Next Up was to finish the baffle holes and then cut the edge pieces to shape. Then using the same router fence setting I cut the upper baffle to width so that the edge pieces fit exactly to the baffle. I glued on the edging and flush trimmed it front and back, then added the 3/4" roundover to the front sides.
This was a lot of work and was certainly the hard way to do it. I wanted the inner baffle mdf to glue to the mdf box so the edging is 3/4" thick at the front and has a rabbit cut into it's back side so it is only 1/4" wide at the back. The back layer of the baffle overlaps the box sides by 1/2". Hard to explain, easy to see.
Next I finished gluing the boxes - I let the sides overlap top and back by about 3/32" and inset the back panel. I will be painting these semi gloss black and it is really hard to hide seams in MDF so this eliminates that problem. Hopefully it won't be too ugly.

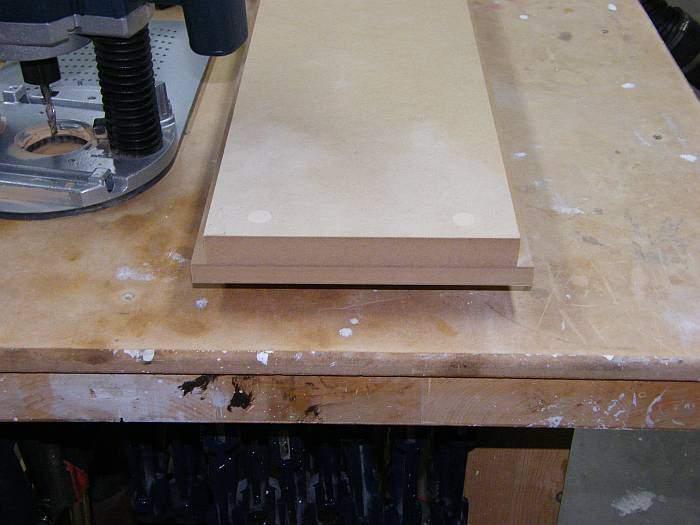
Baffle end view before veneer and solid edging/roundover
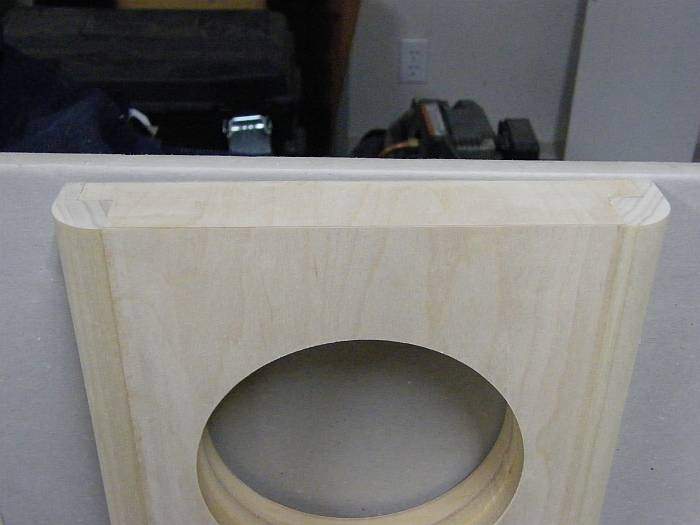
Baffle top view after edging and roundover
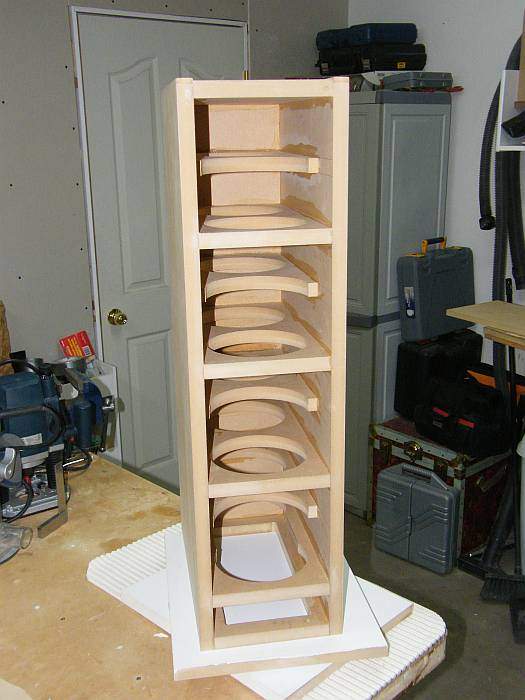
Completed box