TRIPLE- WALL LAMINATE CONSTRUCTION
Below is a photo of VSA's Pat. Pend. wall construction, as used in every Von
Schweikert speaker system offered today. This wall construction was pioneered for use in our UniField Model 3 speaker system in 2007 and has been so successful that we utilize this method in all VSA models in production today.
The idea is to use mass loading combined with "over-kill" wall damping to reduce vibration. In addition, we've discovered a clever method of "Q interaction" in the layers of laminations to further boost the damping effect.
The VSA Triple-Wall Laminate Construction uses three different materials that have an inherent difference in their Q factors, Q being a qualitative factor. The choice of these three different materials was based on how their Q factors interact with each other, with a dense inner high Q layer and soft low-Q inner and outer barrier layers. The three layers are bonded together using a rubberized adhesive (in itself a barrier to mechanical vibration transmission). The three layers consist of the following materials:
1. Outer shell: MDF (medium density fiberboard) is a medium Q material, with a high degree of sound transmission. By itself, MDF (even with a high quantity of resin impregnation), is not a one-step solution. The colorations of MDF tend to be woody but musical in timbre, almost like the sound of a cello, but this coloration is not desirable from the standpoint of utter neutrality. MDF is used by most fabricators due to ease of machining and low cost. Resin impregnation adds mass and stiffness, which serves to raise the frequency of resonances to an area above the critical range. Our Unifield Series of speakers use a molded outer layer of resin with fiberboard powder composition. All other VSA speakers use compressed MDF with resin impregnation as outer walls, using #2 and #3.
2. Inner liner: Bonded to the inner side of the MDF outer shell is a layer of synthetic stone, fabricated from crushed gravel, minerals, and resin binder. This layer exhibits a very high Q, with a tremendous mass and stiffness quotient compared to MDF in fact, it is more comparable to solid aluminum and is far denser than any type of plywood laminations of comparable thickness. The synthetic stone inner layer is formed of small blocks that are bonded to the MDF with an industrial anti-vibrational rubber-based adhesive. The adhesive layer is extremely thick (5mm) and provides an additional mechanical barrier in addition to shearing of energy, turning mechanical motion into heat for dissipation.
3. On the surface of the synthetic stone layer is a final layer of hard felt, with an extremely low Q factor. This layer provides absorption of the acoustic energy generated by the transducers on the inside of the cabinet. Once again, the felt layer is bonded with the same rubber-based adhesive, enabling further damping.
4. Since the transmission of energy requires an efficient medium that will conduct vibration readily, the use of these three different layers effectively absorbs the energy before it can reach the level of audibility. These three layers have been designed to be the most efficient combination of vibration absorption for their given thickness, weight, and cost-- far surpassing any other method of cabinet wall construction and guaranteeing genuine transparency of sound.
Shown below is a side-view photograph of the UniField Model 3 cabinet wall. The molded outer layer of resin-based MDF is to the right of the photo, with the white synthetic stone layer in the middle and the hard felt inner layer shown in dark gray. The black material shown in between laminate layers is the rubber adhesive layer used for bonding and vibration damping. The white fluffy material to the left of the felt layer is Acoustic Dacron polyester fiberfill, used to damp the internal cavity resonance created by the hollow cabinet. We apply the Dacron in three different thicknesses, which we term "Gradient Density DampingTM." The Dacron is packed extremely tight closest to the cabinet walls, and is gradually packed with less density approaching the rear of the driver. This technique provides absorption without reflection back into the cone.
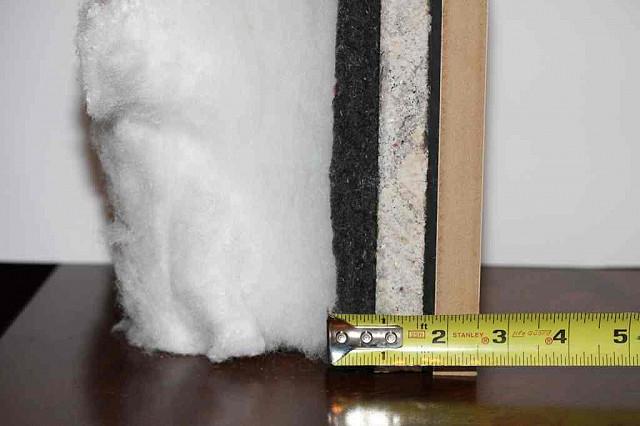
Triple Wall Lamination photo by A.V.S.
On various VSA models, the wall thickness can approach 4 (100mm) but on the UniField Series, shown above, the total wall thickness is 2.5" (63mm).
VIBRATION CONTROL THROUGH ISOLATION
It is known that the cabinet walls are set into resonance by two different means: A) the physical vibration of the driver, transmitted to the front baffle, in addition to: B) the acoustic energy transfer from the rear of the driver into the cabinet cavity. In order to reduce this unwanted transfer of energy, we have devised a method to isolate the driver from the front baffle, in addition to isolating the front baffle from the cabinet proper in the UniField Series of speakers.
A) In order to effectively isolate the vibration of the driver from the cabinet, we have employed the use of a 6mm thick, visco-elastic polymer clay gasket material, originally designed to damp the hull of nuclear submarines. The damping property of this proprietary gasket is extraordinary and serves to nearly eliminate the transfer of energy from the driver frame to the front baffle. In essence, our drivers are floating on the surface of the baffle and hence cannot transfer vibration into the rest of the enclosure. This technique alone drops the resonances down by more than 12dB compared to conventional driver mounting methods used by our competitors. This is a tremendous reduction of distortion!
B) The drive units radiate energy acoustically into the interior of the cabinet, which can result in a highly audible cavity resonance. These reflections from the internal walls of the cabinet create a pressure wave on the rear of the cone, resulting in dips and peaks in the frequency response related to the wave lengths involved with the dimensions of the internal cavity. Our use of the hard felt inner damping layers, combined with our proprietary Gradient Density Damping,TM, reduces the internal cavity resonances below audibility. By contrast, the examination of our competitor's cabinets will reveal that they use hollow cavity design to "enhance" resonances to achieve their desired voicing.
BRACING TECHNOLOGY
Although our cabinet wall damping technique is state of the art, we also employ over-kill internal shelf bracing, which also forms the chambers for our hybrid reflex transmission line bass loading. The UniField Series also use curved side walls to reduce internal reflections that cause standing waves and non-linear frequency response, while our VR Series use slanted front baffles and massive cabinet construction techniques found in products that cost several times our price.
TRANSPARENCY FACTOR
In 1976, while developing acoustic theory at California Institute of Technology, I coined the term "Transparency Factor" to describe a recipe of engineering requirements to elevate a moving coil loudspeaker to the clarity levels of electrostatic speakers, which do not use cabinets. More than three decades later, I still believe that our goal of achieving better sound through scientific research has paid dividends in enhanced clarity, image focus, and transparency through the reduction of distortion and colorations inherent in cabinet design. Our latest development of the Triple Layer cabinet wall design fulfills this goal in a novel and quantifiable way.
Direct side-by-side a/b comparison tests with the most expensive and most hyped speakers in the world have proven the effectiveness of our cabinet wall resonance damping technology our speakers sound more transparent than competitors costing up to 5 times our price due to the reduction of coloration and distortion inherent in single-material cabinet designs.
Copyright 2009 by Albert Von Schweikert