What about assembling something cool such as this, Klaus !
Just Kidding !
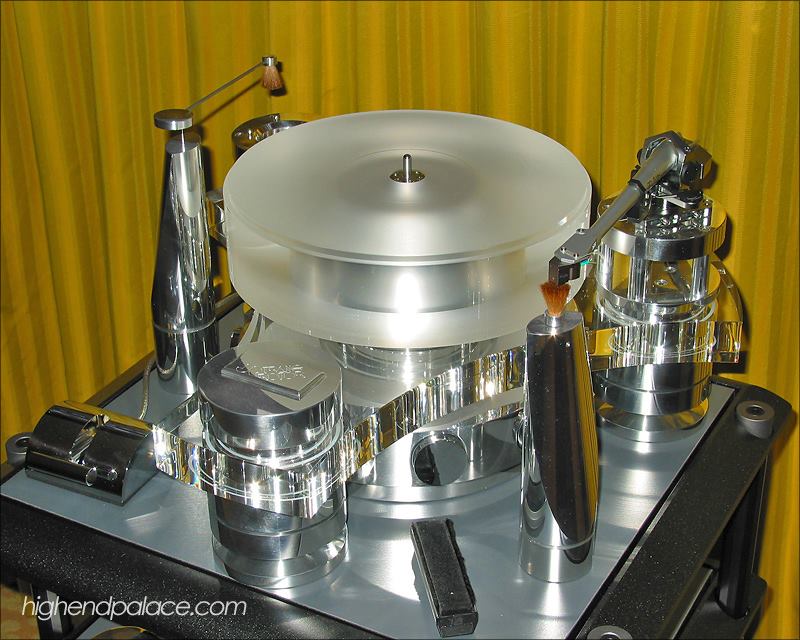
just some thoughts rolling thru my head, and I know some you have already heard a couple times yet.
* a decoupled direct drive would be great, but also a very hard one to make right and yet be affordable. So the next best thing is a belt drive using either rayon, Dacron, or pure silk drive string (no belts per say).
* the motor is an issue, and most are substandard before they are even wired up. The accuracy of a stepping motor or maybe an AC pulse code servo motor with a tack drive built into it (usually standard issue with the better ones). I would prefer a DC motor over an AC, but that becomes an issue in itself. This tach would be supplemented with 6400 line encoder built into the bottom of the platter. The electronic drive (most are toy like) would read and compare both encoders and adjust on the fly. Sounds complicated, but is rather simple in the end. The tach on the stepping motor is standard issue anyway, and would be used to keep the speed constant; while the other would set the actual pace.
* platter can be an issue here. I like heavy dampened metal ones that are built in a series of isolations layers. A spindle diameter of about 30mm using a Moglice sleeve bearing, and a grade 10 ceramic ball bearing that's about 12mm in diameter. This setup should last a couple life times if the spindle is ground right. This bushing is even better than the typical Oillite bearing seen in many high end tables, and can actually be moulded to fit the shaft with about .000050" shrinkage, but that's a little too tight. Two drops of light spindle oil will be all the lube it needs for hours and hours of usage, plus it's a much quieter bearing than typical bronze. The inverted ceramic thrust bearing would ride in a carbide cup that's ground and lapped for a low single digit surface finish. This cup would fit in a pocket that is also loose. It would be epoxied in place on final assembly for a perfect alignment with perhaps a three tenth arc second error due to shrinkage of the epoxy.
* the base would be of either soft steel or aluminum using a three point setup to assure a perfect plain. Setup to allow the use of three tone arms with an infinite adjustment to gain a near perfect alignment and yet be able to use a tone arm upto 14" (if there ever is one). The tone arm bracket would be isolated from metal to metal contact with the base. Maybe using something like .125" Turcite that is machine to be dead perpendicular with the spindle / platter top. All this sounds hard to do, but is actually very easy to do. The motor would be free of the table, but would also set atop on isolator. One issue that's very hard to deal with when using an AC motor is the 60Hz vibration that will travel thru everything electrical. There are anti vibration devices to counter action this problem.
* the electronic drive would mimic the one used by Acoustic Signature (still the best). I would have a read out from the spindle encoder for a finite adjustment.
To build this table, you'll need a good gauge quality grinder. (Studer or Browne & Sharpe) The base can be machined on a cnc machine center as long as the machine is properly aligned and leveled (80% are not). The spindles can be roughed out of A2 and hardened & ground. But you could also pretty much do everything off a 30mm gauge pin, but wouldn't be fun to do. Interestingly, you could also make the tone arm mount out of strait brass. This metal has a very low sonic threshold. You could even do the base in brass, but your looking at a $150 piece of brass, minimum. There's another way to do this starting out with a four inch thick piece of composite granite, but granite has it's own set of issues that hard to work with.
gary