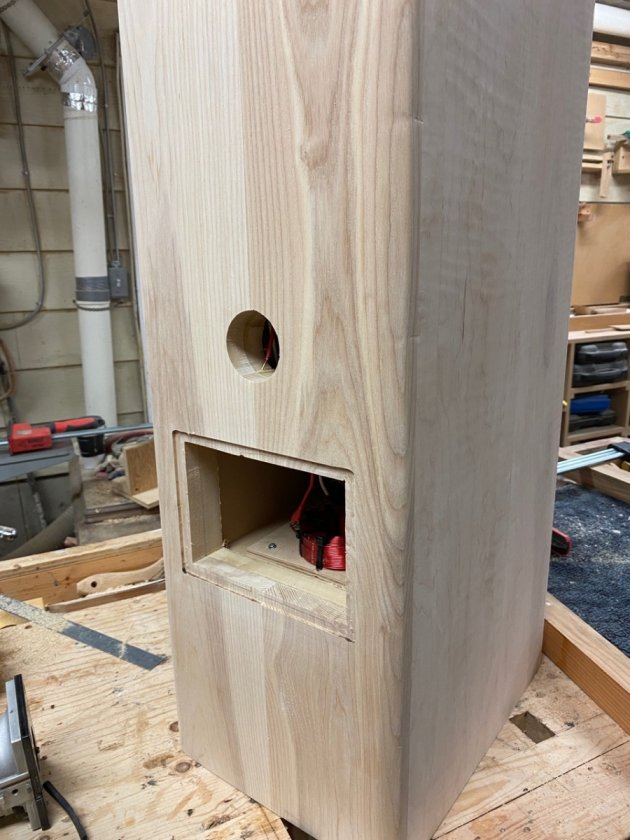
I finally got the backs on. I didn't have enough maple so I made it out of this wood that I had hanging around in my wood storage. I think it is possibly ash or some kind of oak. You will notice some divots in the side where I was not able to hold the router stable when I did the flush trim bit. Next time I will build a much larger base for my little flush trim router so I can avoid this. I decided to make my own binding post plate out of aluminum as I wanted access to the crossover in case I had made any mistakes or need to make repairs in the future. It will sit flush to the back in the little inset.

Well I am finished and they sound amazing! I didn't take as many pictures in the intermediary but suffice it to say that I finished it three times before I was happy. You saw the poly finish above. I hated the way that looked and felt so I sanded it out. Then I went with a straight wax hand rubbed finish. The texture felt really good (I really like touching the things I have made

) but it didn't pop the grain the way that I wanted so I sanded that one out too and started again. One benefit of all this sanding is that it smoothed out the divots in the back.
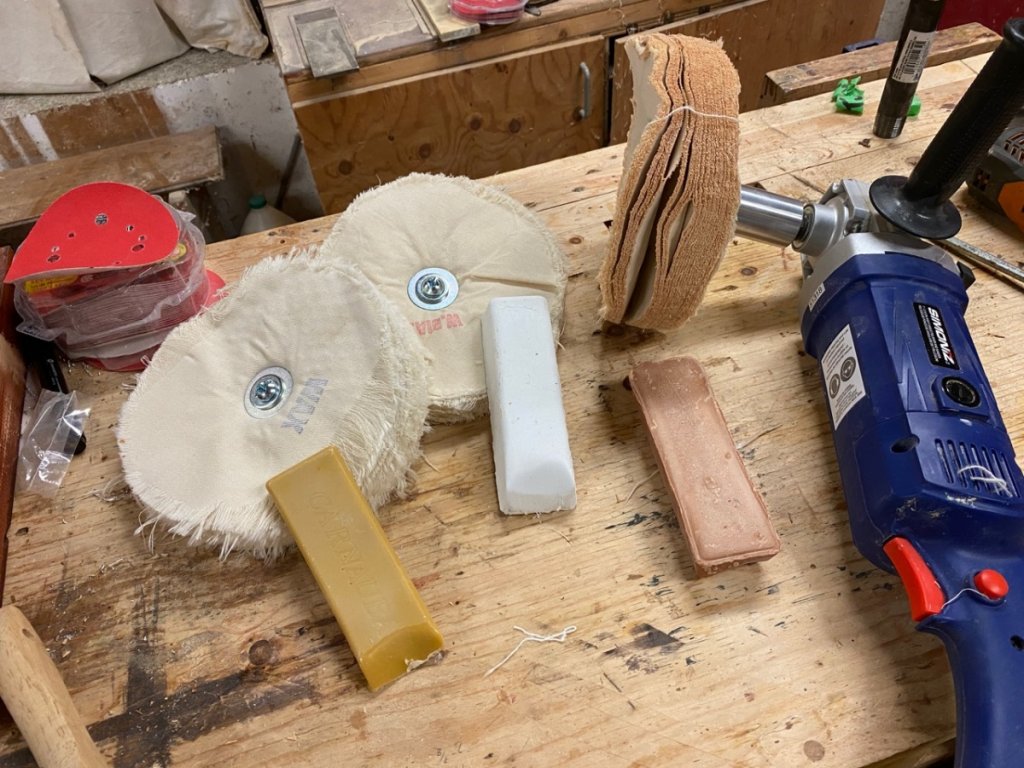
I finally got the right look and texture when I oiled the speakers with Tung oil finish and then waxed it with the Beall buffing system. I had used these buffing wheels on my lathe for smaller parts and they produce my favourite finish but there was no way I would be able to hold up an 80lb speaker up to a buffing wheel on my lathe. I scoured Lee Valley and they had a replacement wheel system with a mandrel to attach it to a bench grinder. I took a chance and ordered it. Lucky me! It fit very nicely on my Simoniz angle buffer. I tried it out on my regular angle grinder but the RPM was too fast. The Simoniz is designed as a buffer so it has a variable speed option. The first two wheels use very mild abrasives to polish the wood and the third wheel applies the wax. It produces the most luxurious silky finish. Exactly what I was looking for.
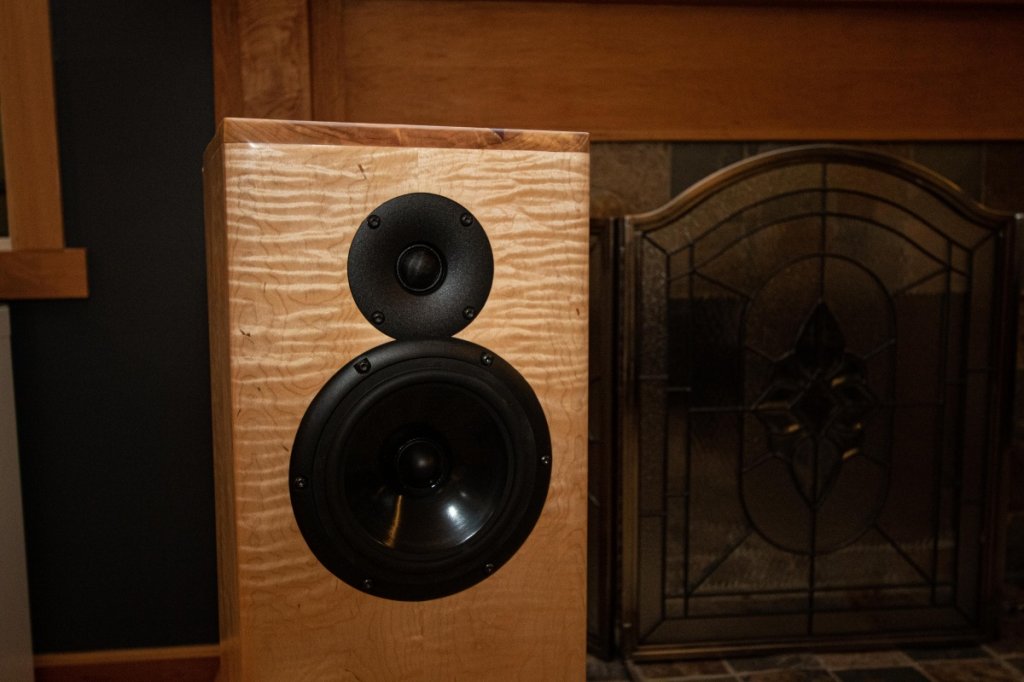
The grain just jumps out of the wood and that tweeter is so wonderful. It has a much more revealing sound than what I was used too. The decay on a piano in a concert hall is full and open.
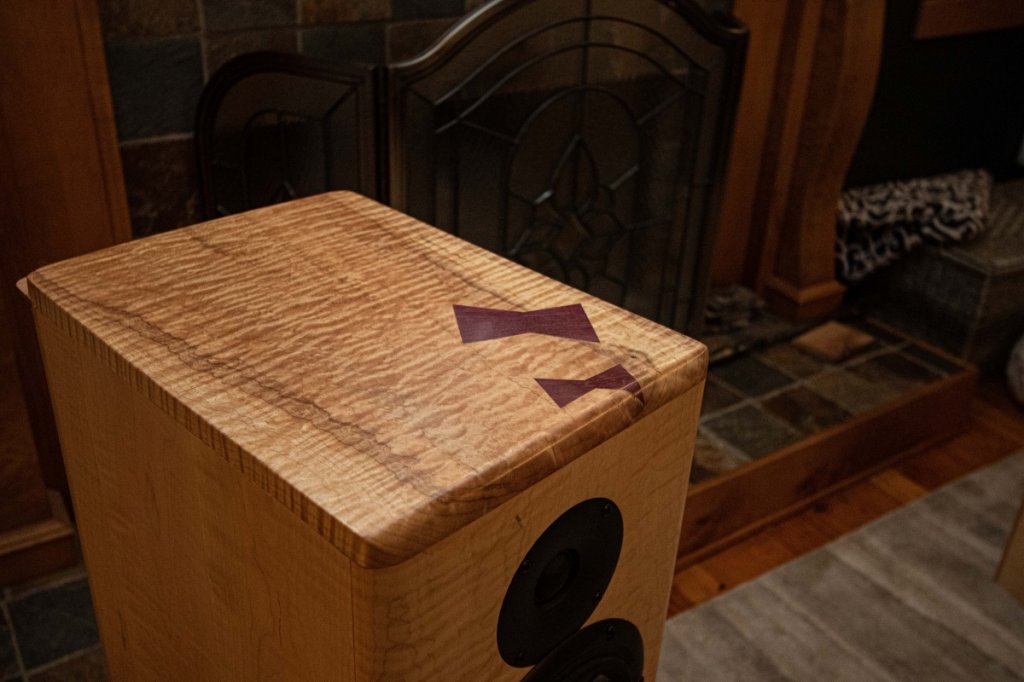
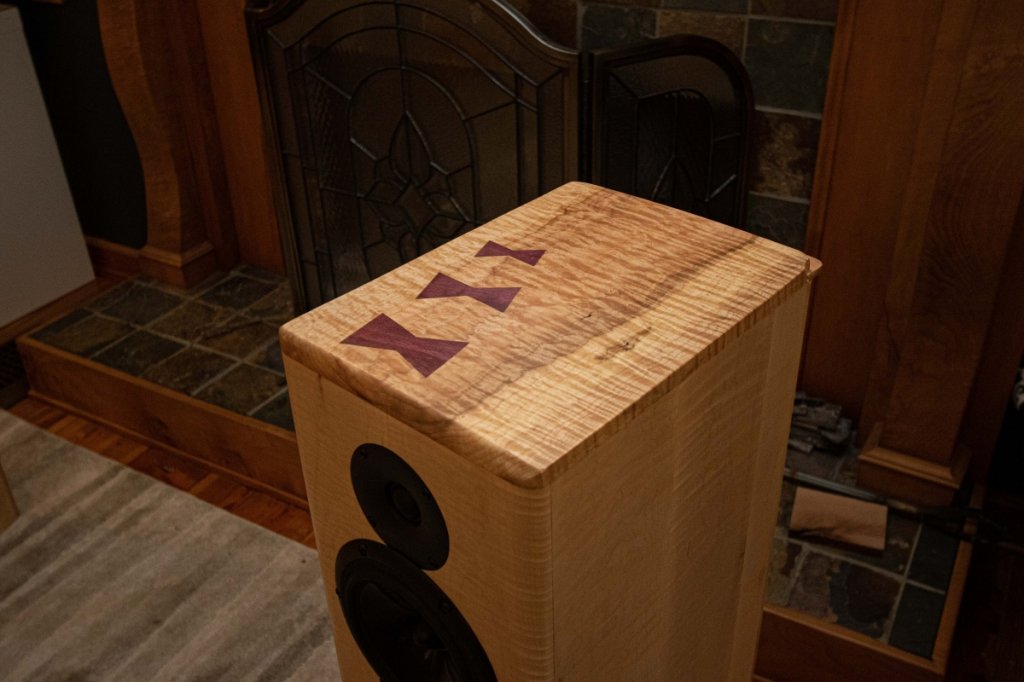
The tops where quilted maple from a very different tree so it provided a nice contrast. I was happy with how the purple heart bow ties turned.
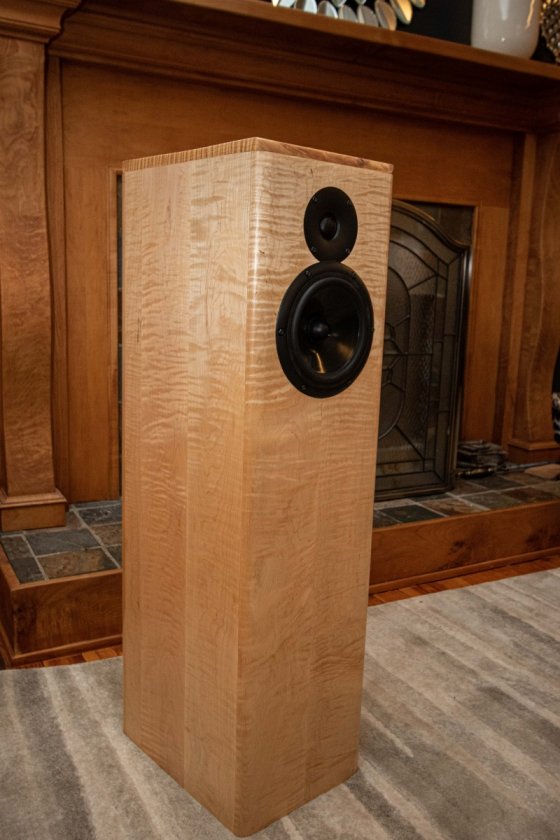
I found that the integration with my sub was much smoother with these X-SLS's than with my previous speakers.
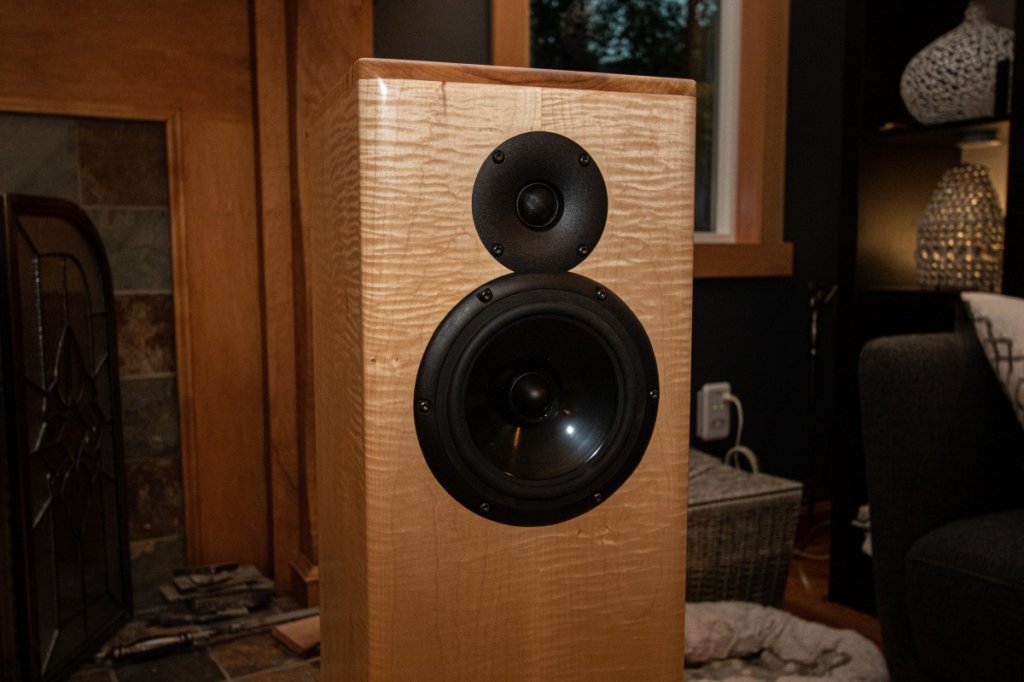
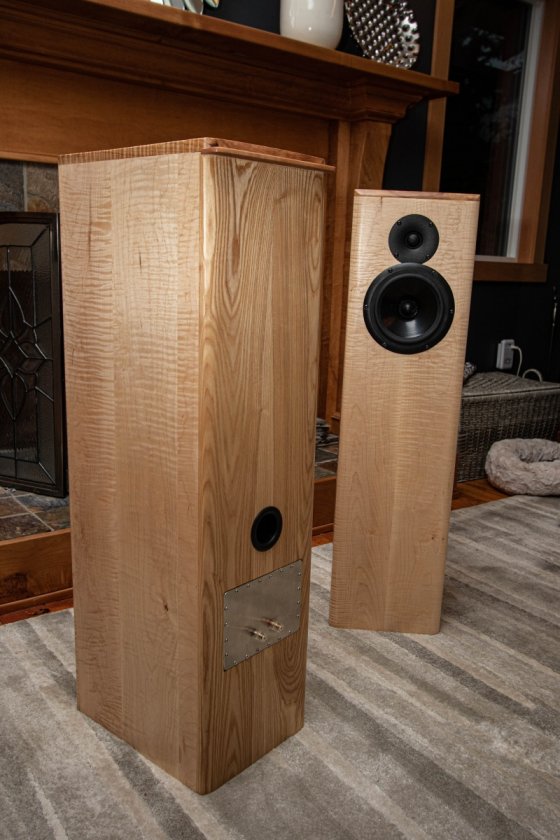
The speaker walls are 1 ½" thick and man are they stable. Even at very high volumes I cannot feel any vibrations on the sides of the speaker. I know that this was over-kill but I wanted to give it a shot. In the future I think I will probably just be building the boxes straight out of hard wood. I really hate working with MDF. I am interested to see if I get any wood movement issues. I will keep you updated.
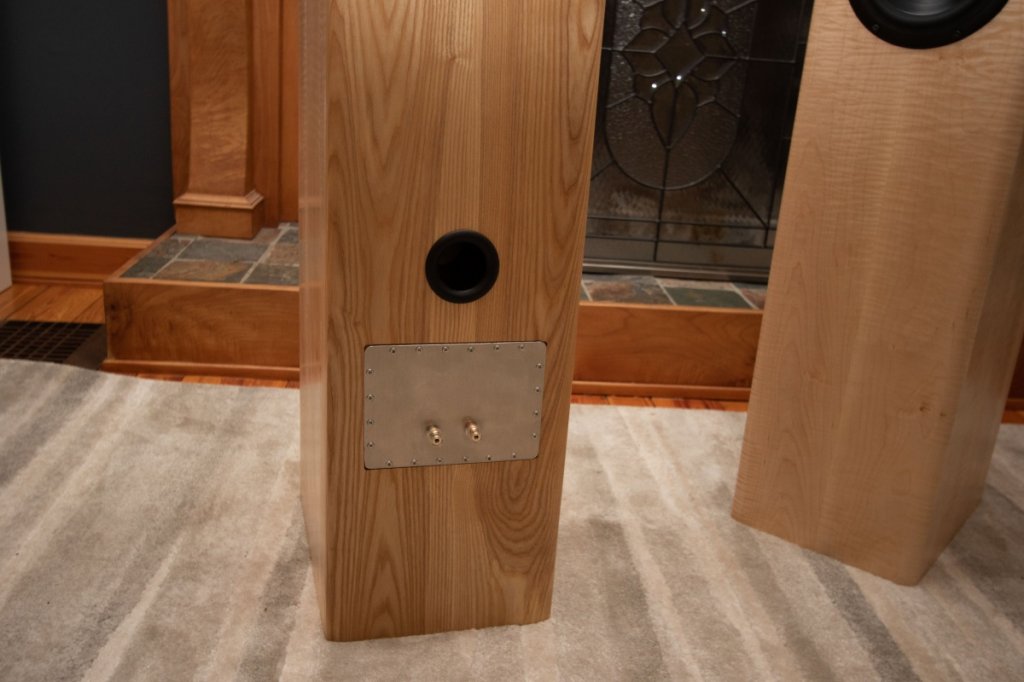
Here is the ash/oak? back. The aluminum plate works nicely as a more interesting replacement for the binding post cup. It also gives me access to the crossover should I have any issues.
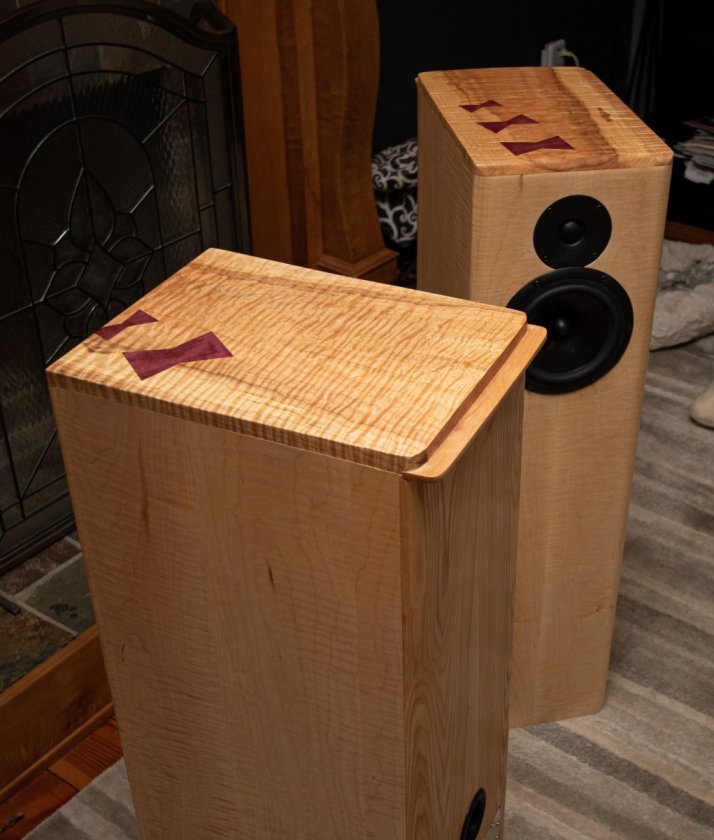
Being a great woodworker means you make very few mistakes. Being a good woodworker means that you know how to hide your mistakes. I had a large gap on the back of the speaker between the top and the back piece of ash. I also had the problem of how I would move these things around when I had finished them to a very slick polish. My gap was ¼" at its widest so I cut a piece of ¼" cherry and routed out a consistent ¼" groove across the back over top of my gap. I then glued in the piece of cherry which acts to fill the gap completely and provide enough a ledge that I can lift the speakers.
This was such a fun project and the satisfaction that I am feeling right now as I listen to something that I made as I type this so worthwhile. Thank you to Danny for the wonderful design and for supplying the electronics and the drivers. It is such a pleasure to have such an affordable entry point to such high quality speakers and we all owe you a great debt for making it so accessible.
-Russell