Some further updates and progress (albeit slow):
Veneering in progress ... Titebond II seems to have worked well.

Danish oil going on:
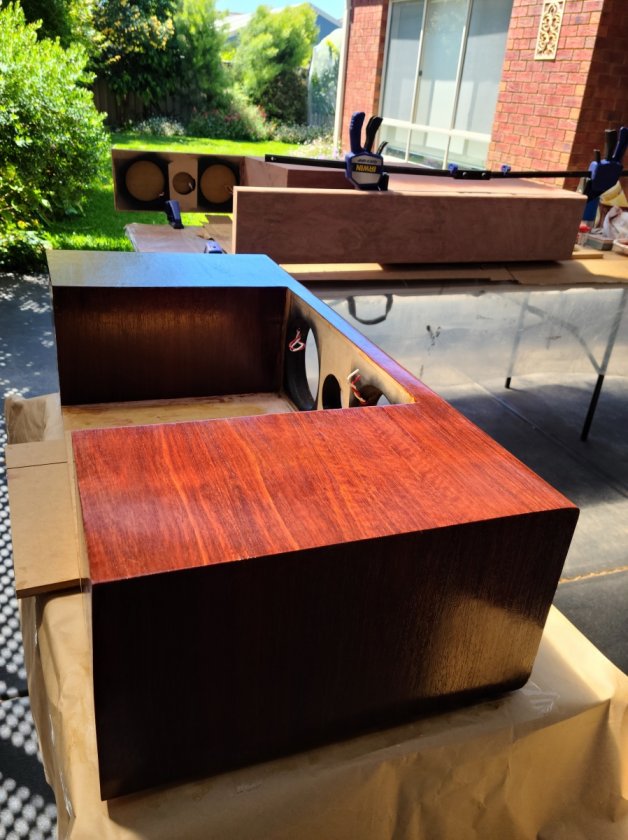
X-Voce speaker wiring - I went with carded lambs wool for the fill.
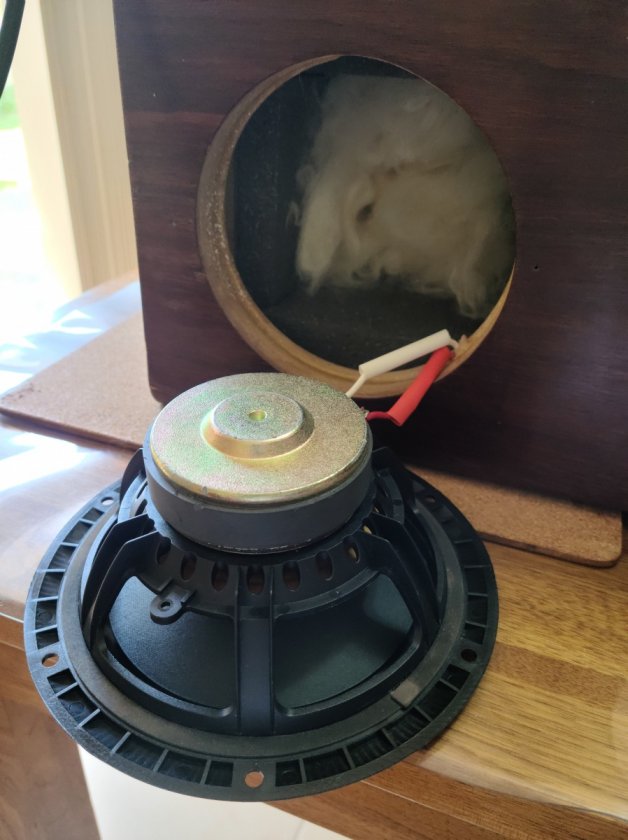
X-Voce cross-over in place - this was the most fiddly bit - not a lot of room to get the screws in to hold the cross-over in place.....
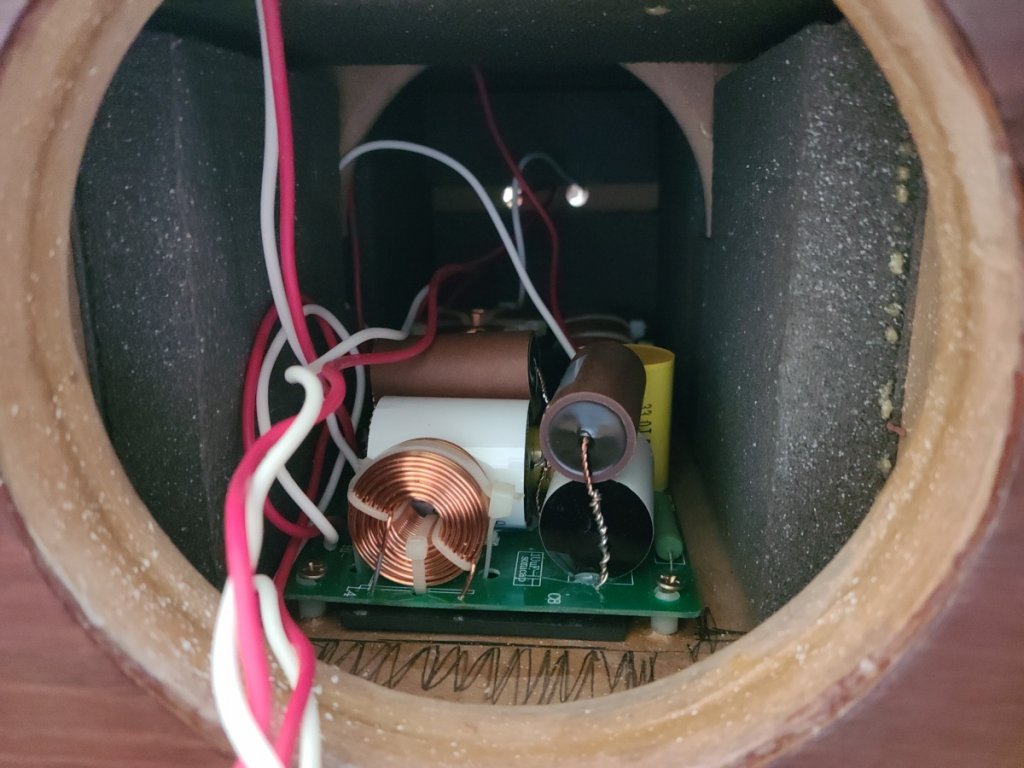
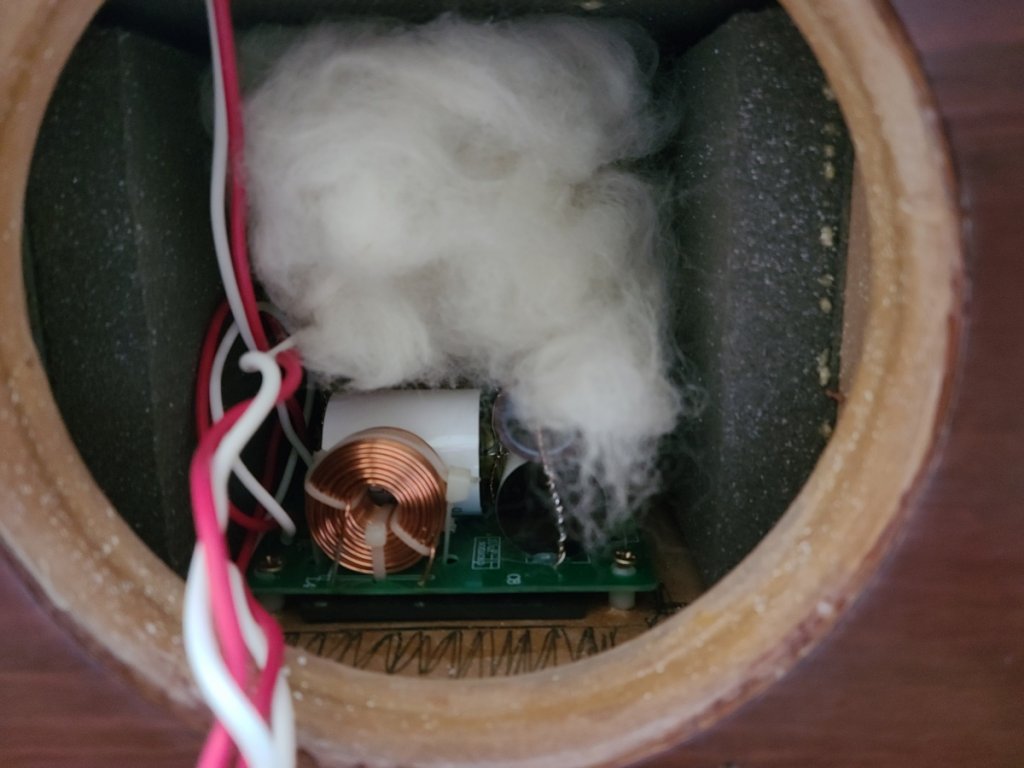
X-Voce up and running. A BIG step up from the Q-Acoustics centre I had previously.... I need a new media centre. The Dayton Audio HTA100BT amp is my first 'tube' amp. I'm impressed when it feeds my existing speakers. I'm really excited to hear how well it sounds feeding my X-Statiks.
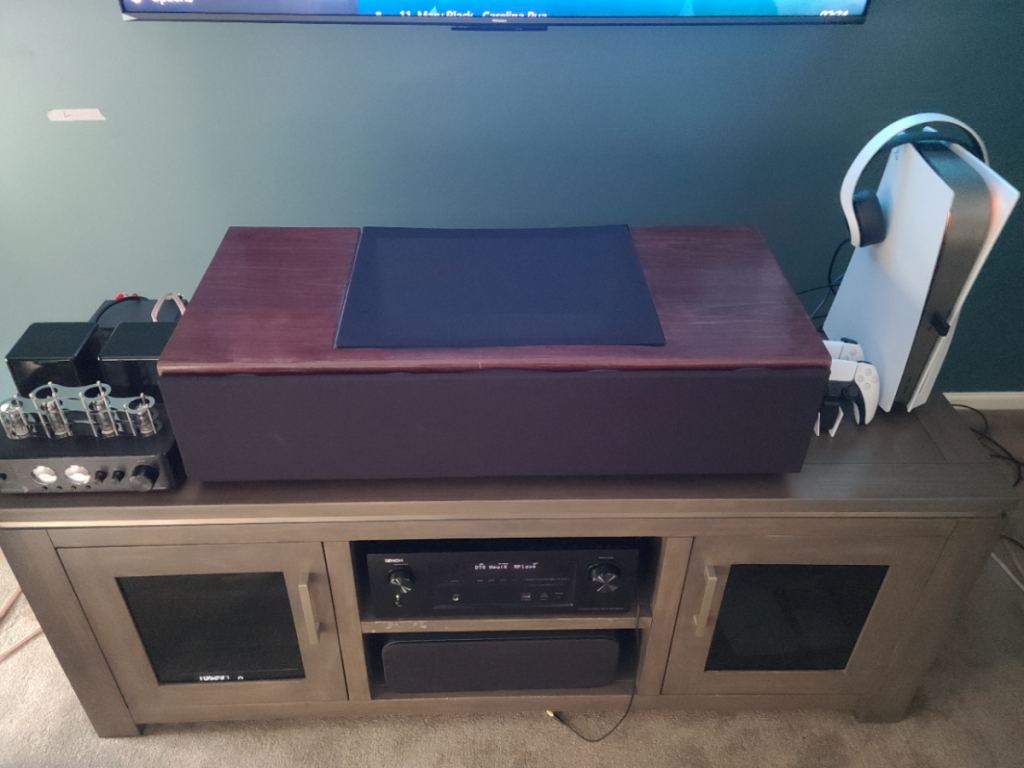
My wife wanted a cover over the OB section, so I knocked up a quick 'dust' cover. It's just resting on the No Rez in the OB section, but seems to do the job. I'm still going through 'burn-in' - about 40hours on the clock so far using the 'fry baby' file at night and music / movies during the day. So far - I'm very impressed.
5th coat of polyurethane over the Danish oil on the X-statik. I'm waiting for it to fully 'cure' before polishing and buffing.
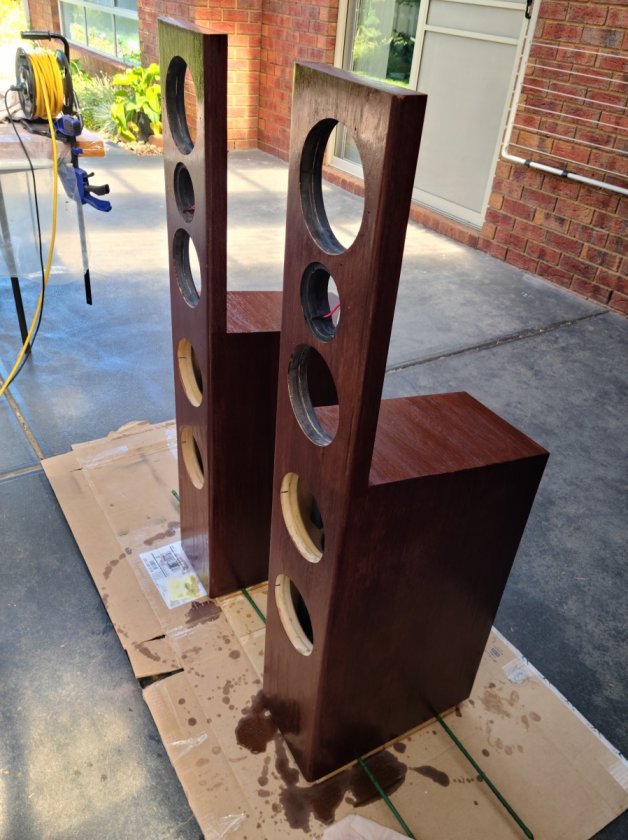
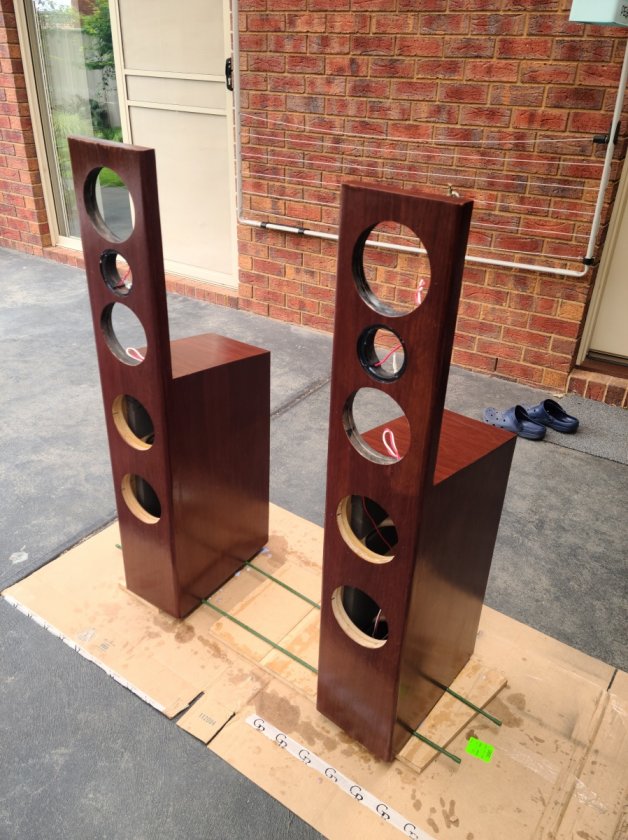
I can't wait to hear how it all comes's together. I'm also planning to build some folded well diffusers for behind the speakers.
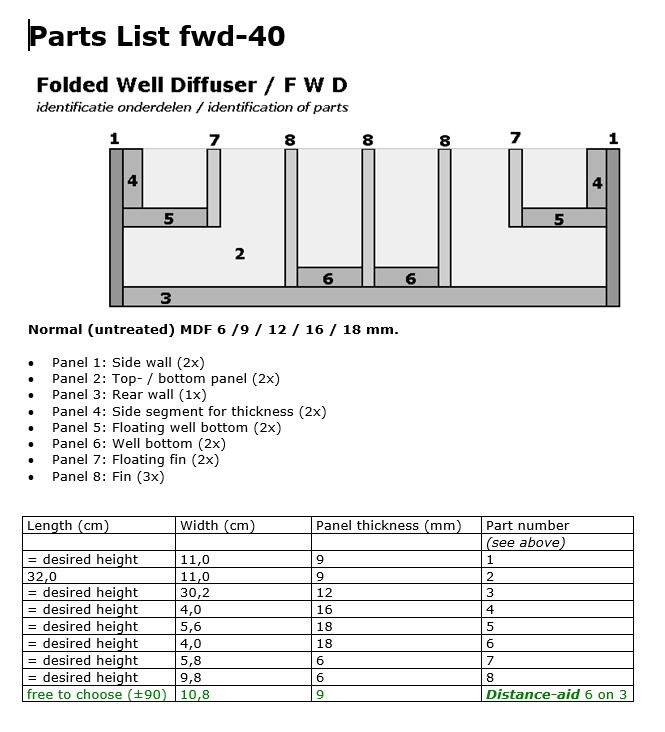
Then OB subs ...... then rears

I've got to say, I'm really enjoying the journey AND the current outcome.

D