So I seem to have taken up another project that is beyond my skills and my time, a garage sale Thorens TD126 Mkii. It seems to be in pretty good shape - it runs anyway.
I’ve managed to partially take it apart.
My first question is, does anyone know how to undo the strain relief shown in the attached photo? I’m baffled. I’d rather not just break it open, but I’m on the edge.
So here’s my grand plan.
1. I’m going to have the electronics sent to someone to re-cap everything, as I’ve read that the caps go with time.
2. I’ll set aside the arm and armboard. I’ll keep an eye out for a used VPI tonearm or something – I’m partial to unipivot.
3. I’ll make a custom armboard using CLD, with sheet aluminum on the outside and maybe a mix of closed cell foam and MDF or hardboard, like a mini Symposium shelf.
4. Remove the power supply from the bottom metal chassis (see photo) and put it in a separate box with an umbilical cord to the table. It just can’t be good having a transformer coupled to the metal chassis on which the sub-chassis springs sit. Maybe I’m wrong, but that doesn’t seem right.
5. Since, without the power supply, the chassis will be straight sheet metal with a few cutouts for the motor and the spring adjusters (see photo), I’ll glue closed cell foam to the metal chassis and effectively turn the bottom into a Symposium Svelte type shelf, I’ll put sheet aluminum under the foam, then ball type footers.
6. I’ll make a new plinth that has a gap so that it doesn’t touch the chassis. It will just be decorative.
My thinking is that this will make for a lightweight chassis that is constrained layer dampened, rather than a chassis with a transformer that is just screwed into a wooden frame. I know from my experience with an LP12 that this design typically favors lightweight shelves, so why not a lightweight but rigid chassis. I will cut holes in the foam and metal sheet to be able to access the motor and adjust the springs.
Any thoughts as to this strategy? Obviously it will no longer be a stock vintage TD126.
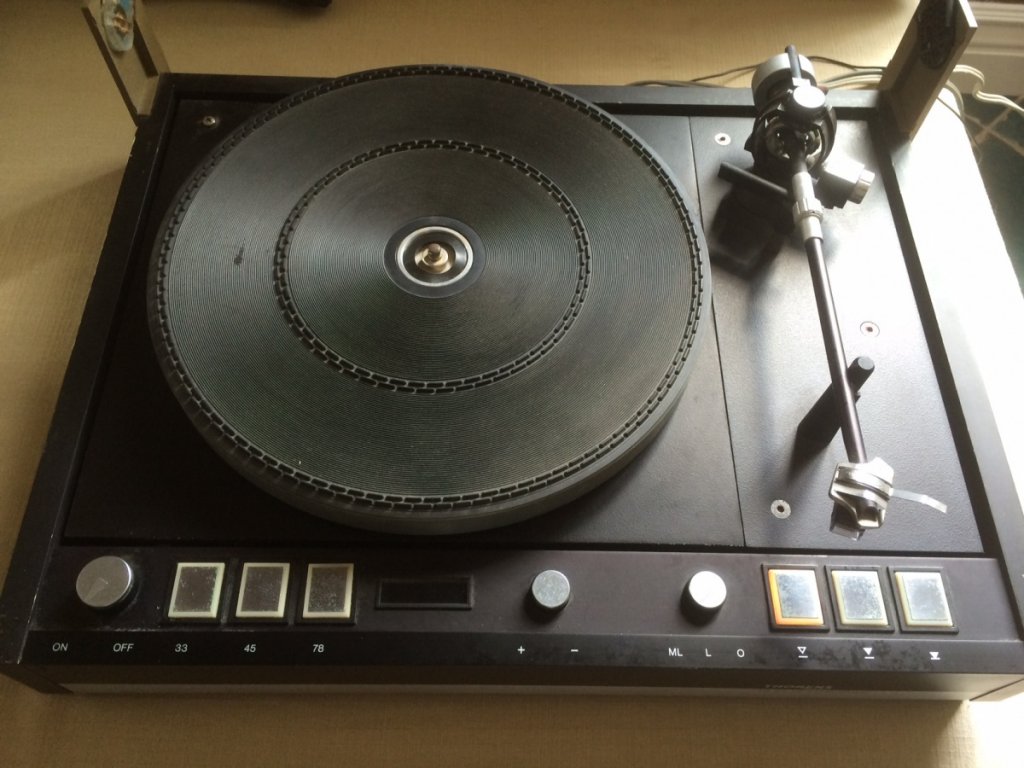
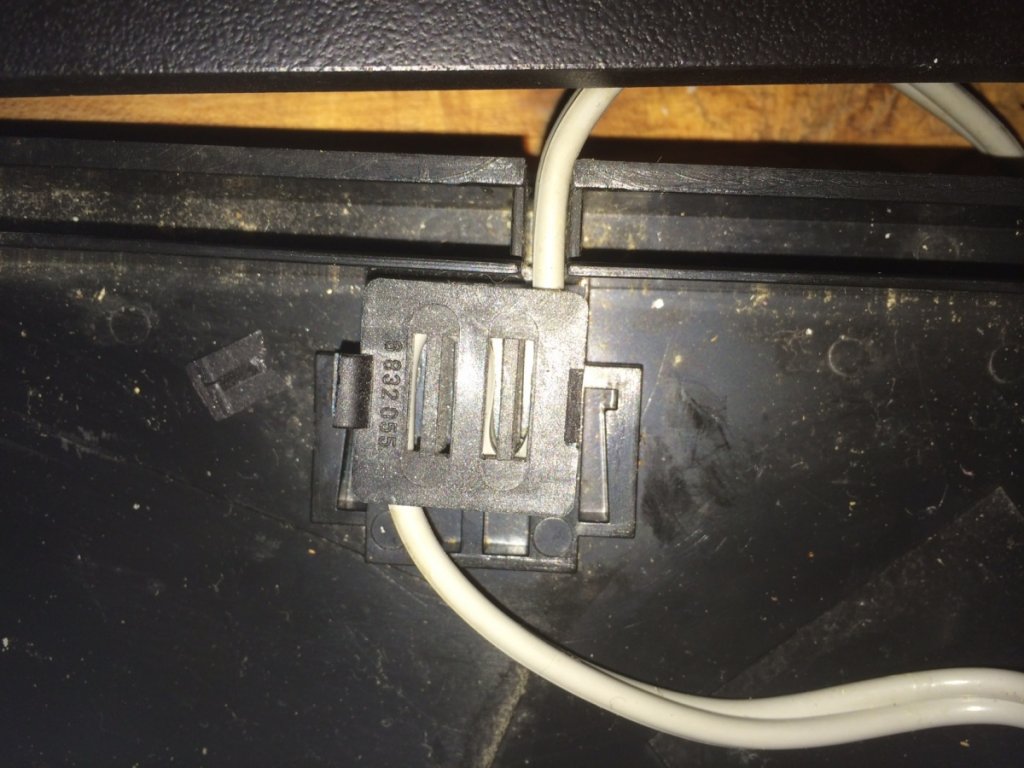
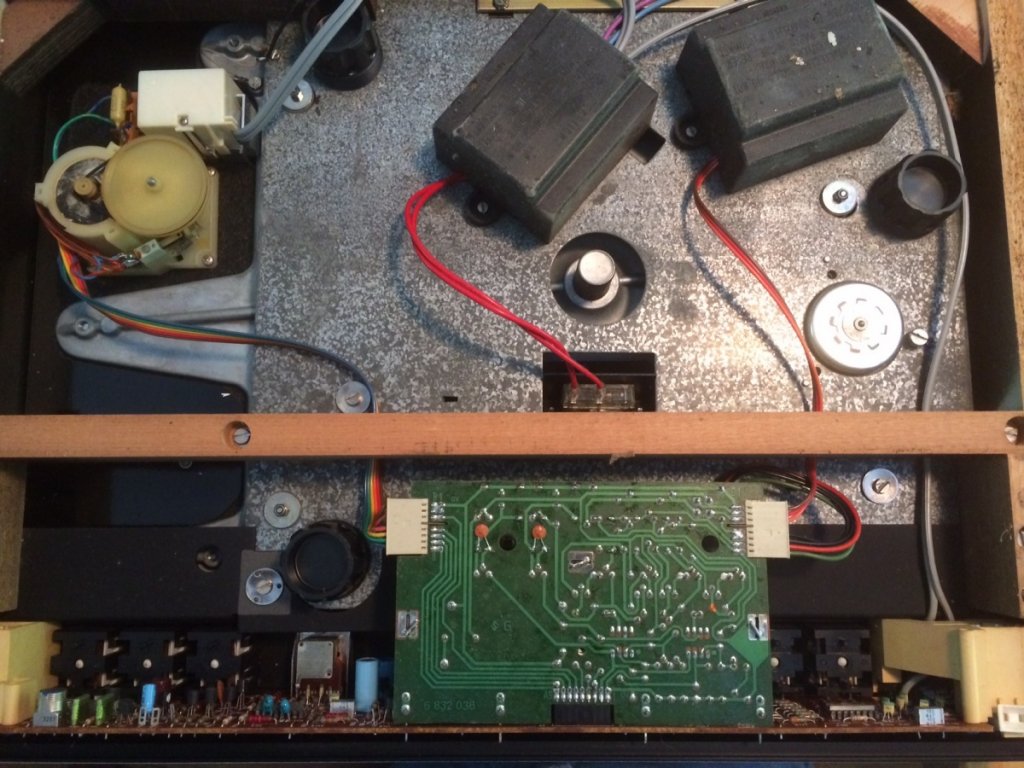