Danny - Thanks!
The cut plan I came up with has the sides, tops and bottoms coming from one section of MDF and the rest from the other section. The sides and top/bottom pieces are such that length of the top/bottom pieces is the same as width of the sides. That way the sides and top/bottom pieces can be made with one cut across the MDF and then a cut across each of those to separate the the top/bottom pieces from the sides. Then cut the width of the top/bottom pieces. Theoretically, this should mean that there will be no fitup differences between these for the front to back of the cabinets.
Sides and Top/Bottom pieces cut plan from one section of the MDF
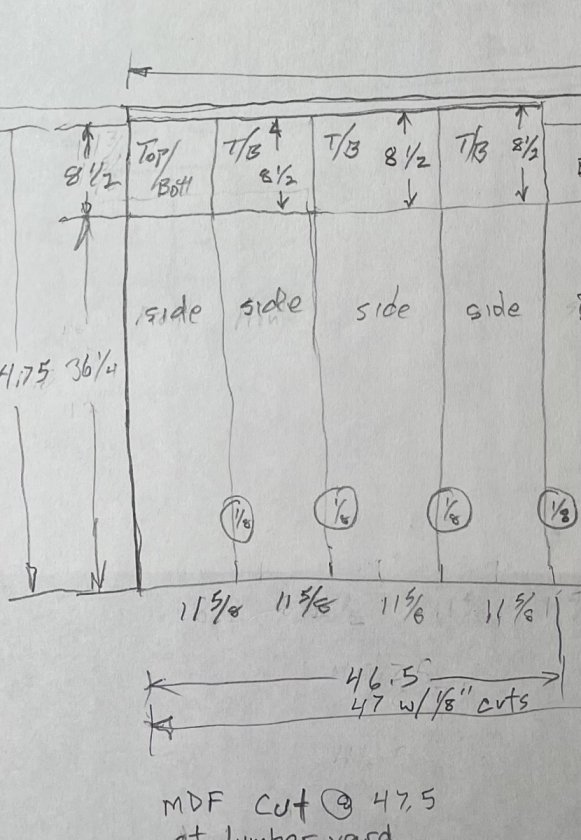
And, yes, the width of a MDF board is 49” not the 48” I have show…

The reminding MDF piece cut plan for the fronts, backs, and braces
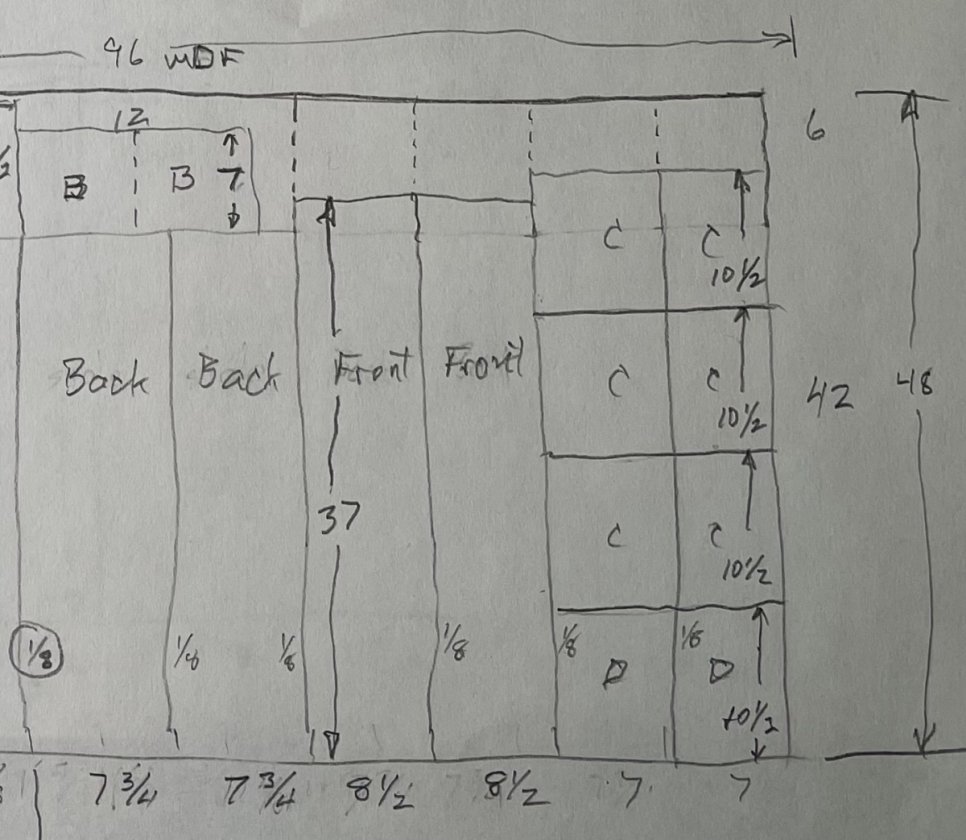
The one thing I did buy new for this project was a 6 foot long piece of 1x2 inch rectangular aluminum tube to use as an edge guide for cutting the MDF and to extend the fence on the table saw for trimming the longer pieces.
Most of the long cuts on the MDF were done with my router with the 1/8” up cut spiral cutter.

I used the router instead of just running it through the table saw as I feared that, with handling the board, any wobble would mess up the cut. Even the approximately 4’x4’ piece of MDF is heavy for me and awkward to maneuver. The router gives me good dust control, far better than using a circular saw or even the table saw. This has all worked well in my previous builds.
And, yes, I wore a dust mask the whole time and had a fan running to blow air out of the basement.
The table saw table and some stands with a 2x12 board made for a nice cutting platform and the space between the two allowed the end of the router bit to go fully through the MDF without hitting anything. This setup worked better than making these cuts on the workbench where, in the previous builds, I had to prop everything up on boards to make clearance for clamps and the cutter.
The final router cut…
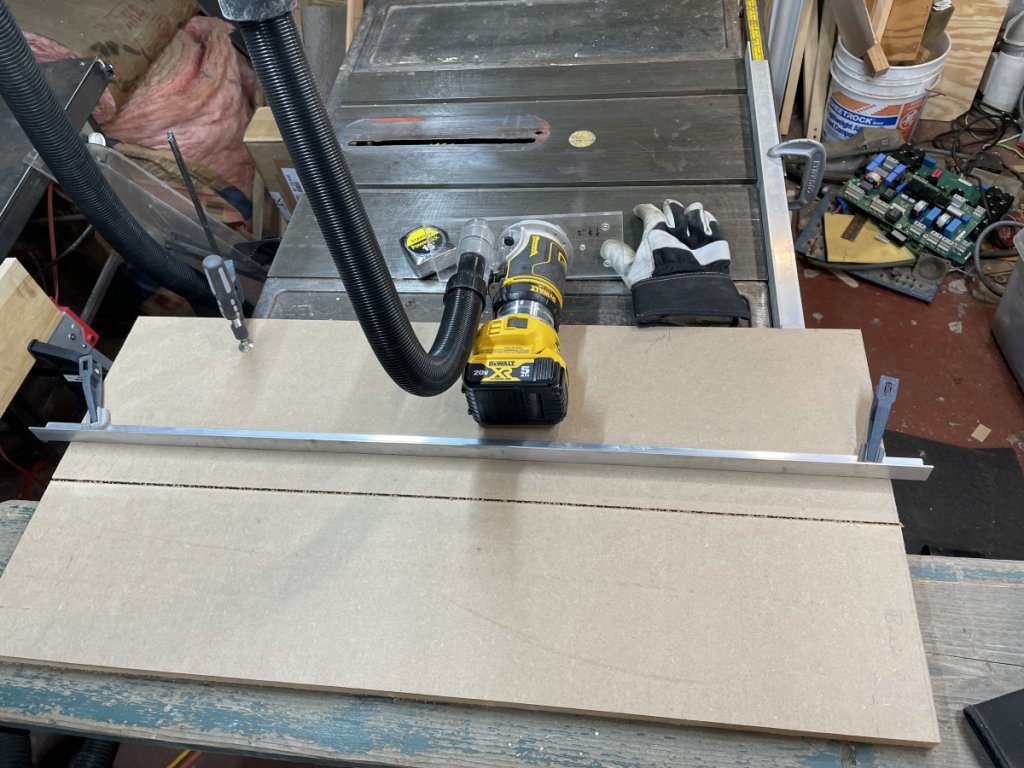
Then the last cut was done on the table saw.

Note that all of the measurements for my router cuts were all made from the uncut edge of the MDF board. That is, the edge that originally existed when the board was made. In a way, that edge became a “datum” that didn’t change, making each successive cut would be square. Had the measurements from a previously cut edge, then any errors, even very small errors (which will exist), would be compounded with each successive cut.
Once the length wise cuts were made, the miter saw made quick work of separating out the top/bottom pieces from the sides, each of the internal braces, setting the lengths of the fronts and backs…. Etc
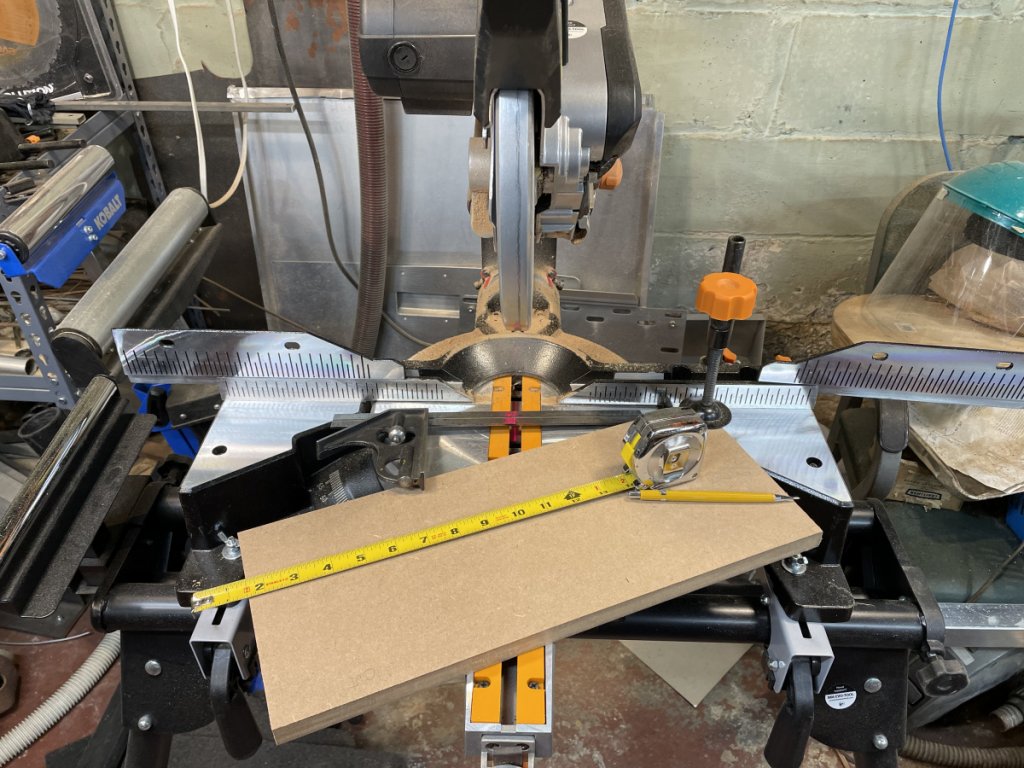