Some people believe that quality Baltic Birch plywood is better than MDF. Has a more pleasant sound. I use it for that reason plus I just don't allow MDF into my workshop. Too many bad issues with it.
+1
Except for being cheap, MDF is not that good a speaker building material.
Speakers can, and have been built from solid, but you do need to know what you are doing to keep them from cracking.
I have some here in Yew and in Douglas Fir (a pine, these built from a 70-year old floor) and we have played with Western Red Cedar (a good build material except for the soft surface that easily dings) and others.
All. built by a skilled woodworker who knows what he is doing.
Fir:
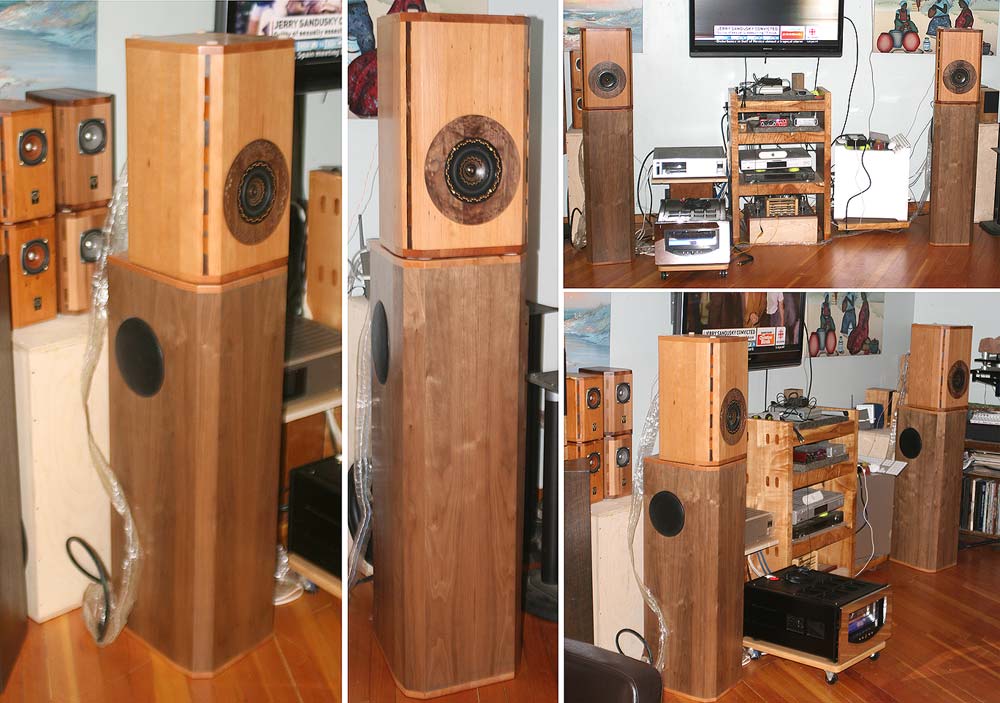
Walnut:
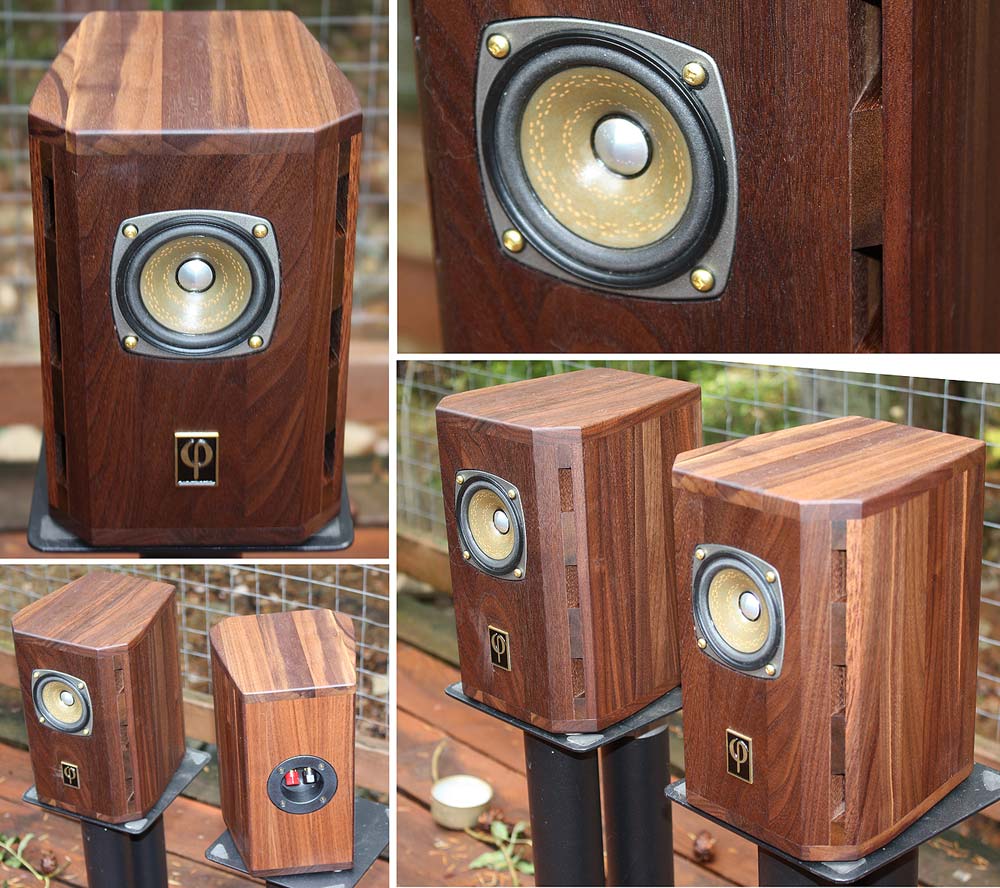
I have many more examples if you’d like.
If you can afford it, stranded/folized bamboo plywood is an outstanding material that bringsmany of the assets of solid with the benefits of plywood.
dave