Oxide Removal for Stranded WireOne of the hallmarks of Hapa Audio cables is their pristine performance across the entire frequency spectrum. While many cable manufacturers use wire straight off the spool—either bare or pre-coated with a dielectric layer—this approach has a critical flaw. Even if the wire is labeled as “99.999999% pure copper” or “99.9999% pure silver,” oxidation can quickly render those impressive purity numbers meaningless. It’s an unintentional false advertisement, promising more than it actually delivers.
Like all audio components, bare wire often sits in storage for months or even years before being used. During this time, it’s exposed to air, handled during shipping, and subjected to conditions that accelerate oxidation and contamination. Left unaddressed, this degradation compromises conductivity, dulling nuances, restricting dynamics, and rolling off the frequency extremes.
The ugly truth.
That burnt orange color in the above photo is oxidation on a stranded wire, fresh cut out of it dielectric. This oxide layer is present on all copper wire unless the cable maker removes this layer, the resulting sound quality will always be suboptimal.
Why Stranded Wire?Through years of R&D, I’ve uncovered several key factors that dramatically impact sound quality. The first is obvious: a pristine surface on high-purity wire is essential. But just as important is another factor that might surprise you: surface area. The larger the effective surface area, the better nuance, detail, and all other performance-related improvements become. This is because of skin effect. Skin effect is the tendency of signal current to concentrate near the surface of a conductor rather than being evenly distributed throughout its cross-section. This effect is most pronounced at higher frequencies, where signal transmission is concentrated at the surface of the wire, but it influences performance across the entire audio spectrum. So, in order to maximize the benefit of skin effect, it is important to increase the total surface area of the signal conductors while decreasing the diameter of individual strands.
Let's crunch some numbers to get a better idea of what we're discussing.
The equation for the surface area of a cylindrical object (like a wire) is:
A = 2πrL
Applying this to wire:* A solid-core 20 AWG wire, 1 meter in length, has a surface area of
25.5 cm².
* If we increase the gauge to 18 AWG, the surface area only increases to
32.2 cm²—a mere 25% improvement, and at the cost of increased stiffness. Subjectively, it offers almost no sonic benefit.
Now, let’s compare this to stranded wire. By dramatically reducing the diameter of individual strands and using multiple strands, we achieve a staggering increase in surface area.
For example, consider a 23 AWG stranded wire with individual strands at 0.1mm diameter. The total surface area jumps to an incredible
103.7 cm²—
a fourfold increase over the solid-core 20 AWG wire, yet with a smaller 23 AWG design.But there’s a catch. While stranded wire offers a major advantage in surface area, it also presents a serious challenge—oxidation is even more problematic in stranded designs than in solid-core wire. Cleaning it properly is far more difficult, especially with hair thin stranded wire and traditional polishing methods simply won’t work.
The Oxidation Problem in Stranded WireTo unlock the full potential of high-purity wire, meticulous in-house cleaning is essential. There are two major reasons for this:
1. Oxidation reduces conductivity, which robs the signal of clarity, detail, and dynamic range.
2. Oxidation worsens over time, leading to further degradation and long-term performance loss.
In my previous designs, I tackled oxidation by sanding, polishing, and cleaning the wire using proprietary techniques. This approach worked exceptionally well for solid-core wire, producing ultra-clean, ultra-pure conductors that significantly improved sound quality and tonal balance. However, these same methods were impossible to apply to highly stranded wire.
While solid-core wire can be polished directly, attempting to do the same with stranded wire—composed of many delicate individual strands—would inevitably destroy it.
A 10-Month R&D ChallengeWhen Brian of Charney Audio approached me with a challenge—creating a stranded wire high-efficiency speaker cable with an Aerogel dielectric—it seemed straightforward at first. But once we examined the details, it became clear that we were setting out on an incredibly ambitious endeavor.
This wasn’t just any stranded wire. Each strand was a mere 100 microns thick (0.1mm)—comparable to a human hair. Here’s a microscopic view of a single strand next to a human hair for scale:
Two months into relentless trial and error, frustration set in. Every attempt to design a new method to clean the wire properly resulted in failure. At one point, I found myself staring at yet another ruined batch, my makeshift polishing equipment tangled in a mess of broken strands. It was a moment of defeat.
Then, a rare insight struck me: walk away. Stop forcing a solution that isn’t working. Sometimes, discovering what not to do is just as valuable as finding the right path forward.
The BreakthroughStepping away was the best decision I could have made. A few weeks later, inspiration struck like a lightning bolt:
Instead of manually polishing the wire, I could design an immersion cleaning process—one that would remove oxidation without physical contact.
Some of you may have already thought of this. If so, hats off to you!
Determined to make this idea work, I dove into studying the chemistry and engineering required to make this technique possible. The result? A high-tech cleaning process developed entirely in-house designed specifically for removing the oxide layer without damaging or reducing the diameter of the wire. This process represents the pinnacle of almost an entire year of research and development. The proof is in the results. Here are unaltered before-and-after microscope images of stranded wire cleaned using my new proprietary method:
Before
After
Before
After
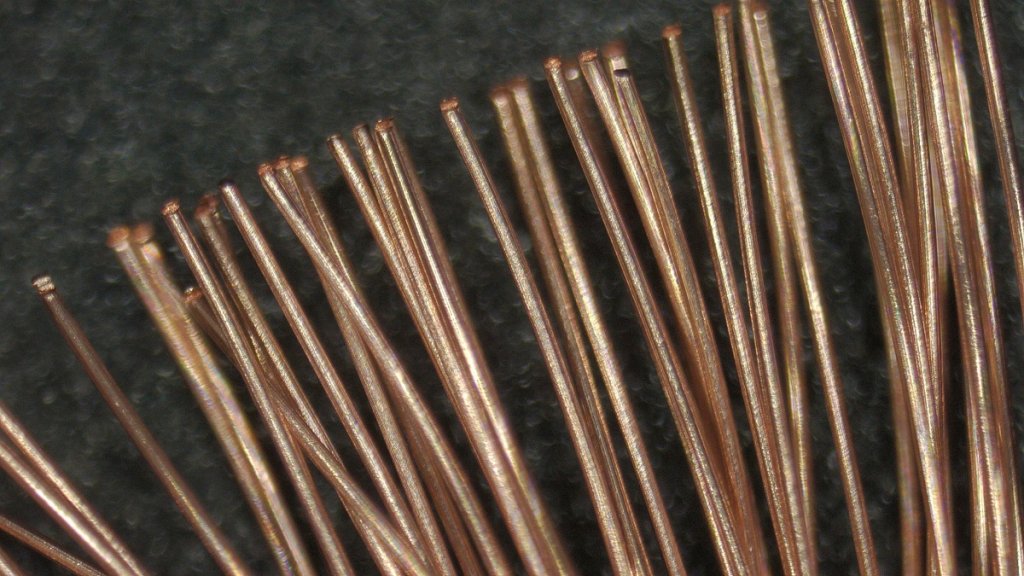
Note the complete lack of burnt orange coloration in the 'after' images. This is evidence of the complete removal of the oxide layer inherent on all wire.
The months of R&D were worth it. This breakthrough allowed me to finally harness the full potential of stranded wire when paired with our patented Aerogel dielectric. But there were still hurdles to overcome.
In my next article, I will discuss how I integrated Aerogel dielectric with stranded wire design...