Above Michael gives the matter of fact updates on his health issues. Presently his status remains good to go and firing on all cylinders. It was quietly tense waiting the late October 2022 procedure from which the good news came, no stents required.
What I want to share today is the concurrent story of how this workhorse of a man I proudly count as a friend didn’t miss a beat during that time. Far from it as events transpired between visits to the cardiologist, testing, and waiting the fateful morning at the cath lab Michael installed a major upgrade in his shop. I was pleased to help lift, tote, screw, and take a few pics.
Early October and that’s Michael in the rented forklift removing a Shop Saber 23 from the freight delivery truck. The forklift is not optional, shipping weight for the ’23 is 1100 pounds.
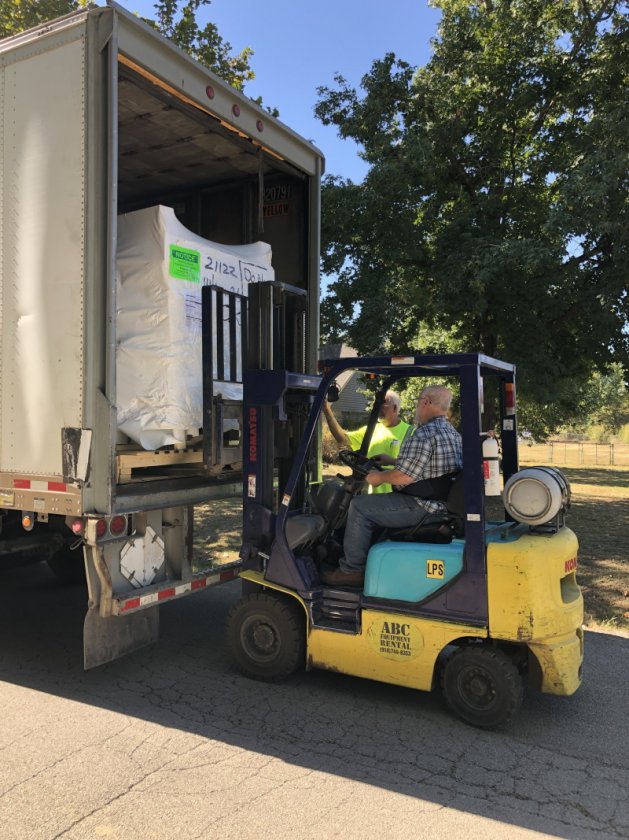
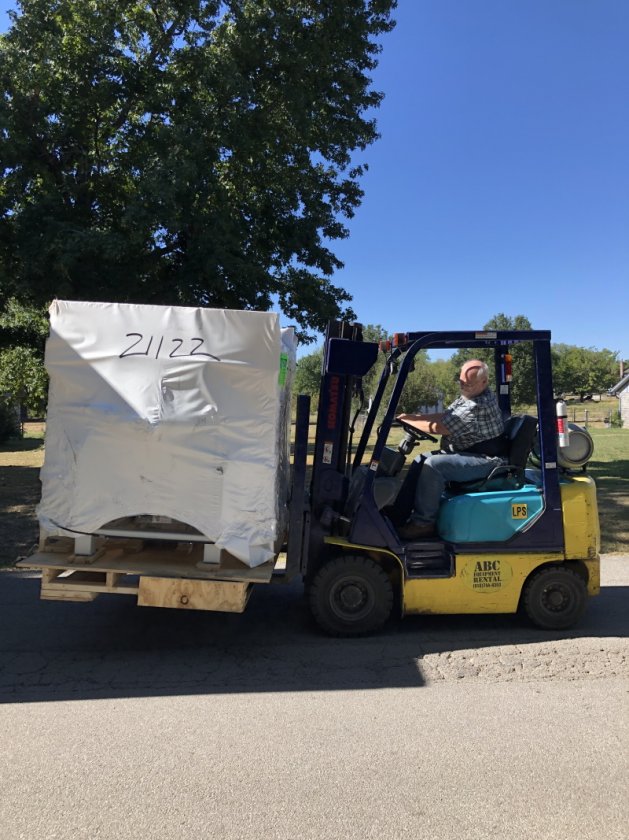
With the pallet safely on the driveway, shrink-wrap removed, and contents inspected time for Michael and Norman to get busy as riggers moving the beastie into the shop. For my fellow CNC nerds who are curious the box strapped to the machine’s bed is the dedicated PC that will send G-code to the Shop Saber 23. The black device strapped to pallet is the high power vacuum pump that powers the vacuum chuck system Michael optioned.
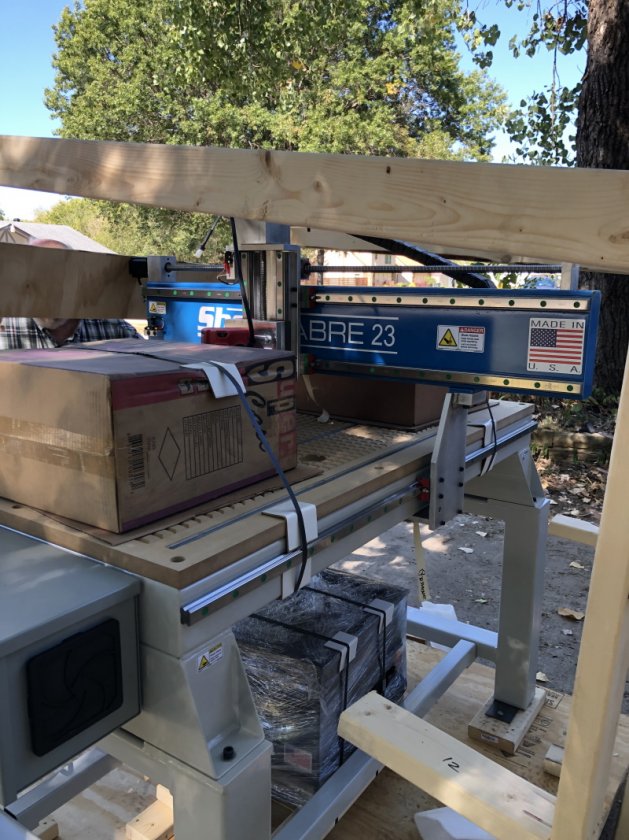
Off the pallet and with fork-lift and then men-push the CNC arrived at its designated location in the shop. Michael is reading up on next steps including leveling, powering (both 110 & 220 VAC required), and connection of PC to stepper motor control electronics.
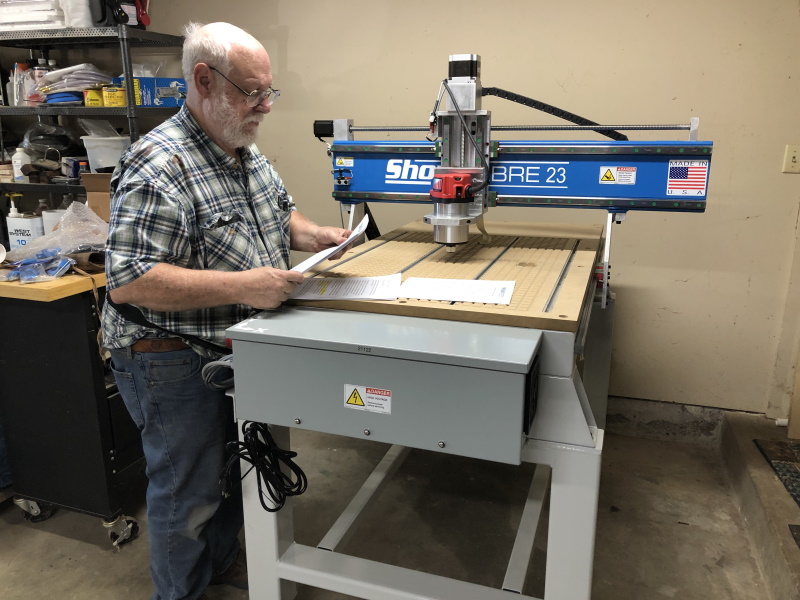
This long day getting half a ton of CNC into the shop happened the day before Michael’s last pre-op visit to the cardiologist! Delivery schedules for equipment do not take health issues into account. In hindsight it is also good we forged ahead during the waning days of fall in Oklahoma. I am really glad all this work was not done in freezing winter temperatures.
Dust collection is vital for wood working shops and all the more so when a production capable CNC installation is added. Thus in parallel we worked on installing this beast.
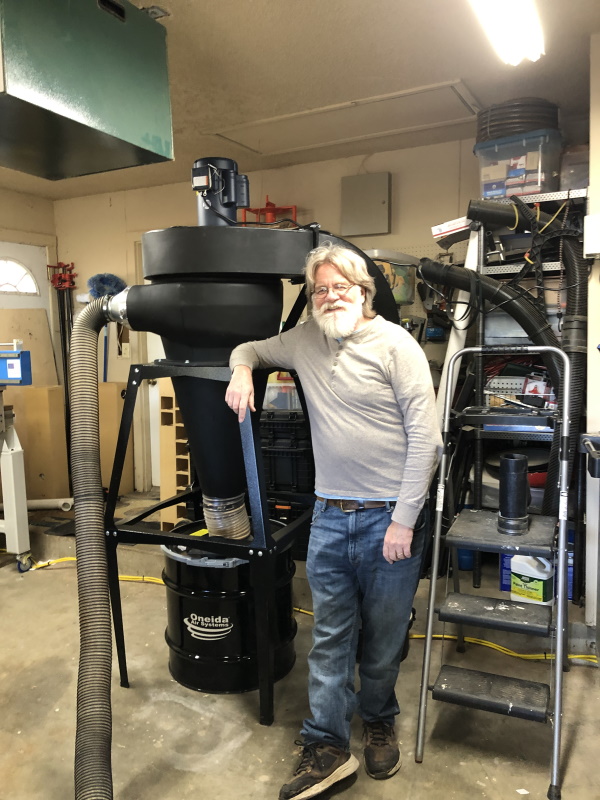
When this photo was taken with me standing next to it for scale the work had just begun. Soon a full ducting system based on 7” feeder piping with four gated branches to tool stations arrived. All that was run across the ceiling with drops to both sides of the shop and a central multi-tool location. I am very pleased to report we got it all hung with no ladder falls, just sore muscles after a long fulfilling work day.
With CNC and dust collection in place time to calibrate and make the first cuts. At this point we split our efforts. Michael largely returned to work on the speaker build commissions queued up while I used my CNC experience to help us up the Shop Saber’s learning curve. Many ways to do CNC, for now the work flow processes CAD input using Aspire CAD to program toolpaths which are output as G-code using the Shop Saber 23 post processor. That G-code is loaded into the control program on the PC interfaced to the Shop Saber 23. Following picture is the control interface with preview/progress display showing cuts ready to go.
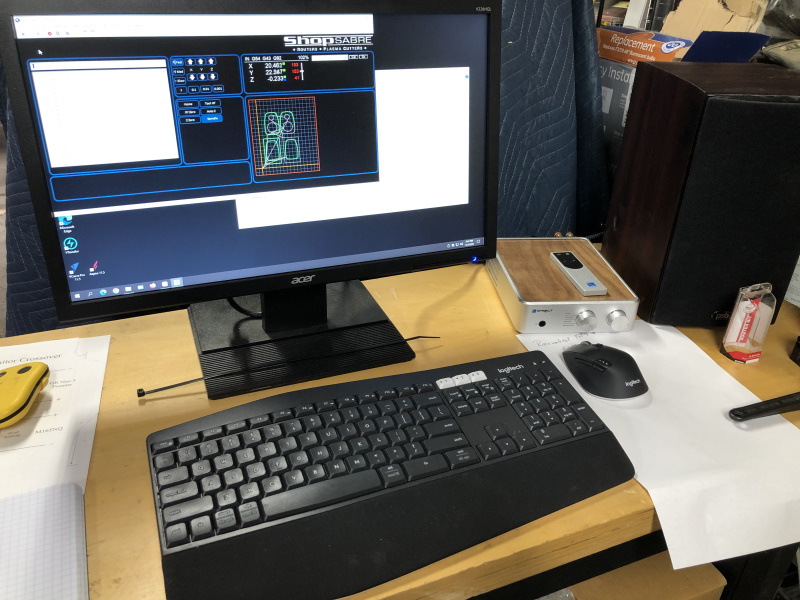
First cuts making some baffles. Keeping it interesting with added learning this job includes two sided machining. Getting the resulting flips synchronized between CAD, the material, and CNC was a great learning experience to get out of the way.
And the resulting parts cutting on the Shop Saber. The machine is cutting when this picture was taken. I am (pardon the pun) blown away by how effective the dust collection Michael invested in is performing. If you have been around CNC cutting wood and especially MDF you will agree to be impressed at how little sawdust remains on the work in progress.
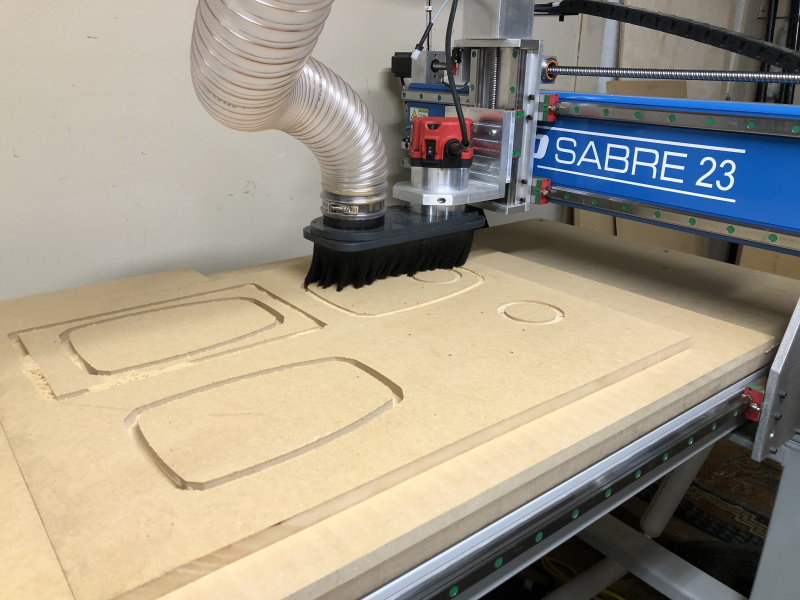
And soon one has the parts to build a pair of speakers. This is an experiment based on the X-LS Encore platform. Details will be posted once a bit more progress is made.
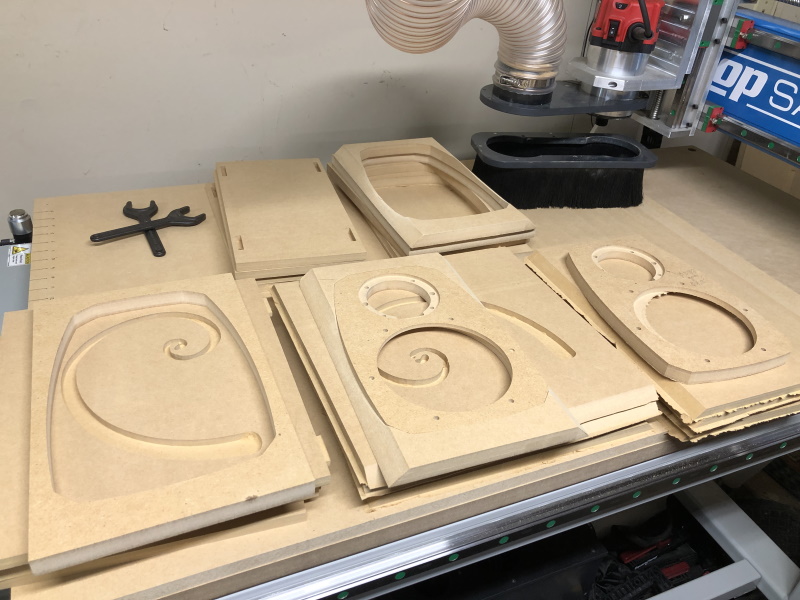
I will close asking my fellow GR Research fans a simple question.
No Rez, what can’t it do? Until his new shop gets past the local bureaucrats Michael’s workspace is shall we say ‘tight’. The Shop Saber 23 weighs 1,000 pounds because it is made out of solid steel. The gantry is a bump hazard in the confines of this compact shop. Bump into that and there is no give, only
ouch. Solution?
No Rez to the rescue! 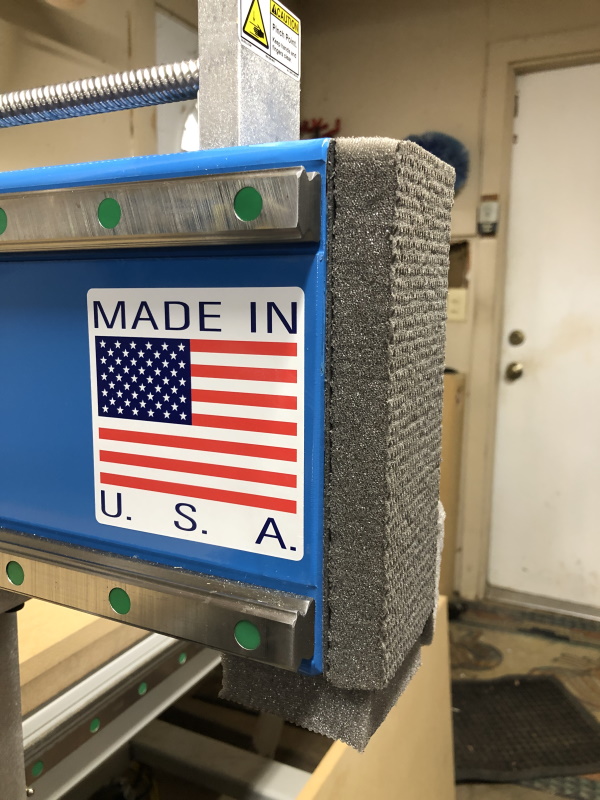