I should have mentioned that I was able to resolve an issue I was having with my soldering iron. In my past projects I migrated from a 24w to a 45w pencil type soldering iron. This was needed in order to solder the junction of several heavy gauge wires or a bunch of wires. However, in doing so, I found that after a few minutes of running the 45w iron would overheat and oxidize the solder on the tip, which then needed to be cleaned off in order to make good follow on joints. My solution…
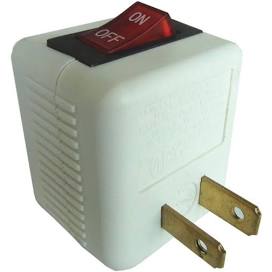
A very simple solution. This way I could have the iron on when I needed it, and easily turn it off when done making a solder joint. Worked great And way better than some of my well over-thought ideas. Yup, a lot of really complicated and/or more expensive solutions went through my head…

As for the heat shrink tubing, my old Black and Decker heat gun has started spitting out insulation. So, I was game for trying something new, keeping in mind how much I hate cords and hoses….
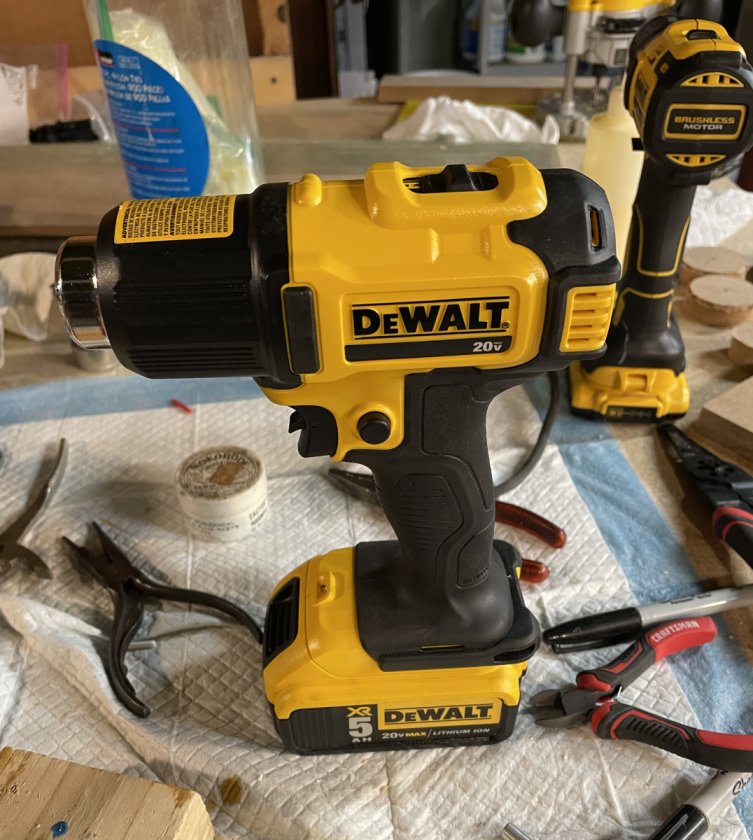
I love the idea of not having a cord that inevitably will knock something off the work bench. And, nope, this will not peel the paint off a wall. But it works great on heat shrink tubing…

And don’t get me wrong, Dewalt makes some nice things that I really like, but they also make some clunkers. The drill in the background is an example…. How could they get the chuck and variable speed so wrong

Now their little 20v router… I am a fan, as you may have guessed from my earlier posts. Yes it can get over loaded with a large bit, like the 3/4” bit I used to make the recess for the binding posts and for the tweeter, but that is easy to work around. Otherwise I find it works really well and there is no cord to deal with

I was even able to rig a vacuum line from the ceiling for dust collection, which kept it from getting in the way.
As it was, it made quick work of holes in the front panel for the drivers and port…
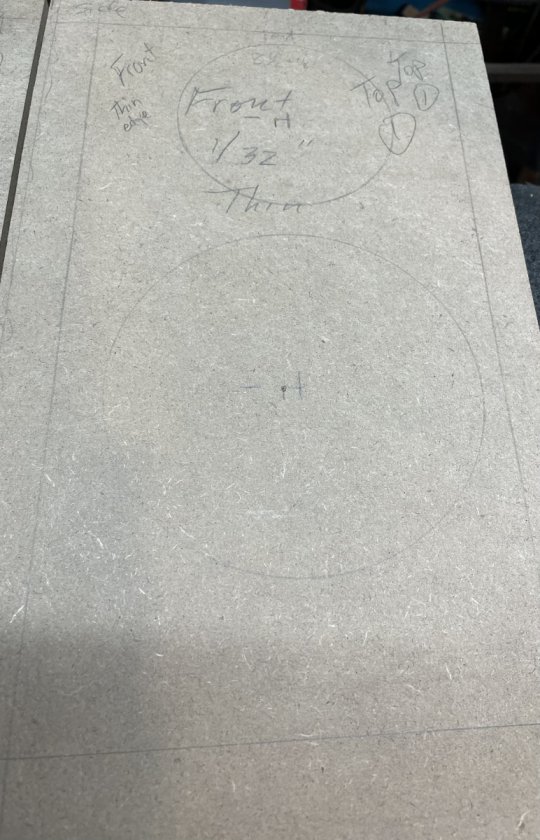
To start, I did a layout of each of the holes. And lo and behold, I caught a mistake on the location of the hole centers on one panel. Yup, just one. Why, just one? Don’t know. Hmmmmm for one panel 8.5” divided by 2 = 4.25 and the other it = 4”.

I did them both at the same time, but long before this. So, there were multiple reasons for making the over check. Measure 2, 3, 4 times…. Cut once…

The hole cut for the tweeter is a 2 step process for me. First is to cut the recess, then the through cut. The recess is 3-15/16” dia and
1/8” 0.18” (or 3/16”) deep. The center setting on the hole jig is 3-7/16” with the 3/4” dia cutter. The through hole is 3-1/8” dia made with 1/8” dia up cut spiral bit with a center setting of 3-1/4” on the hole jig.
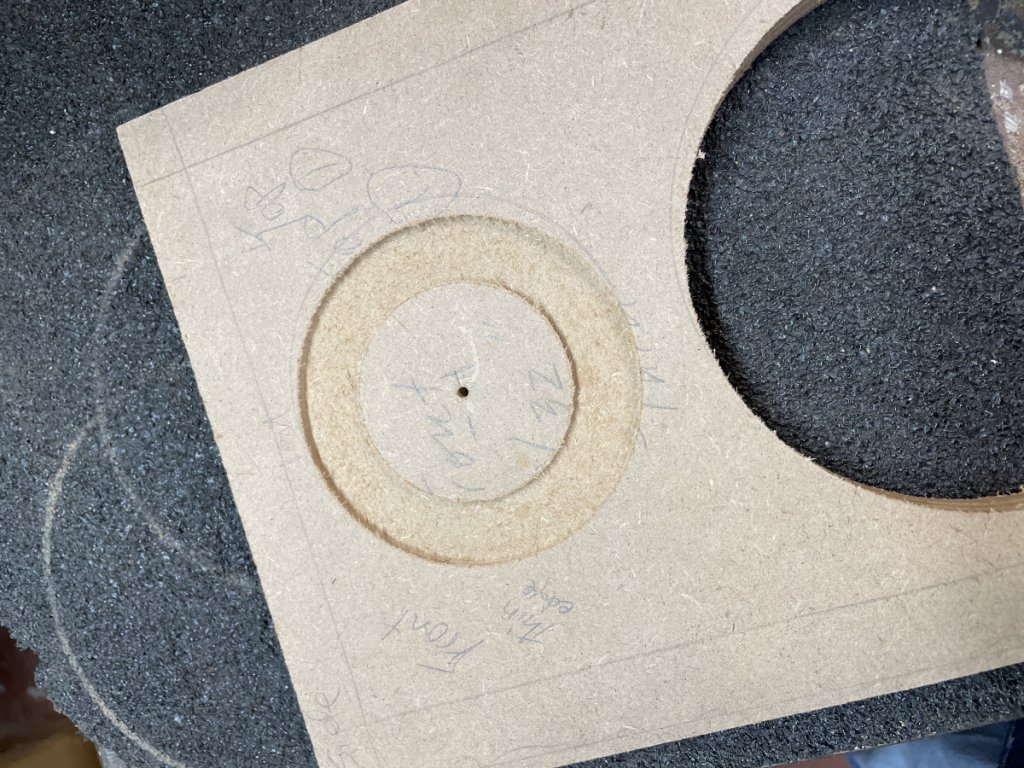
The 2 remaining holes to be made are for the bass driver and the port. The port is a 2” hole made with the 1/8” dia bit with the jig center set for 2-1/8”. The base driver hole is called for 5-3/4” dia, however I like the fit with the hole cut at 5-11/16”. This was done with the 1/8” dia bit with the jig center set for 5-13/16”. Remember that the jig settings here are set to account for the smaller bit size than the 1/4” dia bit the jig is design for. Again, I hope that makes sense.
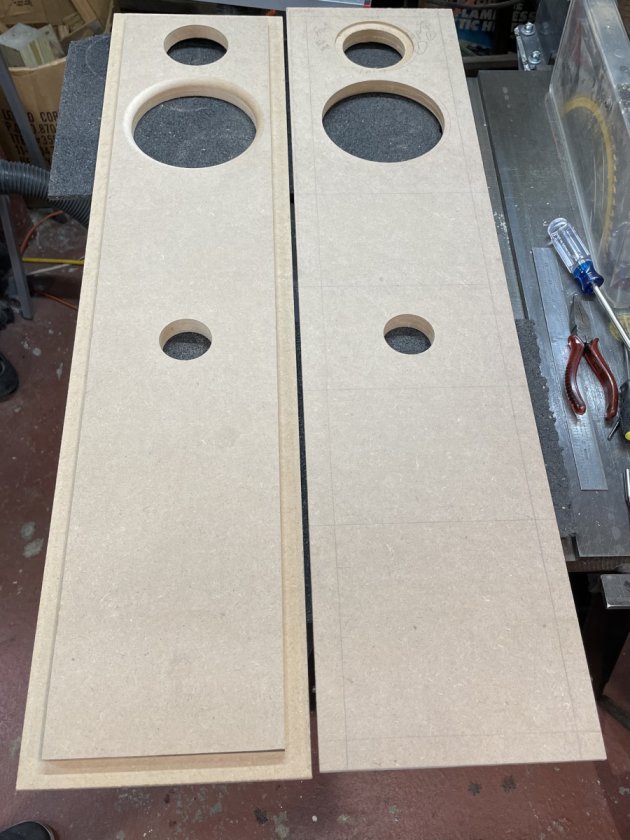
Here are the 2 front panels, one showing the back side and one the front side. I added a 3/8” round over to the back side of the bass driver openings, the same as is called out for the X-LS cabinet. The reliefs for the tweeter driver’s wiring tabs still need to be cut in, otherwise they are ready for being glued in.
Yes, I know, the ports belong in the back. However, that does not work for the room these are going into. So, the same as I made the X-MTMs, the ports are in the front. I will say, if I am missing anything by having the ports on the front of the X-MTMs, I can’t tell. They sound fantastic. I expect these, too, will sound fantastic with the ports in front.
One other thing. Notice the recycled rubber mats I am working on. These were “sticky” enough with the MDF to hold the pieces in place, prevent them from moving/sliding, without any clamps. That was such a bonus to not have to deal with clamps being in the way while making the hole cuts. Further bonus was that they caused no damage to the router bits when they went through the back side of the piece being worked on.
