Hello Everyone,
It's been long time since I've been active here. Good to see the spirit still going!!!
I wanted to post a few pics of my build from the el'cheapo exciters from PE.
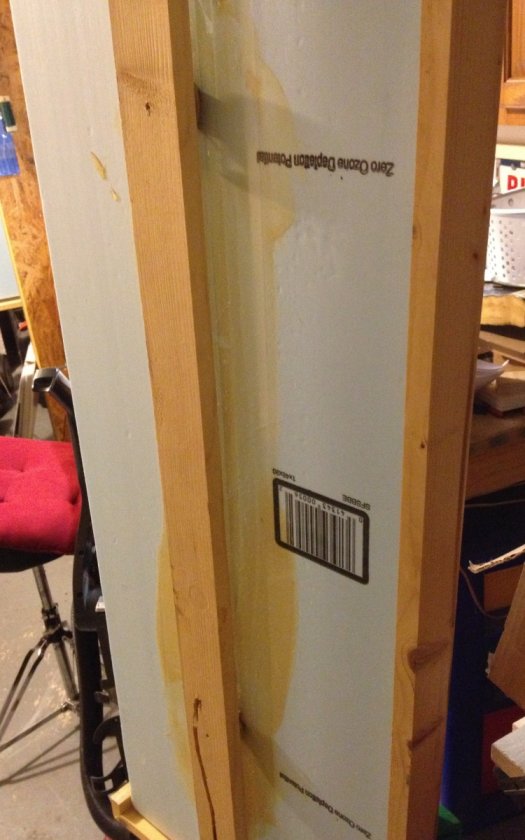
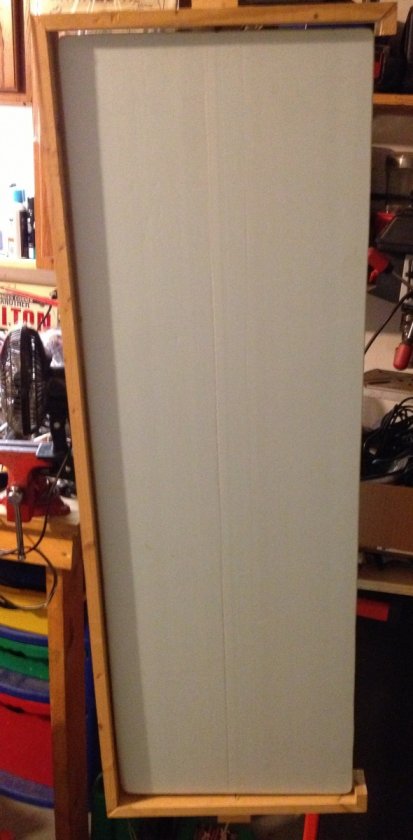
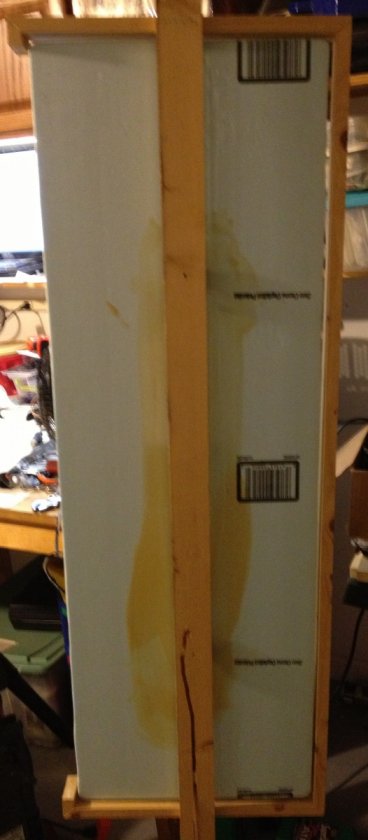
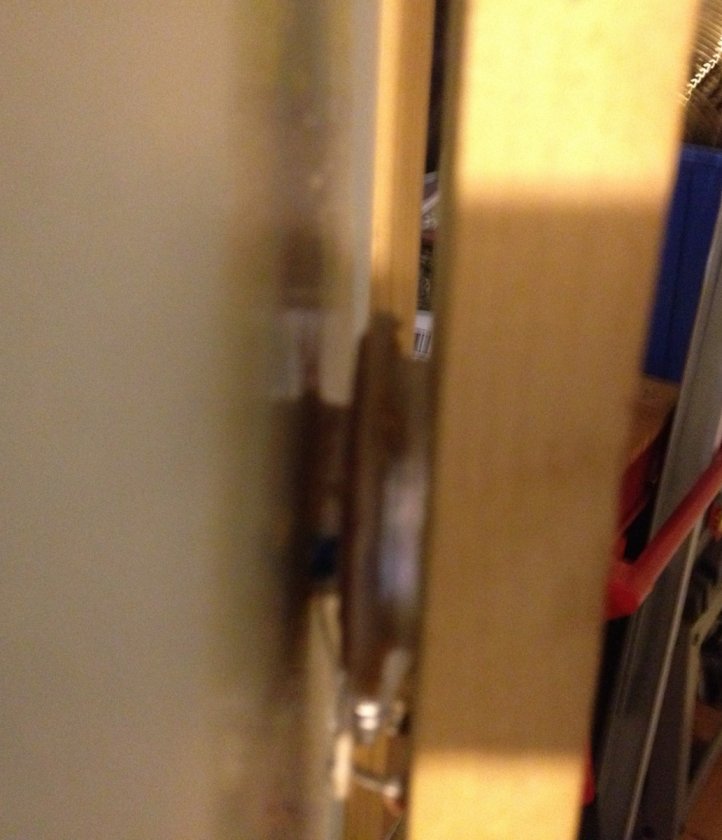
So as you can see I'm using EPS for the panel material. My frame is simply 1x3 with a 1x3 support spline. I have the exciters and speaker wires recessed into the spline. I plan to "clean up" my prototype and make it more presentable by wrapping speaker grill cloth from the front to around the back and stopping at the spline. I like this design the best as you can either mount the whole speaker to the wall, or you can easily convert it to free standing with a floor base design. At the moment I have it suspended to the ceiling with rubber tie down straps...lol
You can't see in these pics, but I have some closed cell rubber strips that I cut from a sheet. I basically have the panels tensioned at the center top and center bottom. This effectively makes the panel free floating and relieves any stress to the exciters. I've never had any exciter, or voice coil drop by using this design. Plus the rubber is flexible enough and light enough to not impede the EPS's sound characteristics.
Some may ask why one side of the frame is cut off....well, it was a full square frame originally! But after the first minute of listening I realized by blocking the edges of the EPS the frame was killing a lot of the ambience of the panel. I just sounded like crap. To experiment, I cut off one of the sides and the speaker panel came back to life.
I've learned you CAN NOT block the edges of the panel!! If you block the edges you will not get the 170 degree sound field that these speakers are capable of.
As for the mounting of the exciters to the EPS panels, I've used G/Flex epoxy by West Marine. This stuff is great!!! It will not melt the EPS and it will accurately transfer the sound from exciter to panel!!!
I know a lot of people still use the 3M foam tape, which they've had great success with, but I feel is only good for testing purposes only. I don't see it as a permanent fix or solution. Plus I would venture to say the 3M foam tape impedes the overall sound. By using foam it will dampen the energy transfer from the exciter to panel.
I feel you must have a solid bond, but slightly flexible, between the two. I have found that G/flex epoxy provides this and have had great success with it!!
I noticed this thread is talking a lot about using 5mm wood for the panel material. I think that is a very viable idea.
I would imagine that that material would provide a warmer, non-harsh sound. Characteristics that most EPS is noted for.
If anyone hasn't already done it... what about laminating the wood panel with a thin EPS board? I would think that the EPS board would not only help make the wood more rigid, but also help amplify the woods overall tone and sound. The best bonding material to sandwich the wood and EPS would be epoxy...of course

Has anyone tried this already?
Anyways. Its good to see everyone still at it. I wish I had more time to get back to this project. I find the wood panel an intriguing idea!!
Zygadr...Glad to see you're still active in this arena!
And yes, I'm still working on my driver design(if you remember from a year or so ago..lol). I have an even better idea and path than the one I originally shared with you.
I've been slowly gather materials to make a prototype. I believe it will be a good success if I can pull it off!!!
Only time will tell..hehe
Hope to get back more often!
Peace