Hi All
I visited KR audio in Prague a week ago and thought I might share my experience with you.
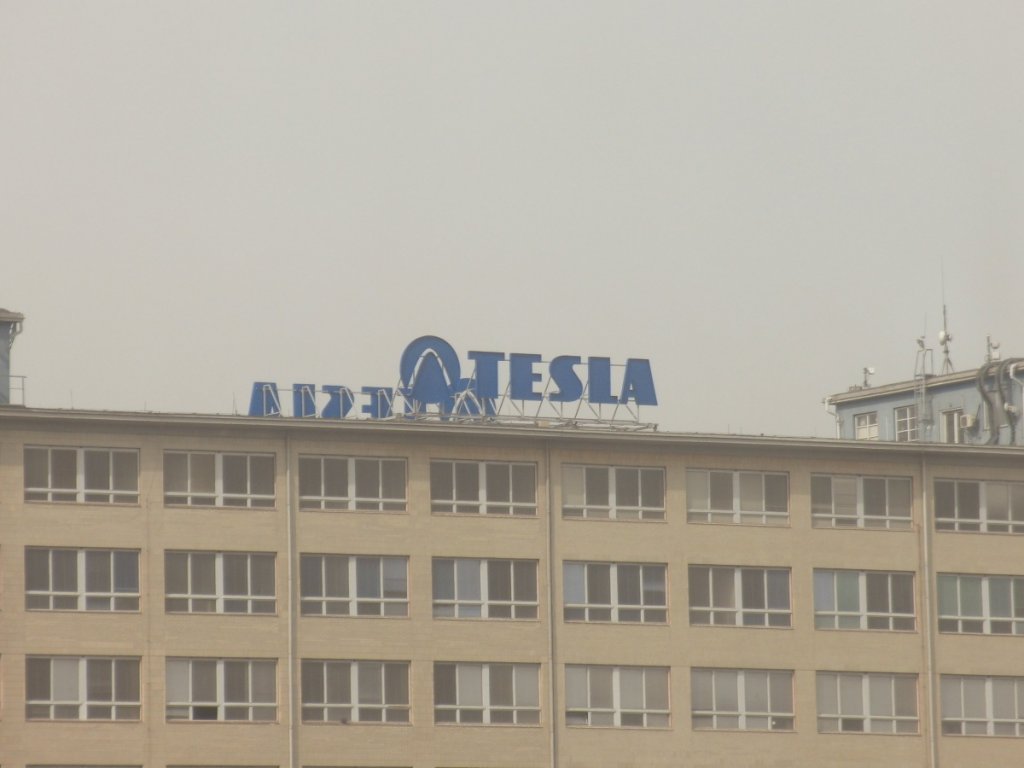
On the outskirts of Prague lay the remains of the giant electronic producer TESLA. Enormous old factory buildings that once housed the production of tubes in all shapes and forms. Today KR AUDIO is housed partly in these facilities and since then been producing high quality audio tubes.
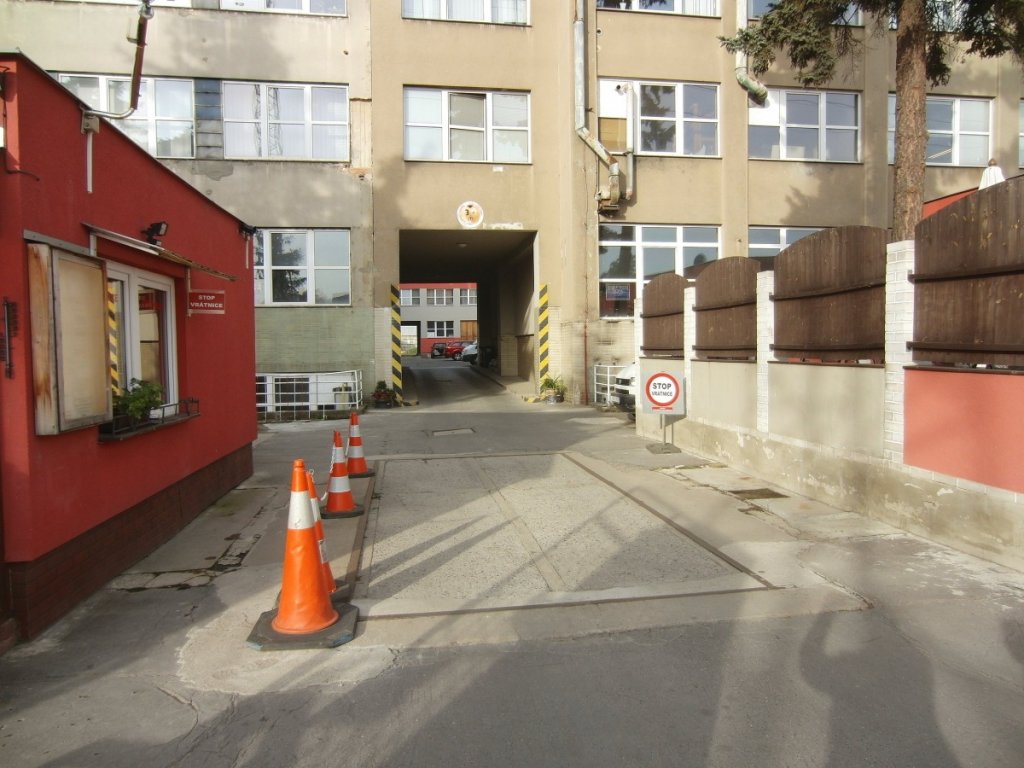
Welcome to the factory.
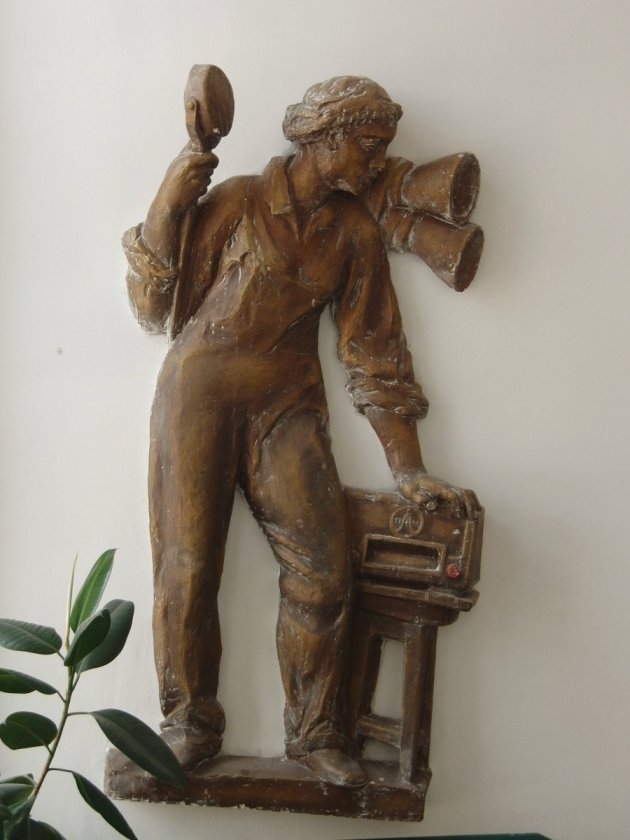
On the stairway wall is the remembrance of what once was produced in these buildings presented by this figure of the TESLA telephone worker.
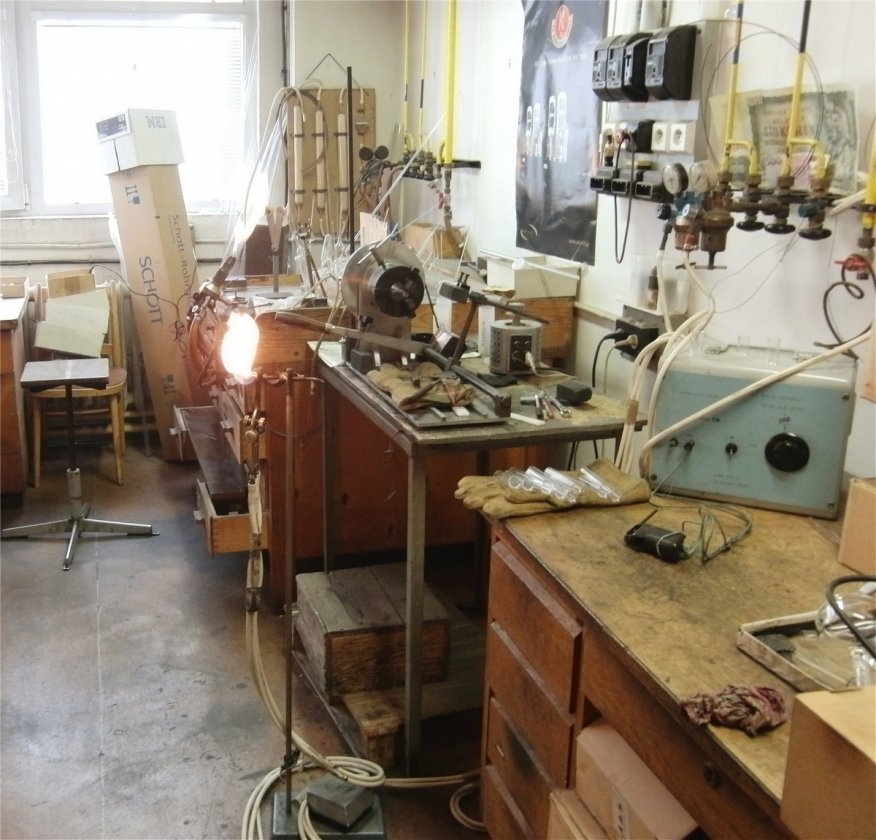
Once inside it feels like time has frozen and one gets transferred back in time to when things where made by hand and skilled craftsmanship. An open flames burning makes the room hot and one has to be aware when moving around. In this room the tube bottoms are produced and married to the tube dome once all the inner parts are connected and fastened.
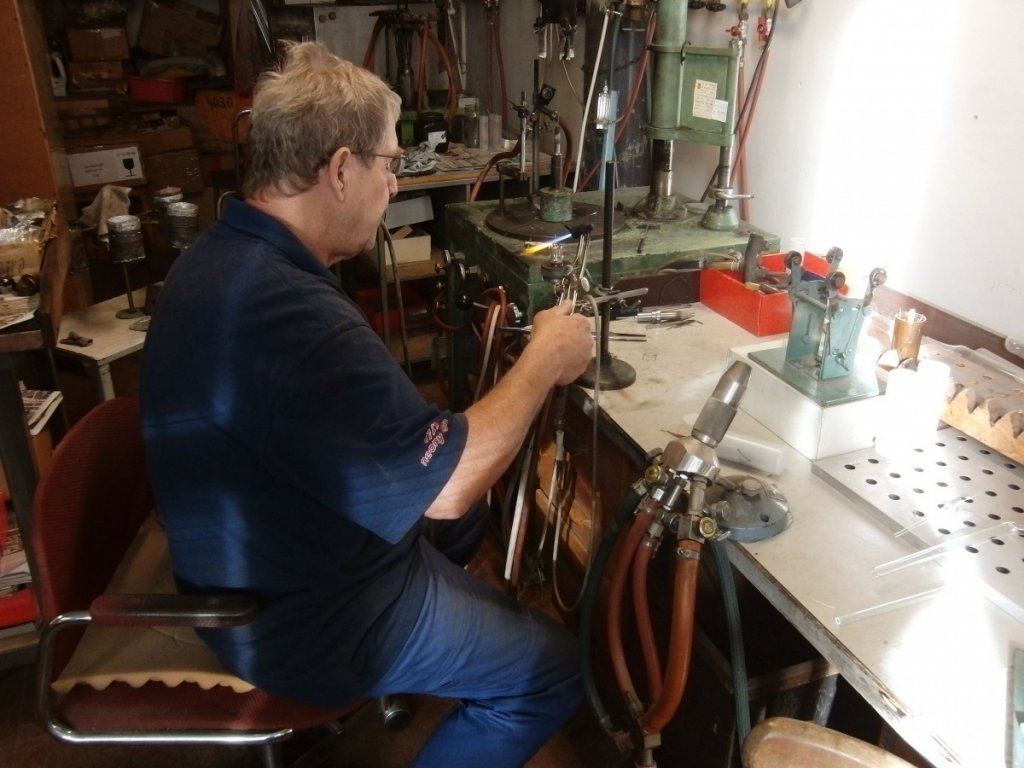
A skilled glass technician at work producing tube bottoms. He works from one place of the room quickly moving to the other side all the time. Better watch out for those flames…..
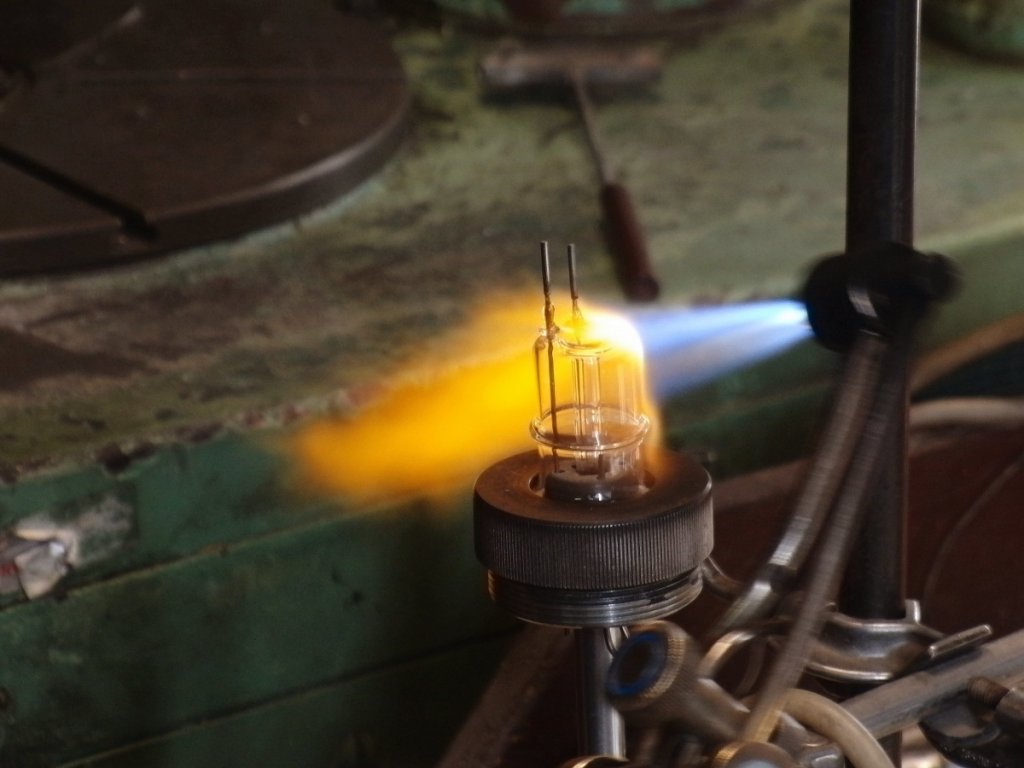
A tube bottom is beeing heated up before pressing it into form.
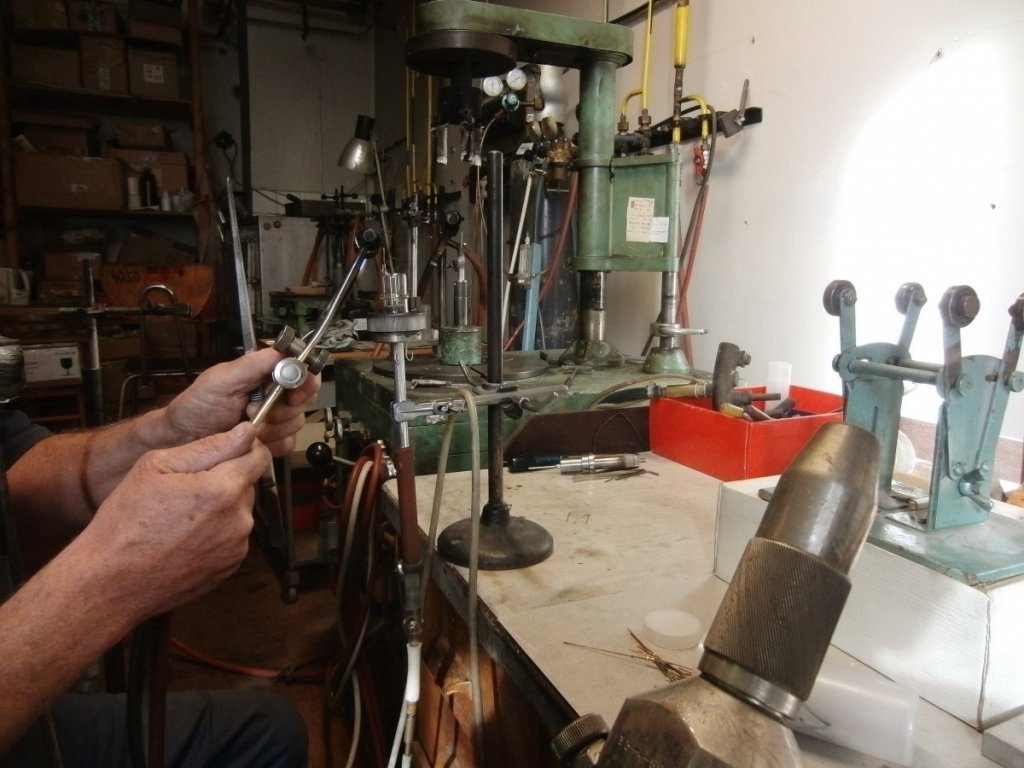
The pressing.
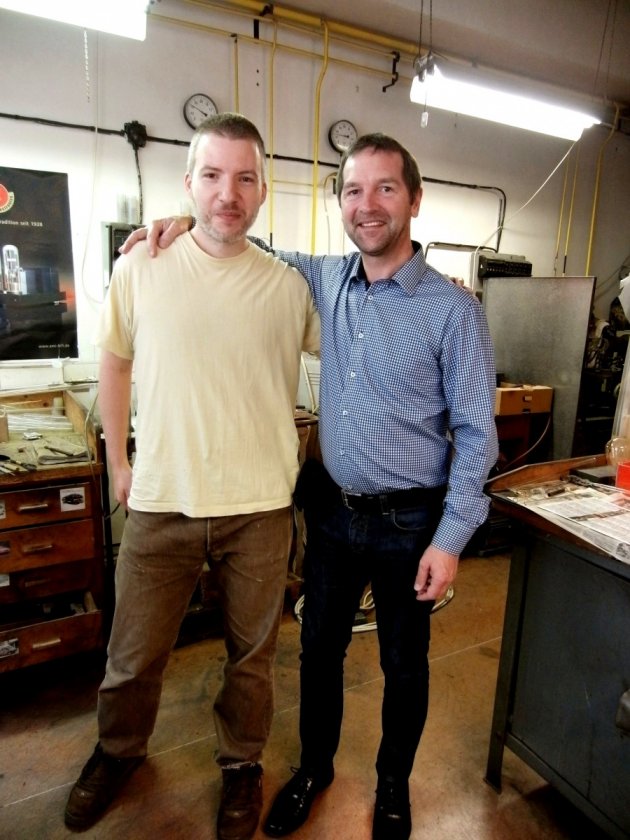
Chief engineer Marek steps in to say hello.
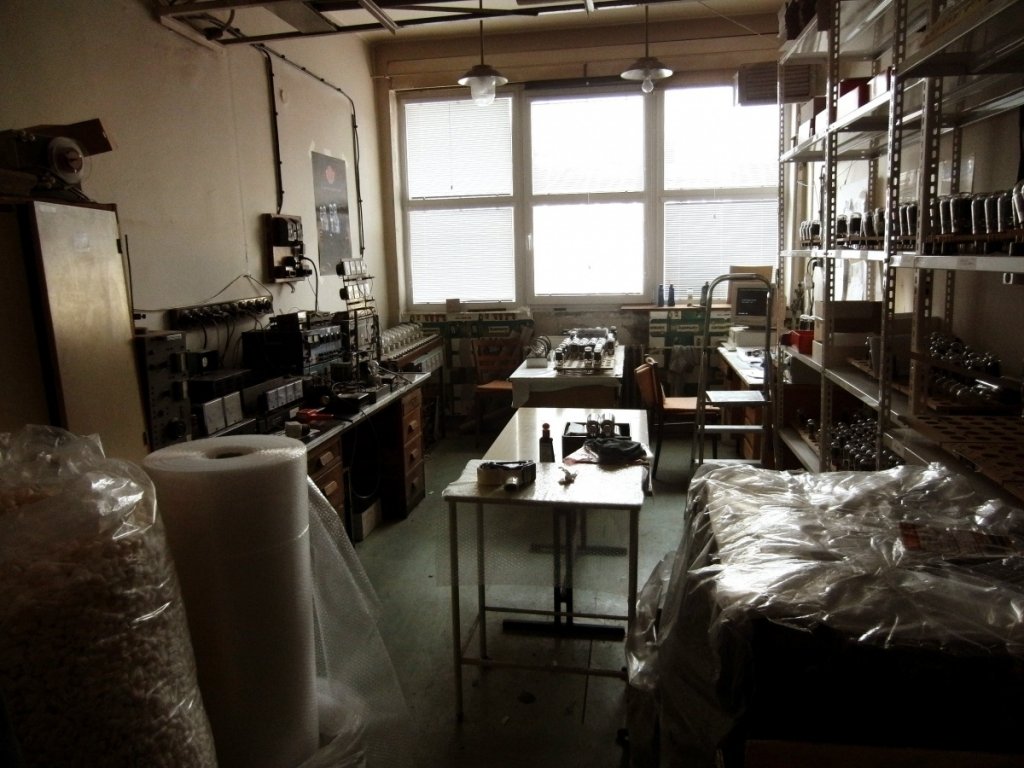
We now move to the next production room, in fact this picture of the room comes in at an early stage because this is the storage room, also used for QC. On the left hand side is the old tube tester and burn in bench. Hiding away in the right hand corner is a modern computer based tube tester for high precision testing.
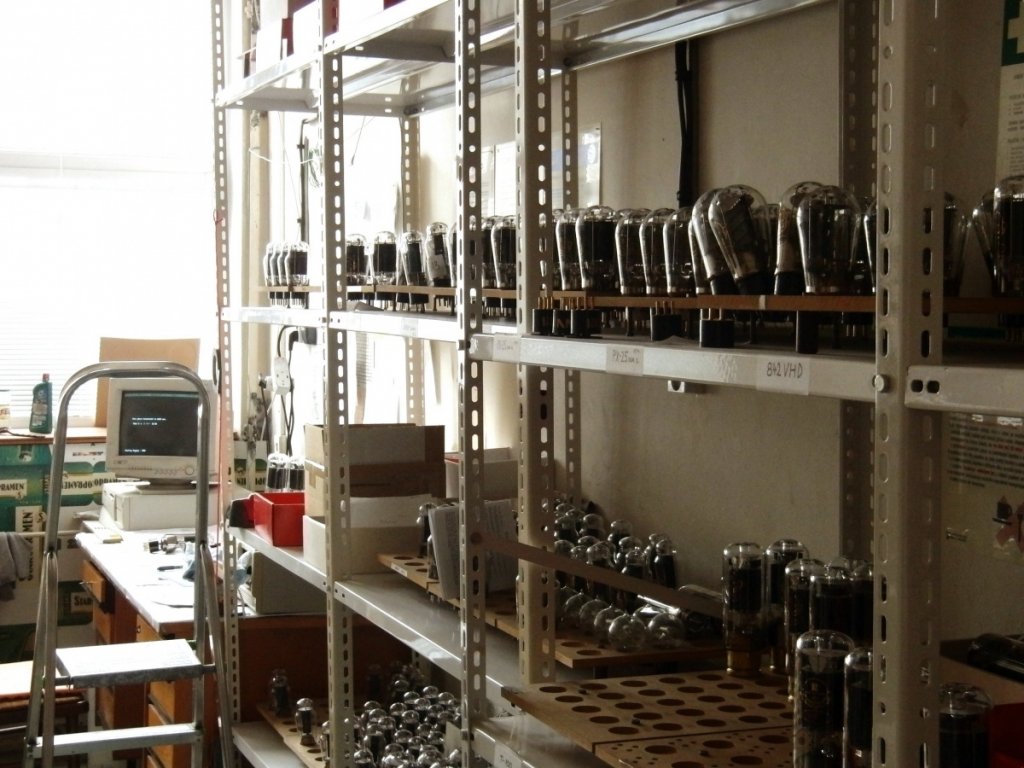
Tube storage.
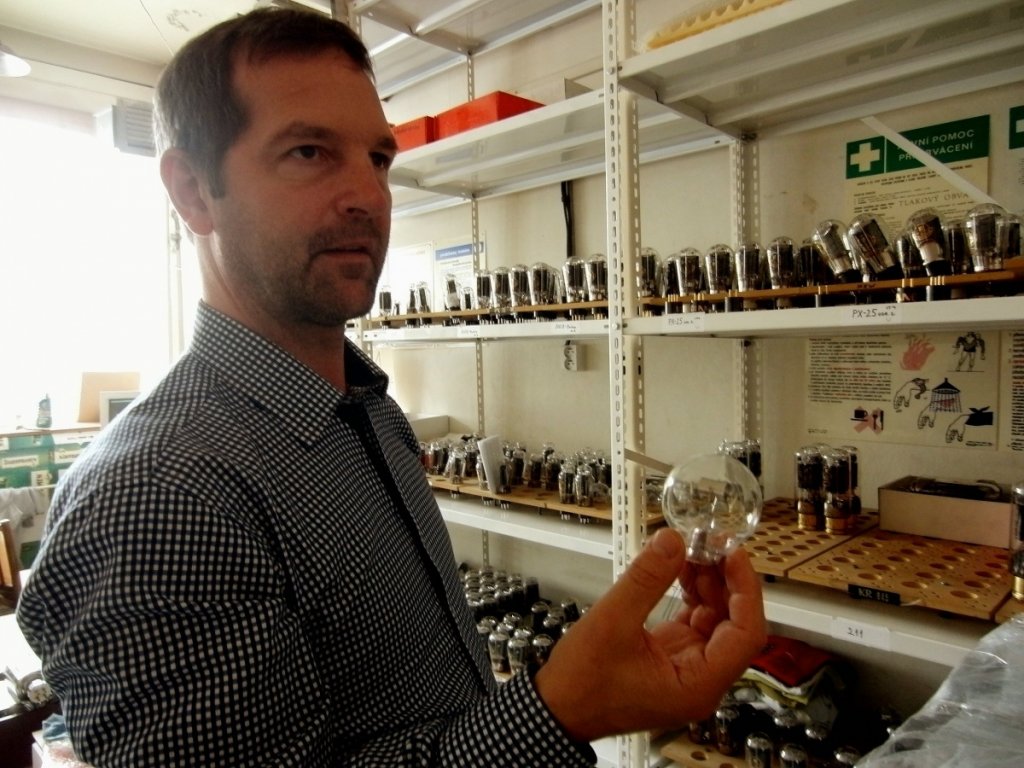
The Marconi tube (without socket) is being scrutinized.
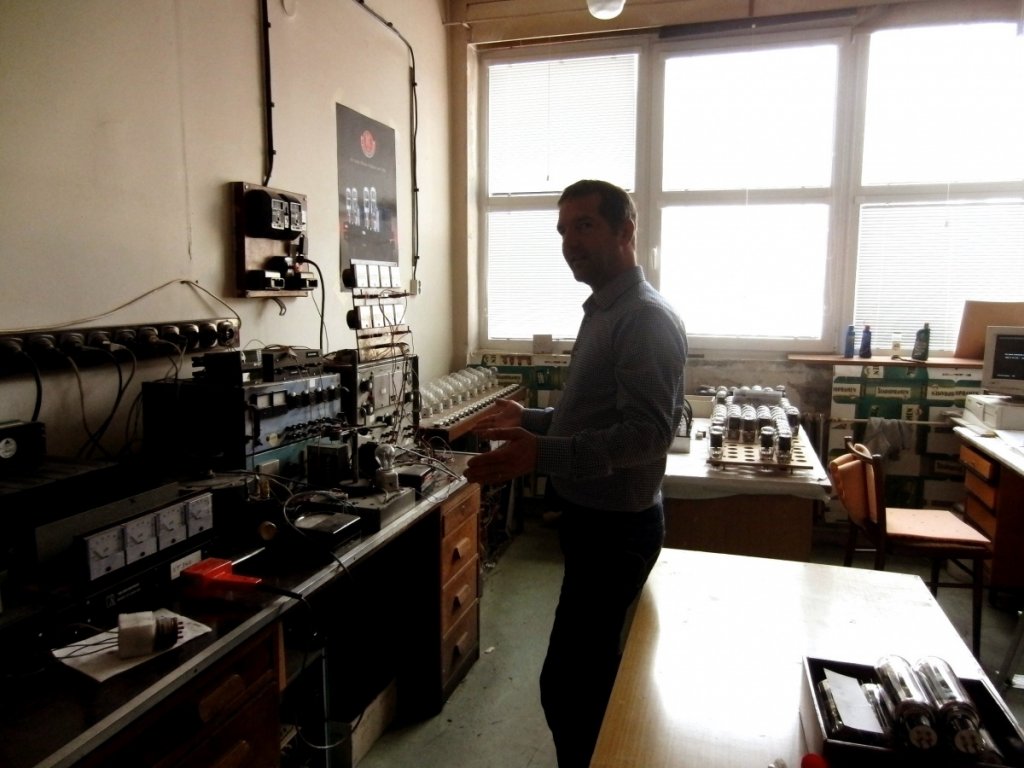
Here´s the old tube testing equipment, still used today in testing.
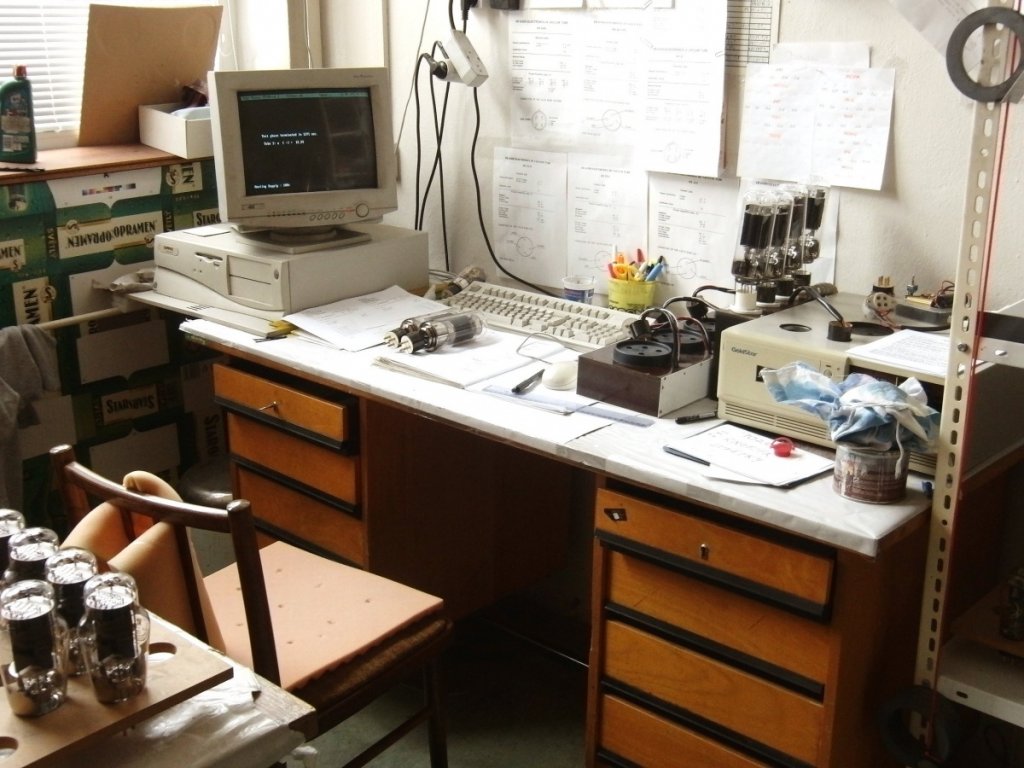
This is the modern computer based tube tester.
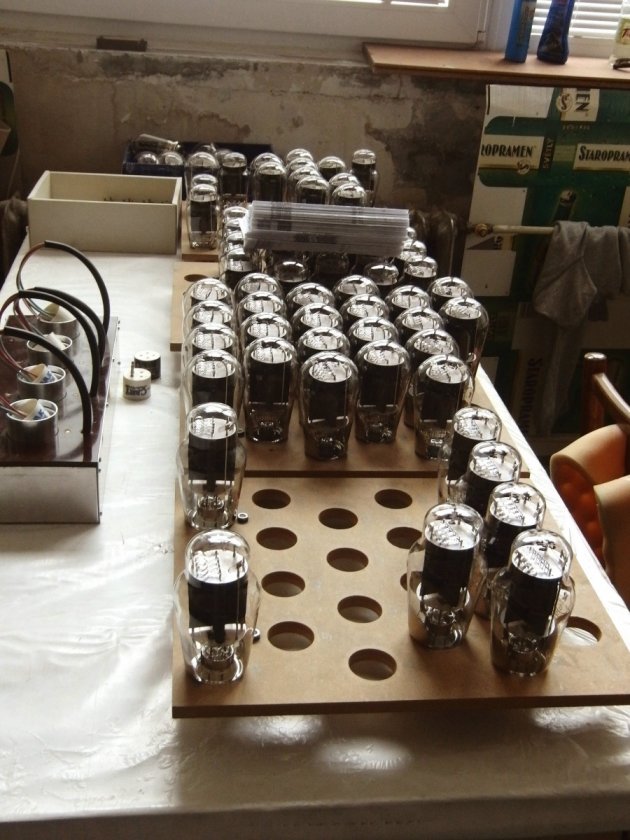
Tubes waiting for matching.
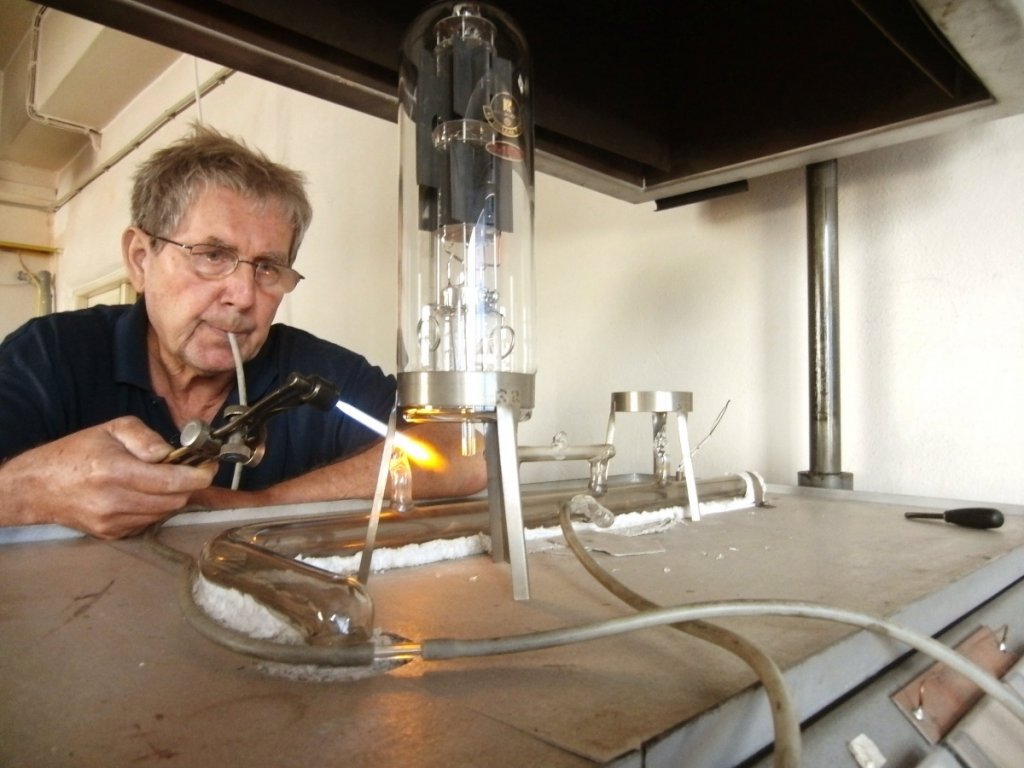
Now we move into the next production roor. Here the technician is welding the tube to a glass pipe. This pipe is connected to a vacuum pump and also an oil distiller device to create the high vacuum. This is also a heating chamber to heat the tubes under vacuum.
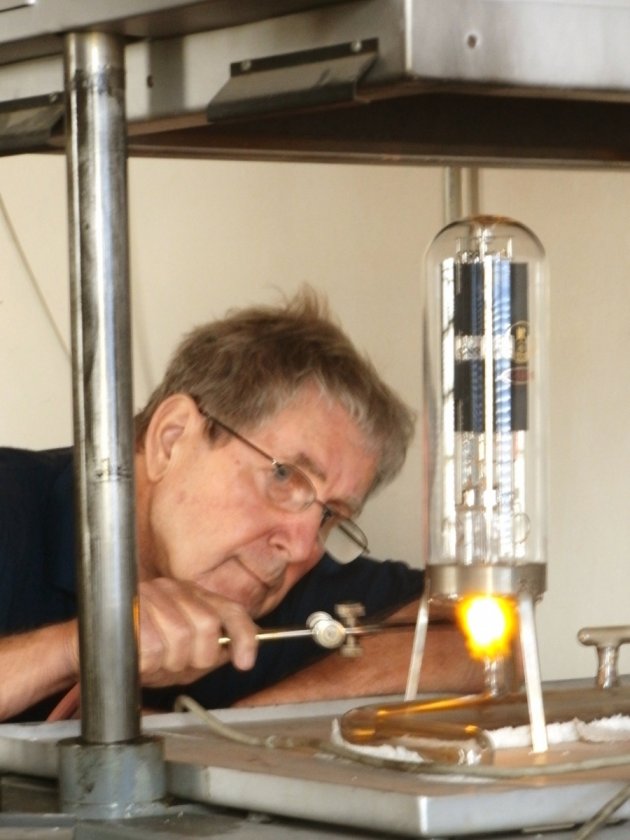
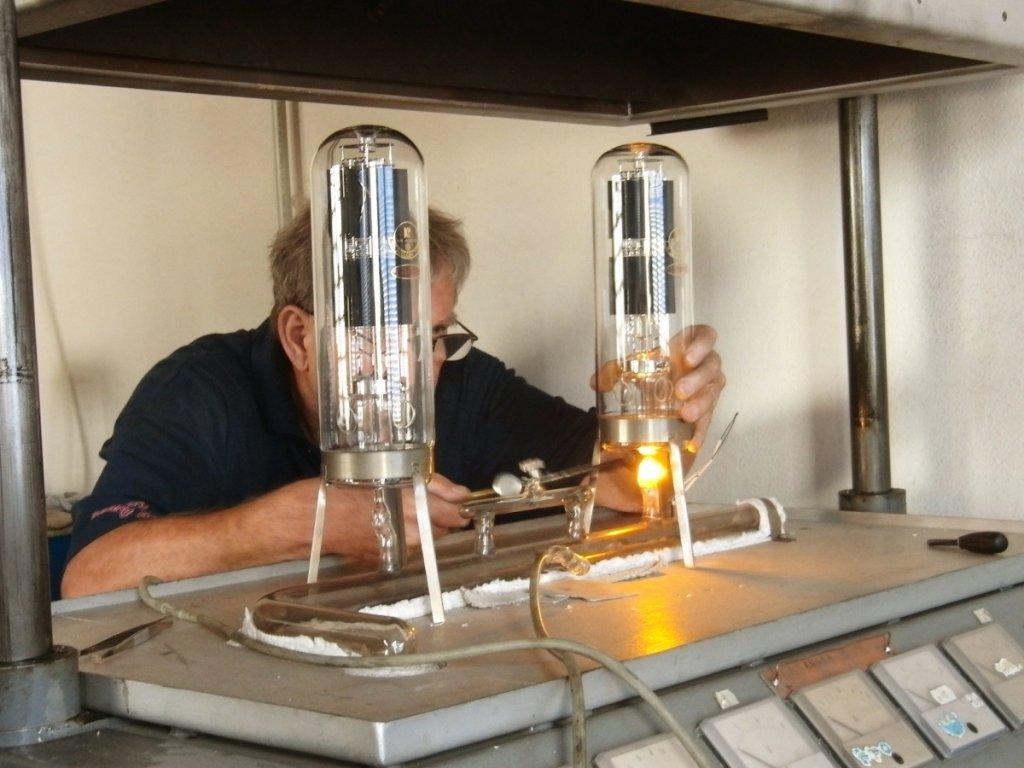
Tube nr 2.
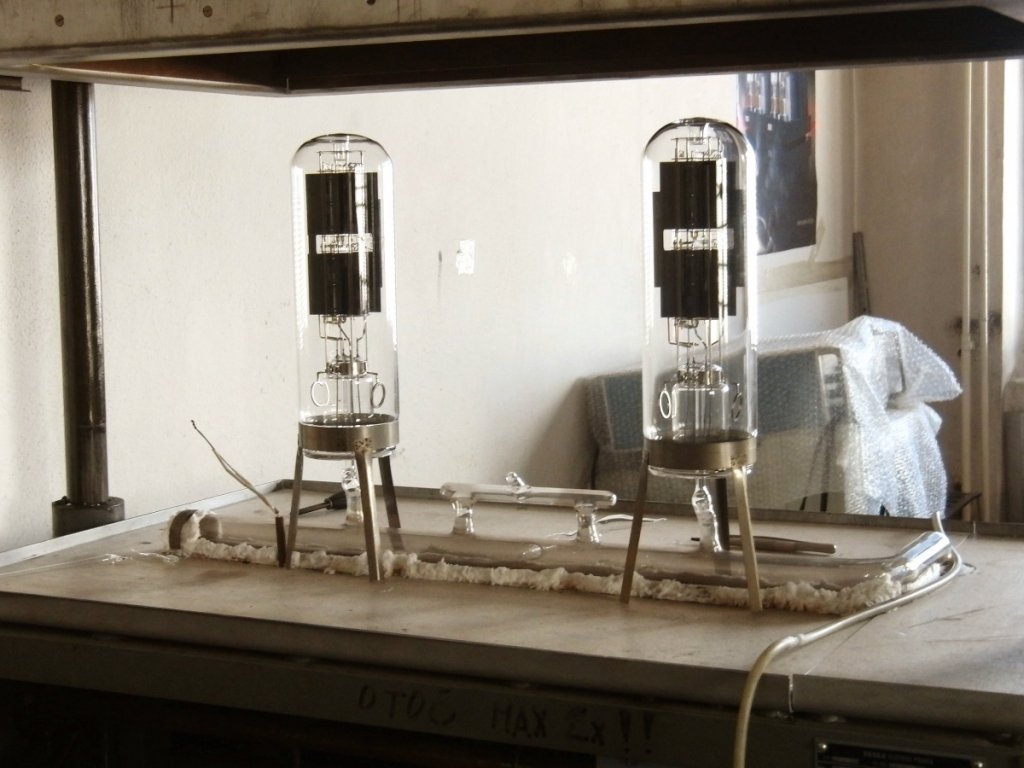
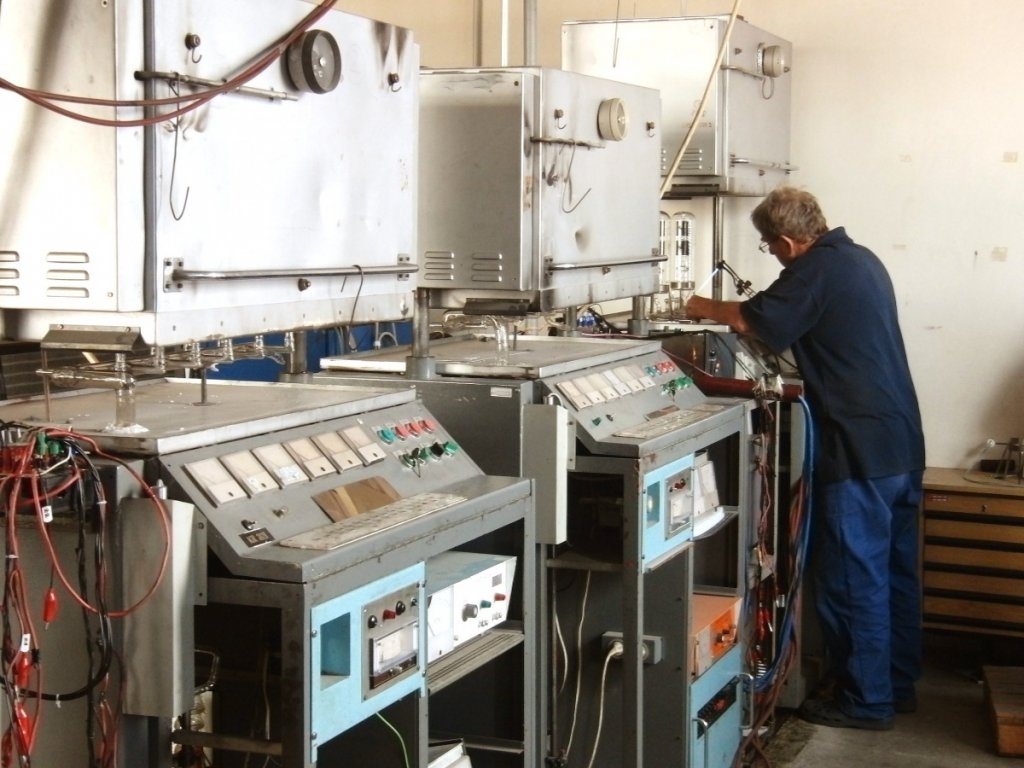
Final touch
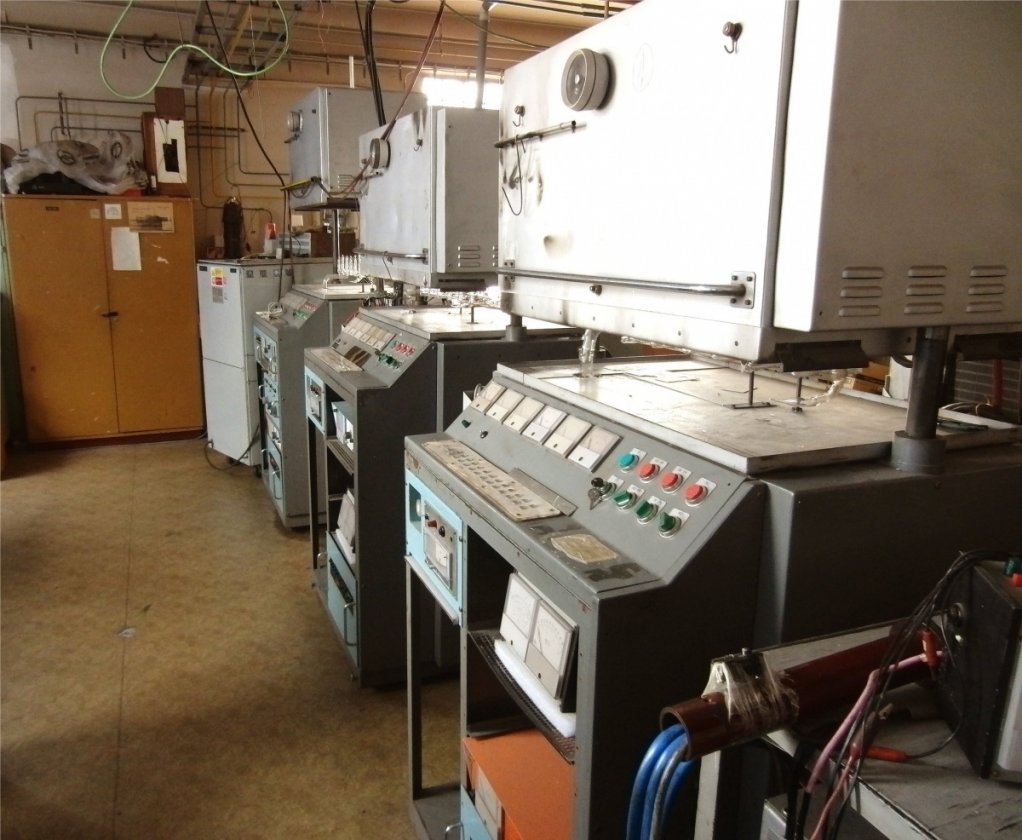
These machines are from the TESLA age and where used for research. They are perfect for small production scale.
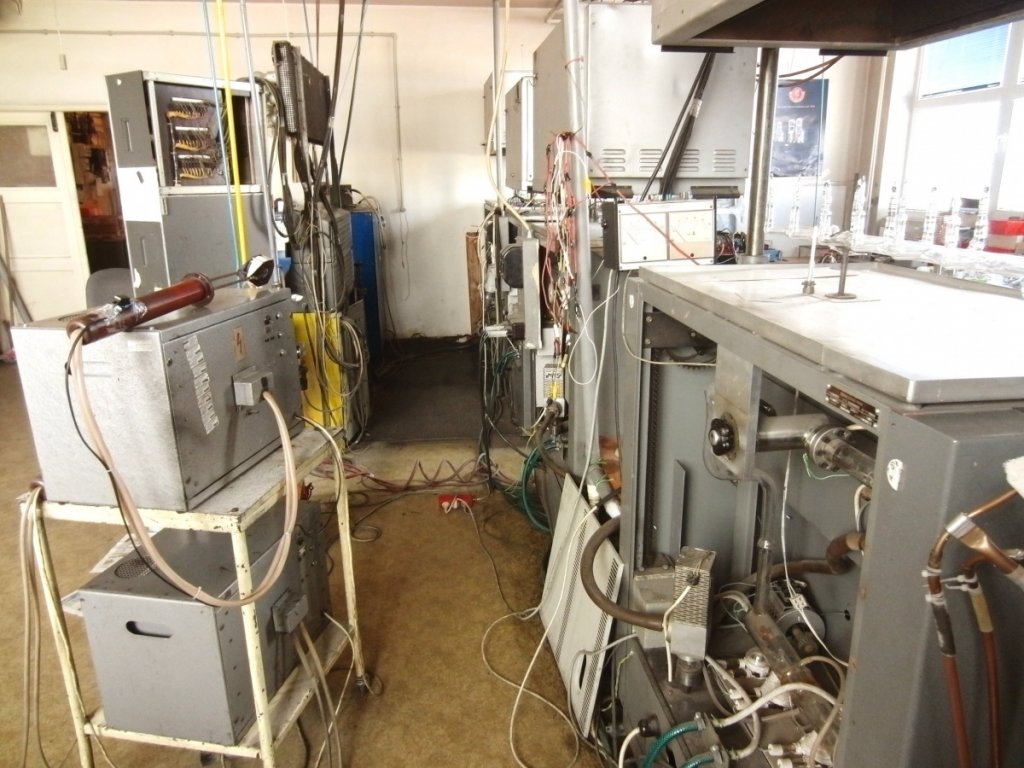
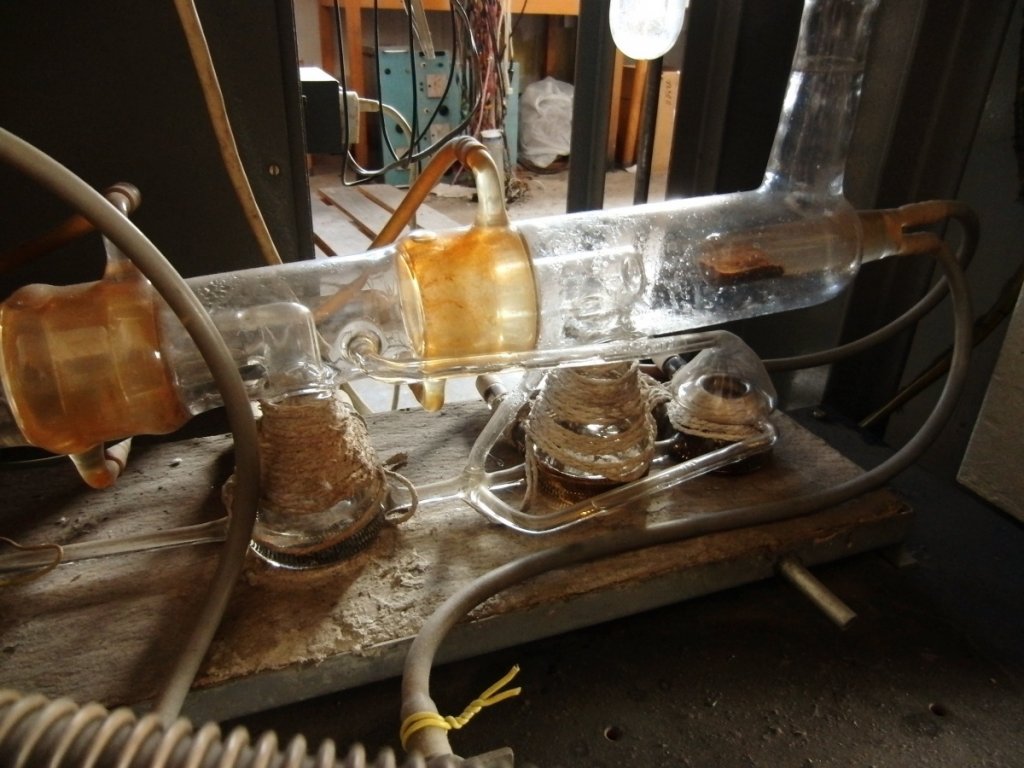
Oil distiller device for creating the high vacuum that KR is known for.
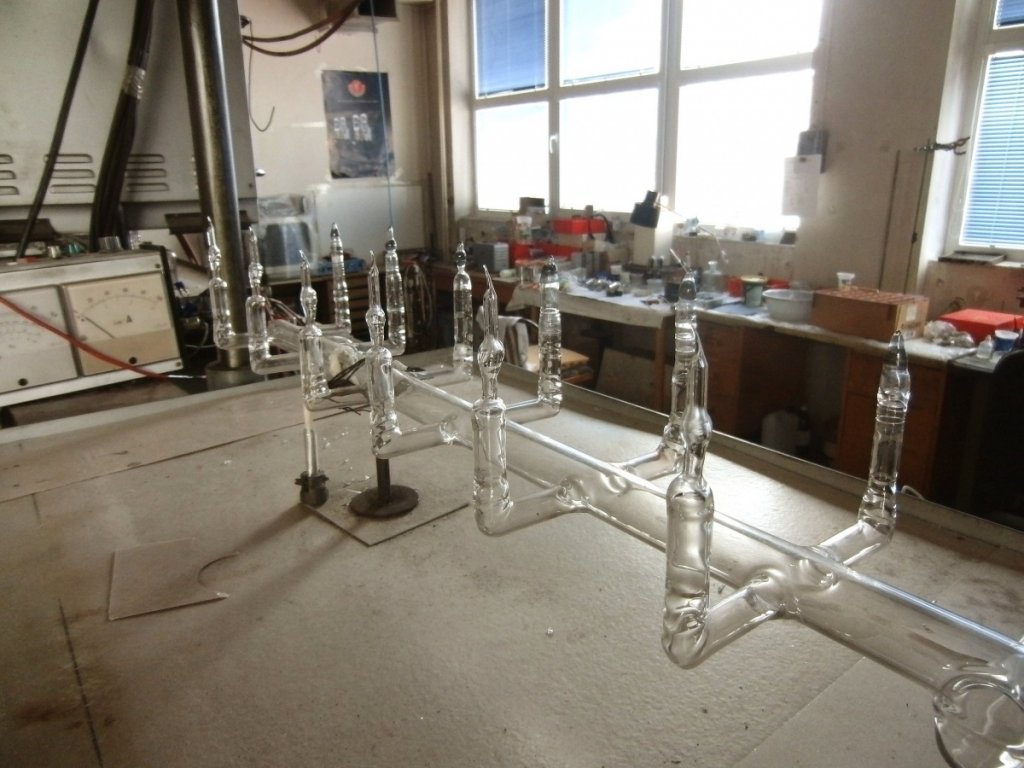
This is what remains once the tubes are vacuumed and dislocated.
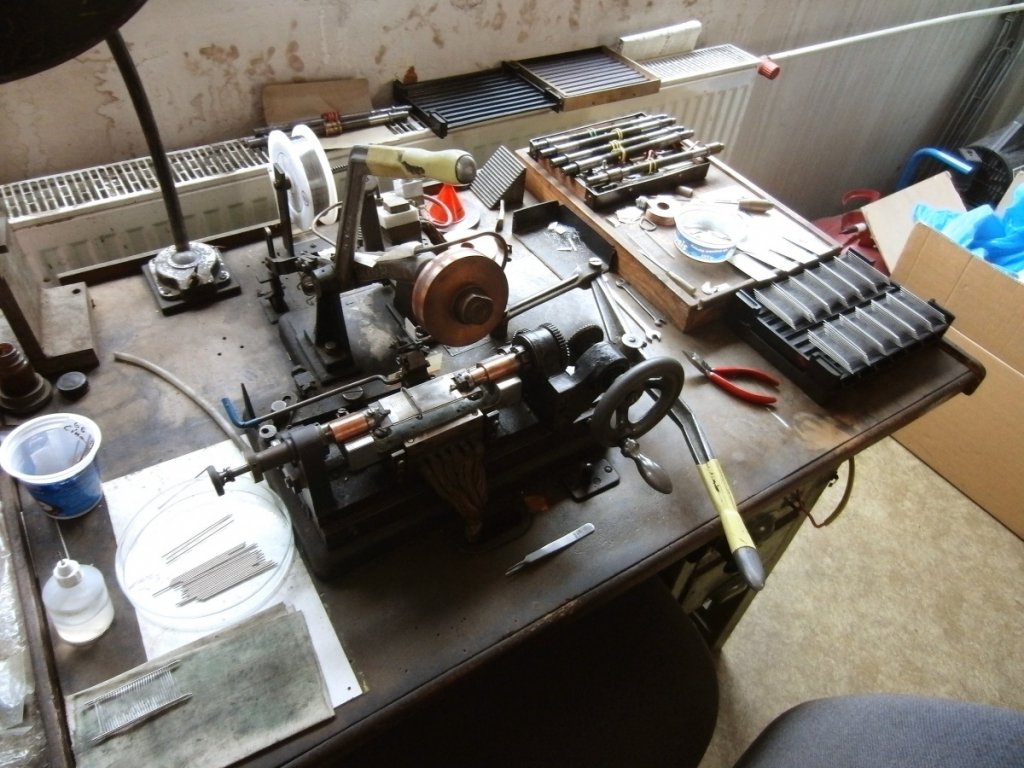
This old machine is from WWII era and is used for making the grids.
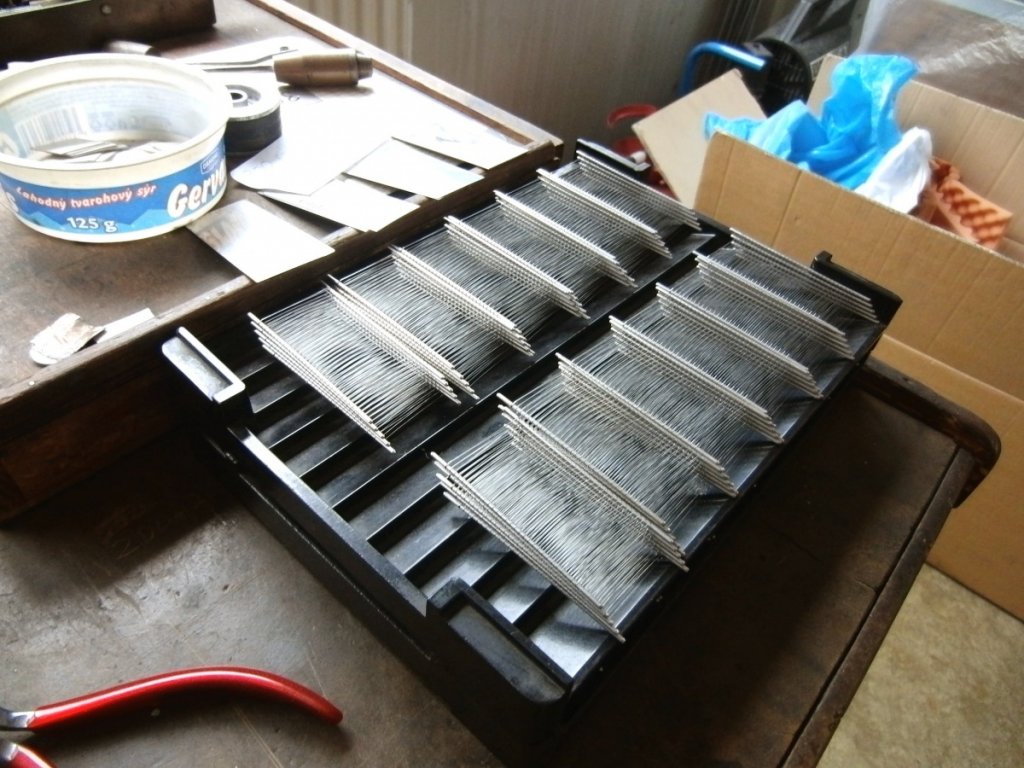
Grids ready for assembly.
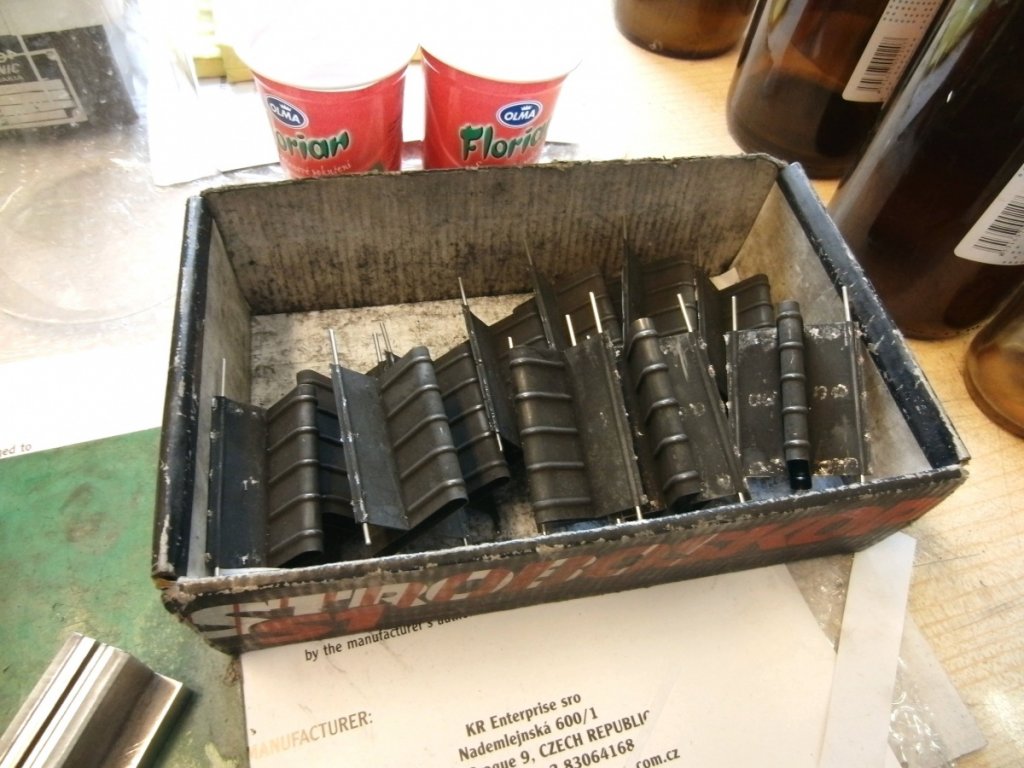
Now we step further and into the next room where the plates are produced and all internals assembled. Anode plates ready for assembly.
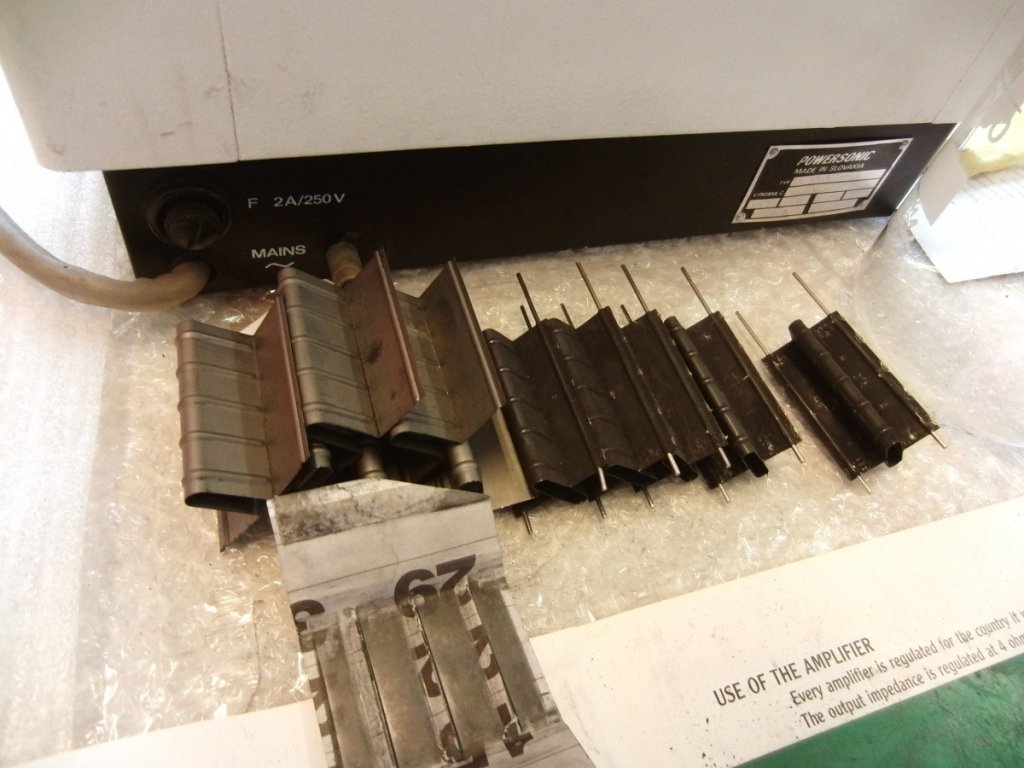
Notice the left anode plates are not coated, the right ones are. At the bottom of the picture the press tool is present.
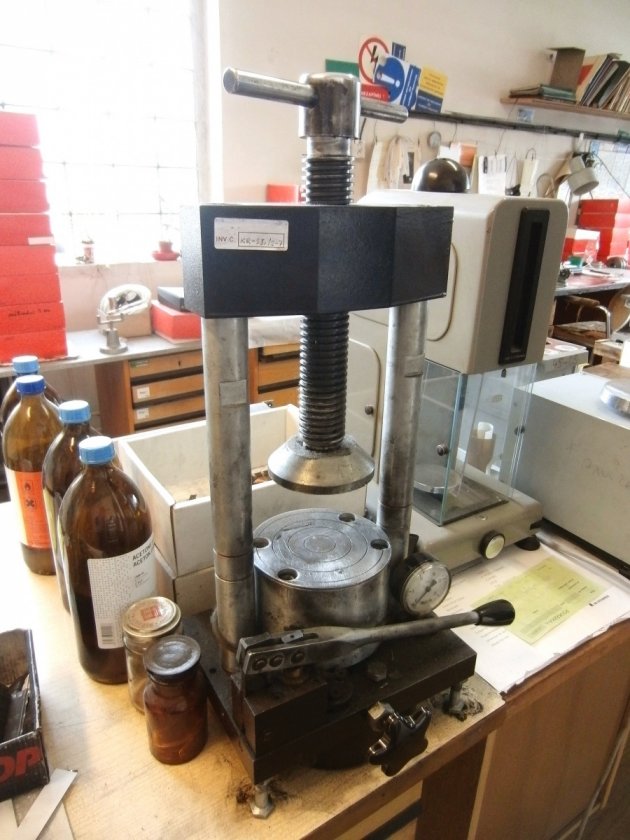
The press for pressing out the shapes of the anode plates.
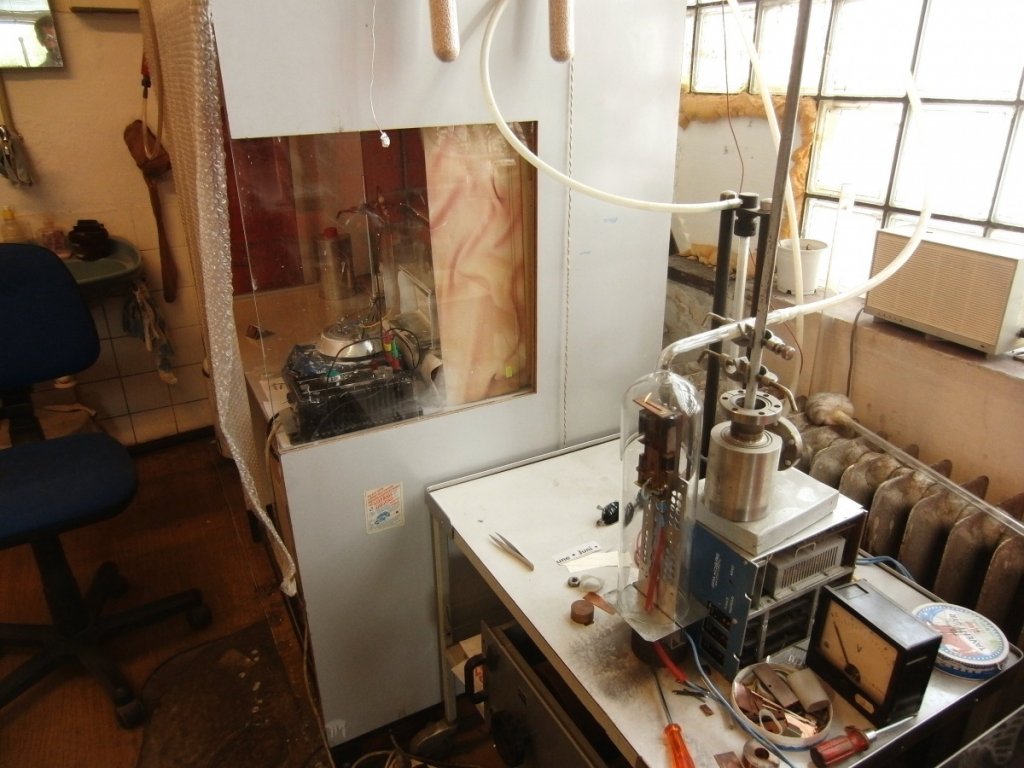
This machine is for mixing the anode plate material.
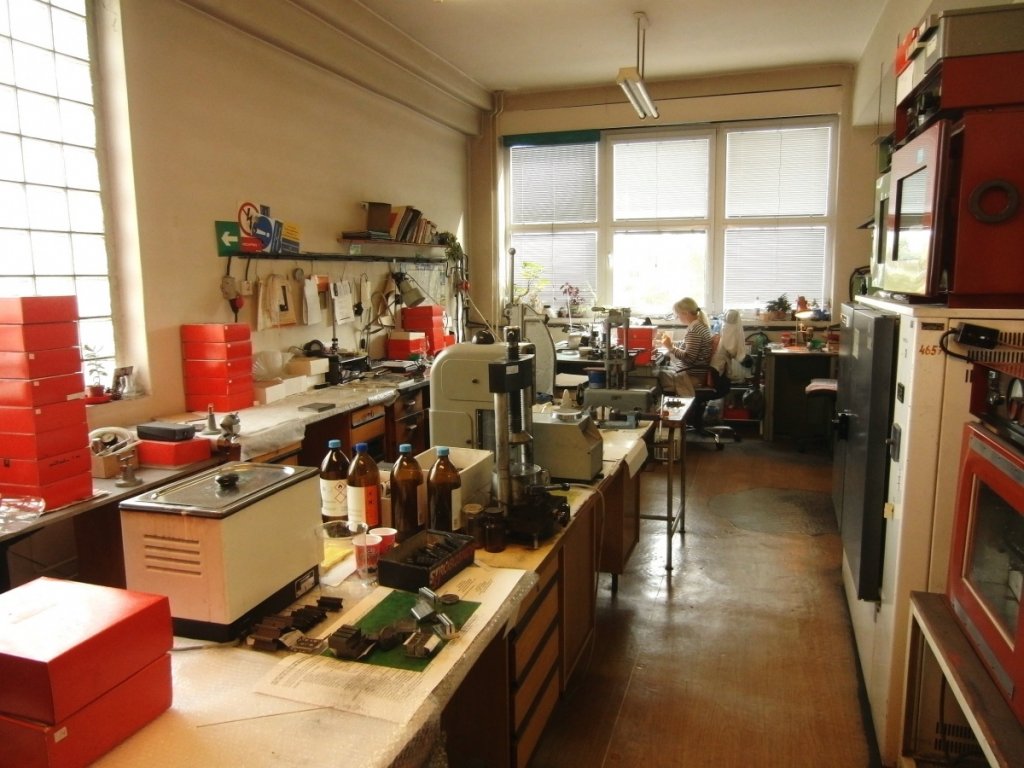
A full view of the room. At the far back of the room the assembly station is present. This is the station where the anode plates are welded and the tube internals are married together.
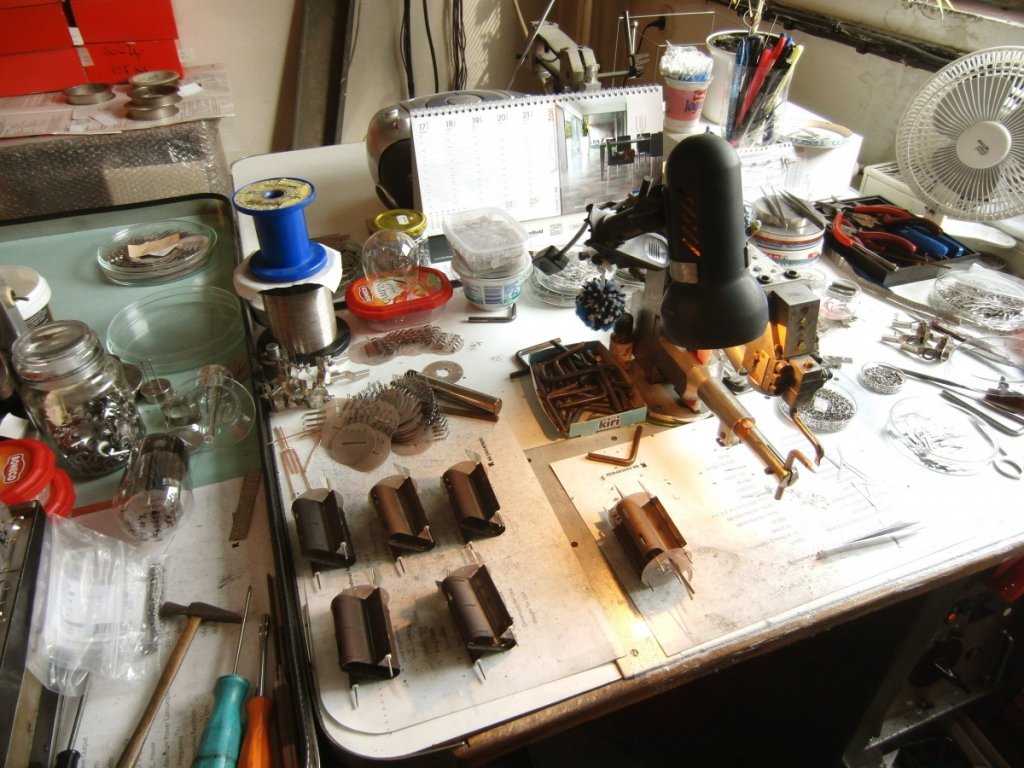
Notice all the parts!!
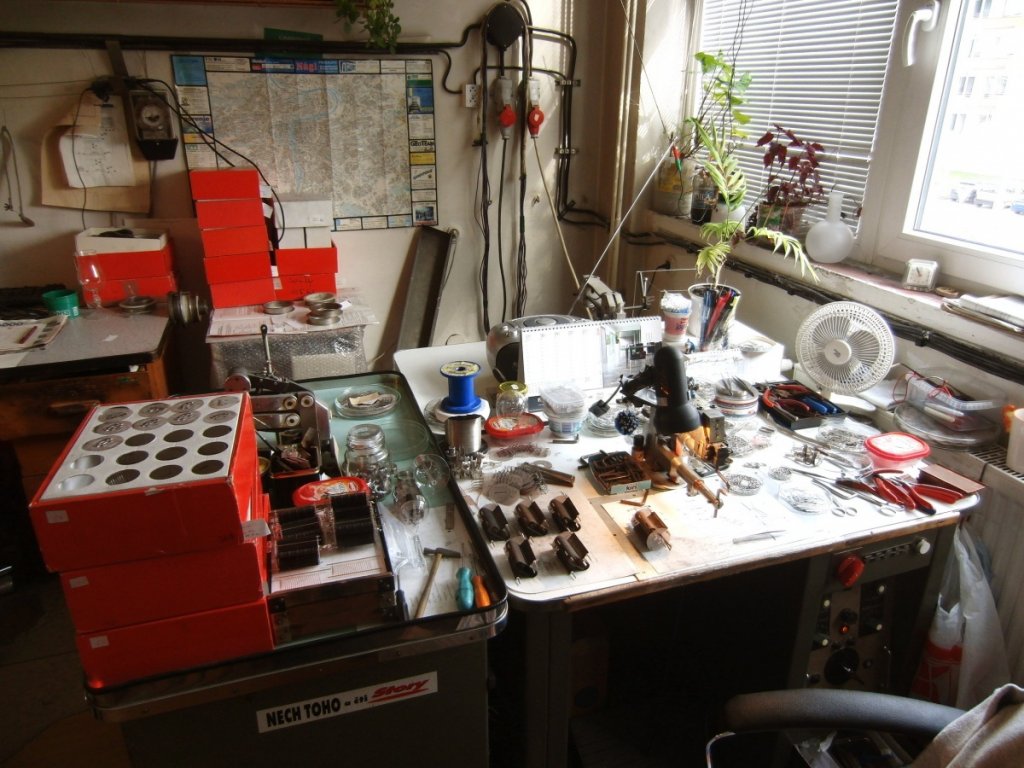
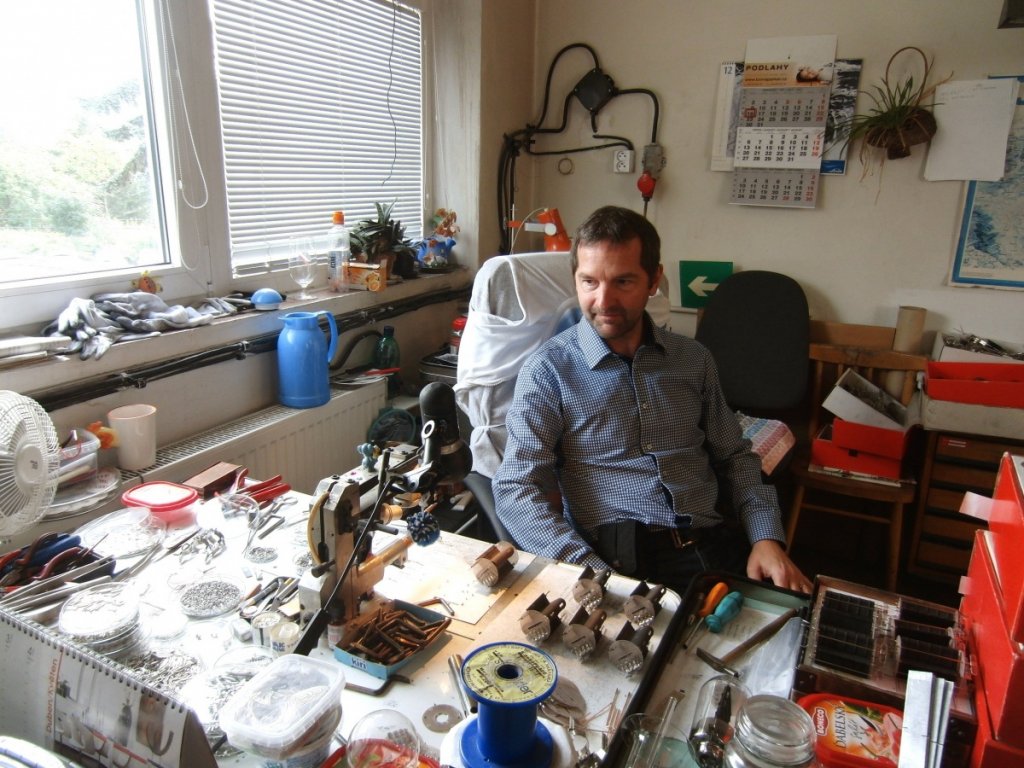
I wouldn´t know where to start and havn´t the patience.
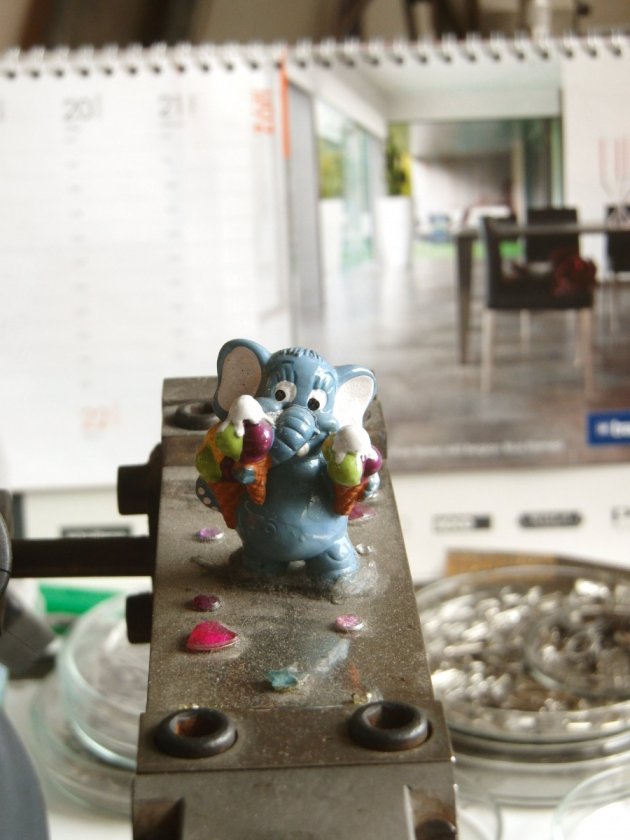
Mascot to keep company.
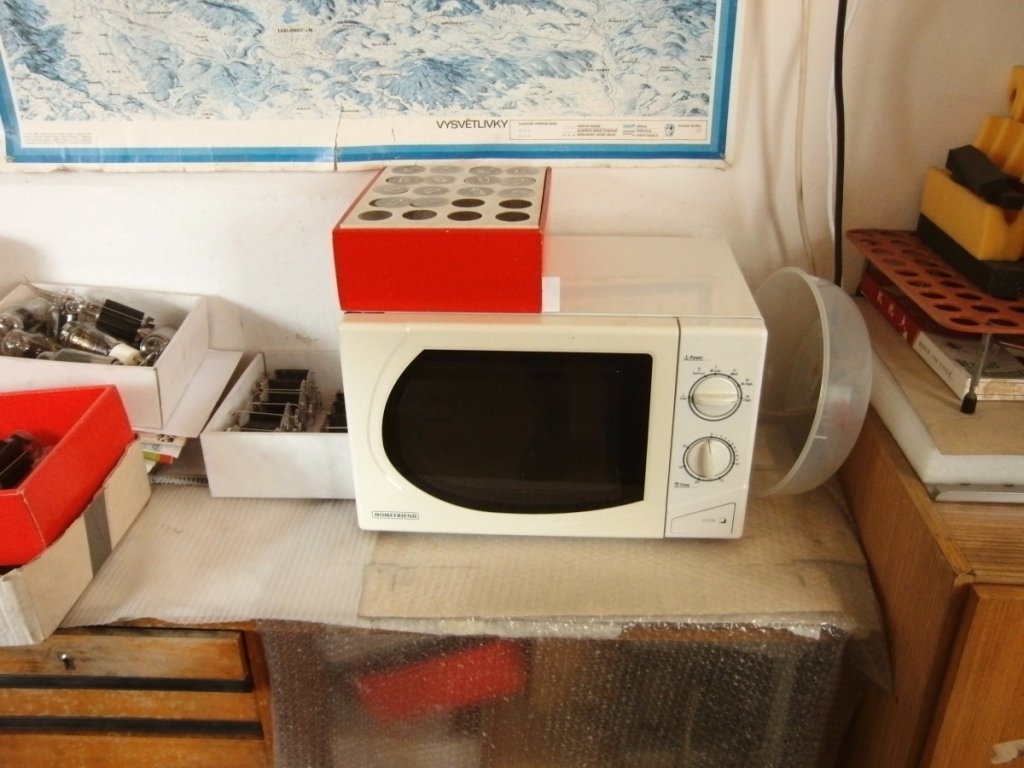
High tech precision industrial machine for heating lunch.
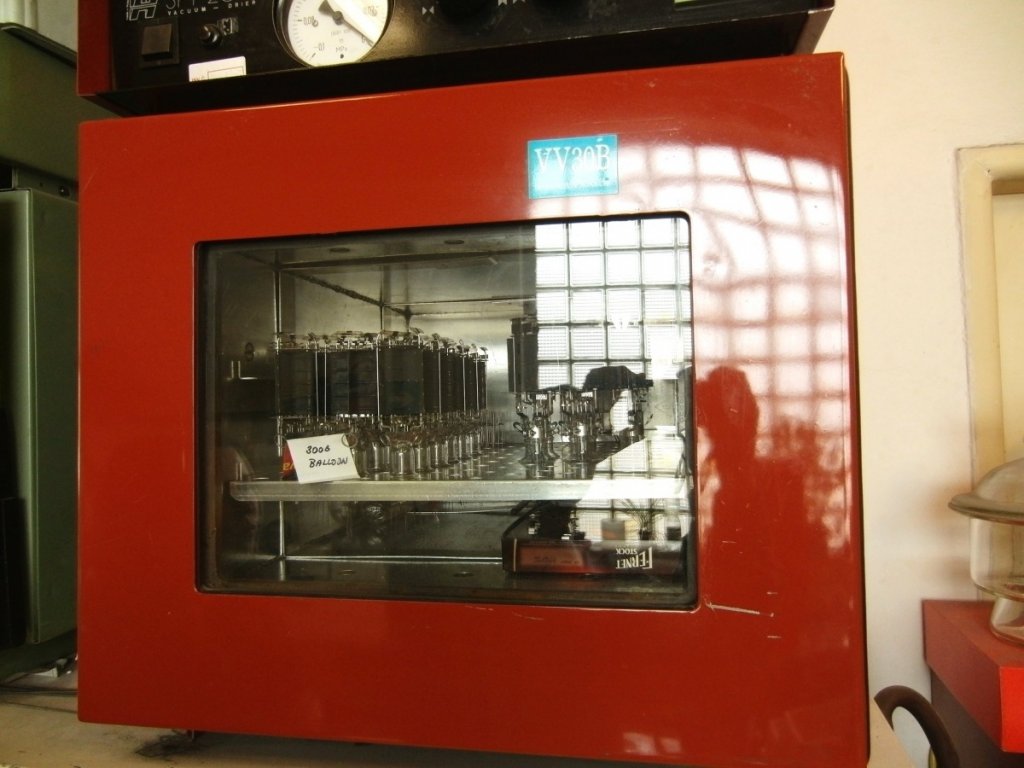
This is for storing the completed tube internals before enclosing them in the glass tubes.
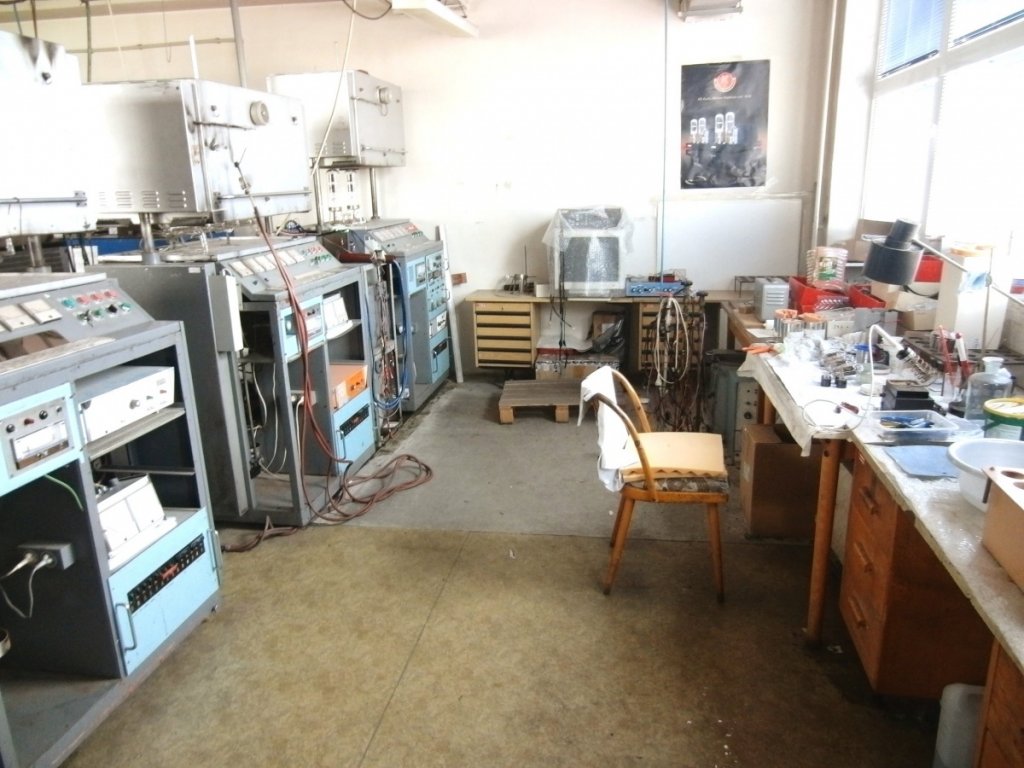
Once the tube internals are enclosed in the glass tube it´s time for the socket mounting. This is done at the mounting station on the right.
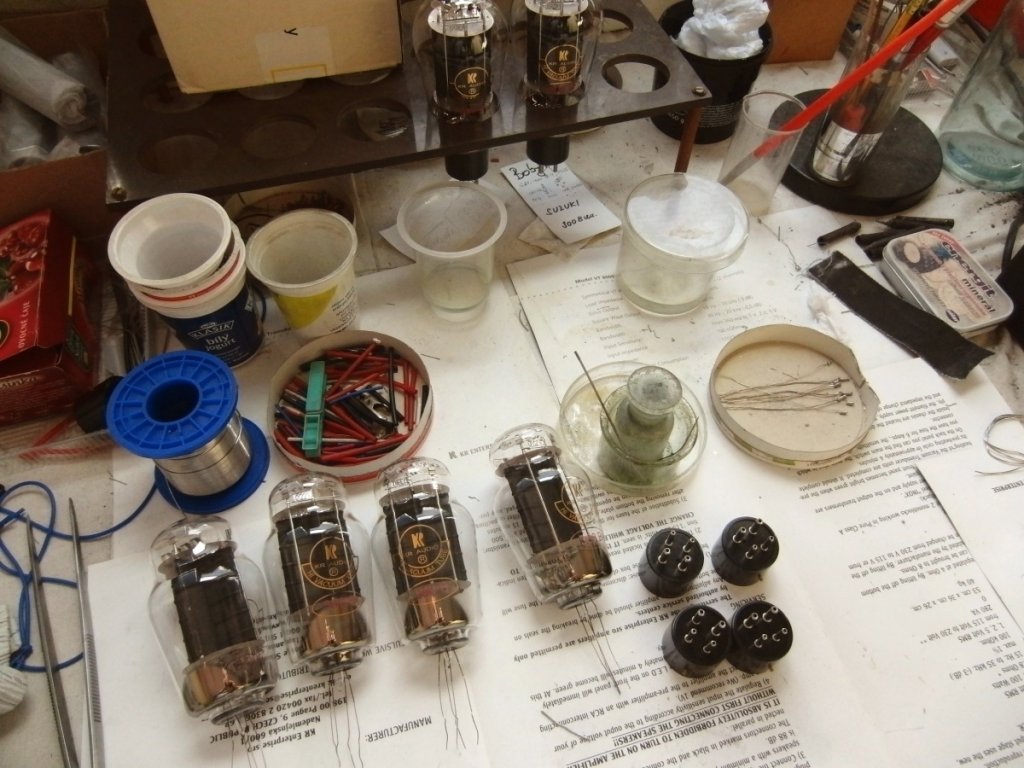
Tubes ready for mounting with sockets.
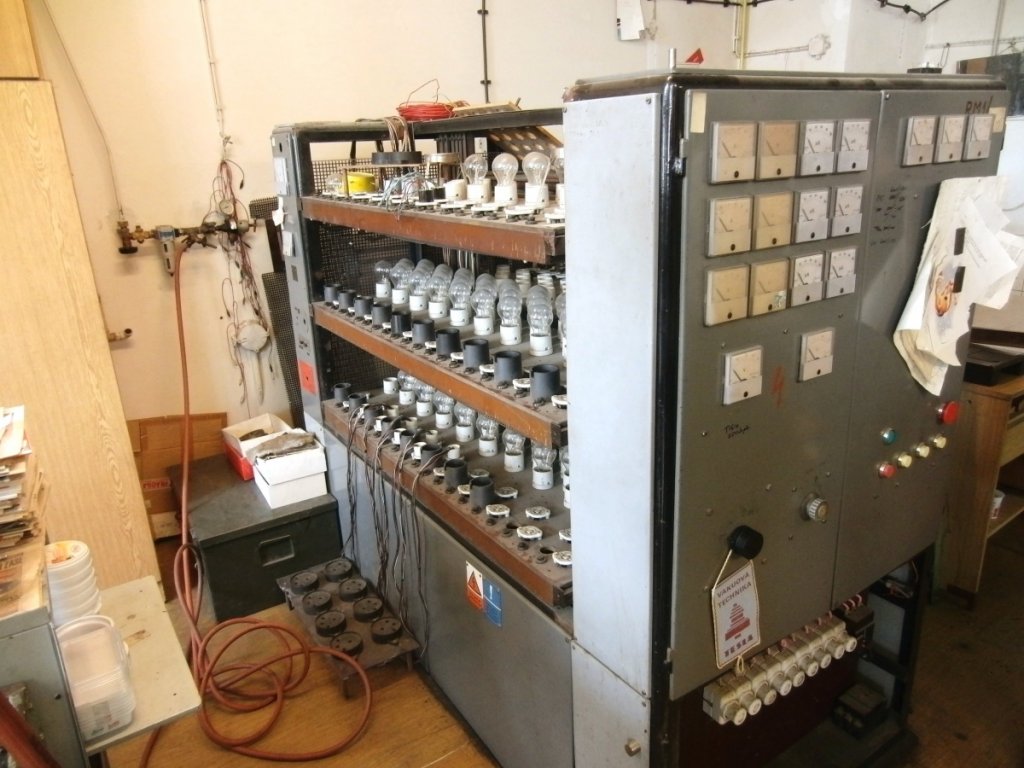
A burn in station for a 24 hour burn in cycle.
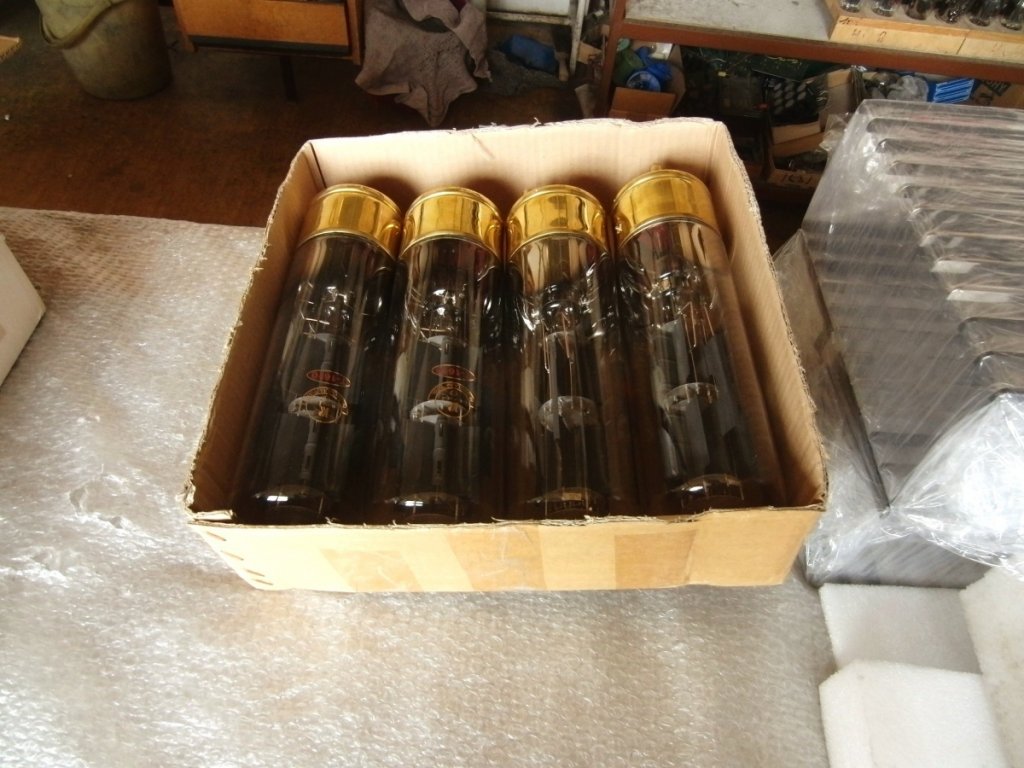
KRT1610 tubes ready for shipping.
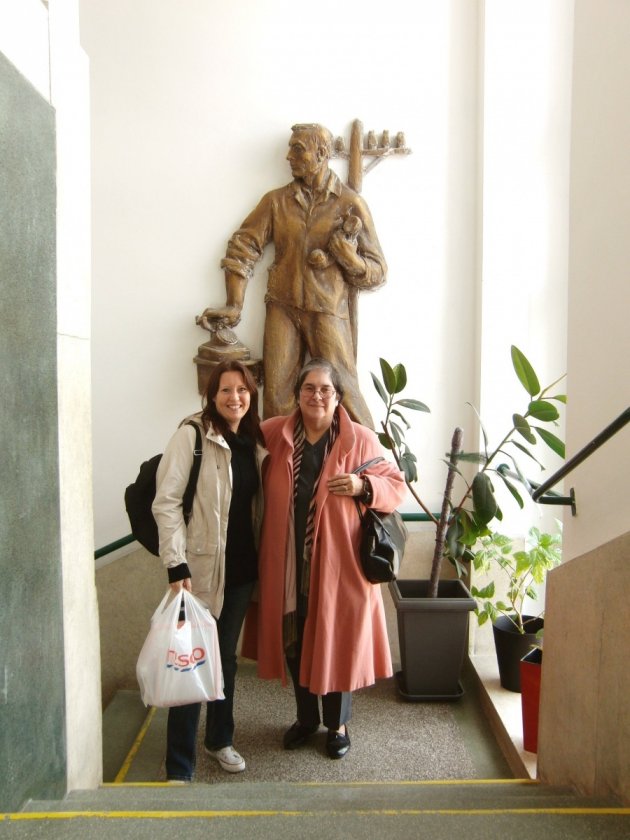
On the way out with Dr Eunice Kron. Notice the TESLA technician on the wall. — with Fredrika Engvall.
It was wonderful to see the factory and I would like to thank KR for the time and dedication they took in guiding us arround. I was impressed by the craftsmanship of the people who work there have, great that tey keep the tradition alive. I am amazed that they are still getting the economy in the business when it takes up to 3 days to produce some of the tubes. I have no financial interest in the visit or posting I´m just simply a tube interested audio geek.
Cheers