one number wrong, it was a 1 instead of 11. So...yeah, it was 10" off. Not the end of the world but it forced me to revamp most of my cut list.
- Know and understand the difference between a standard cut and climb cut with a router. Due to inexperience my first dado ran away from the fence. Luckily it's in an innocuous spot and can be fixed. After that I spent most of the morning making a more robust dado jig that ended up saving a lot of time and heartache in the long run.
- Almost forgot another. Keep track of the factory edges. I thought I was referencing a factory edge on my first round of dados only to find I was using a cut edge. I even ran a sharpie around the entire perimeter of each sheet before cutting them down to minimize the likelihood of this. Luckily my track saw cut was within 1/32, so I don't think it will have much effect. Bullet dodged.
I'm sure I'll learn more as I go along and should have more progress after this coming 3 day weekend.