I figured I'd share this here on forum in case anyone else experiences a similar problem and is looking for a solution.
A customer reached out to me explaining that he had a pair of 24-strand braided cables in use but one of the cables, barely reached, was stretched really tight, and needed some extra length. The initial request was about the viability of reterminating one end of the existing cable with female tube connectors, to be connected to a new 3 foot braided cable that I would assemble for him. Basically the thought was to use a pair of male and female tube connectors to join the two cables.
My default position is generally on the frugal side and I didn't want him to incur expense of additional tube connectors or have a possible weak link. I imagined the connection immediately or eventually requiring additional securement to keep the two ends well mated, especially if any force or movement was applied.
I gave it some thought with 2 resulting proposals.
#1 was to repurpose the existing 12ft cable by cutting it in half and rebuilding it into a 6ft pair which would be resold to pay the cost of my building him a new 15ft cable. That would give him the needed length, without the tradeoff of a joint or additional connectors.
Proposal #2 was to cut the tails off of one end and then manually slice together each of the 24 strands with a new 3 foot extension.
Manual splice was the chosen path, so here we go:
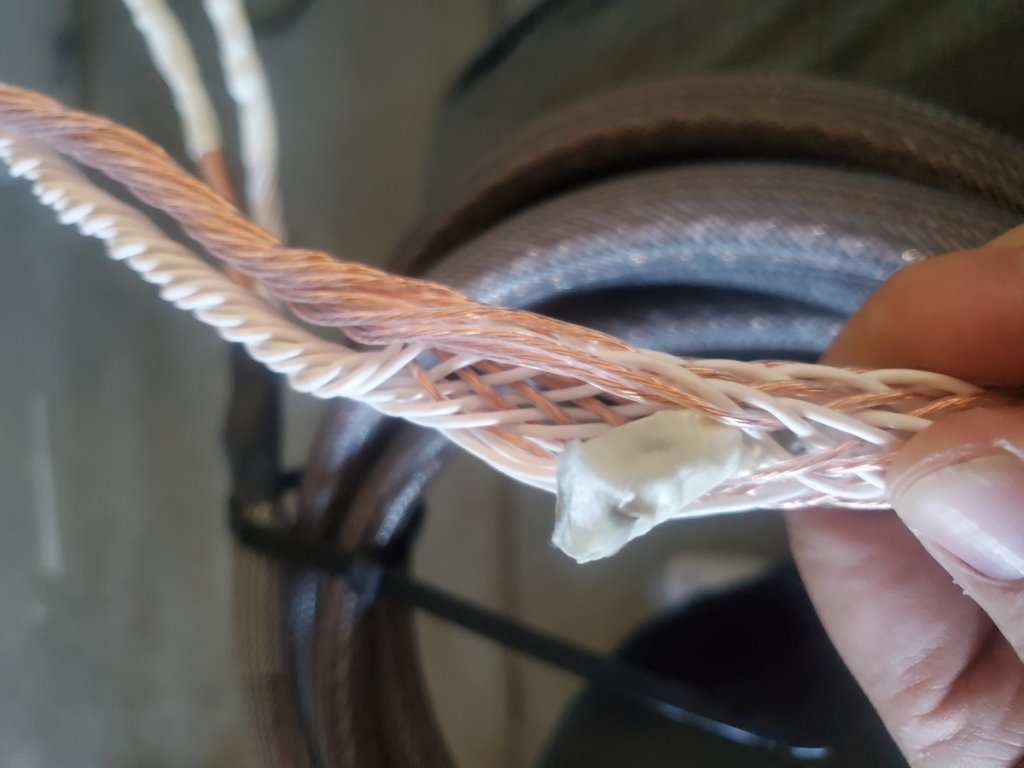
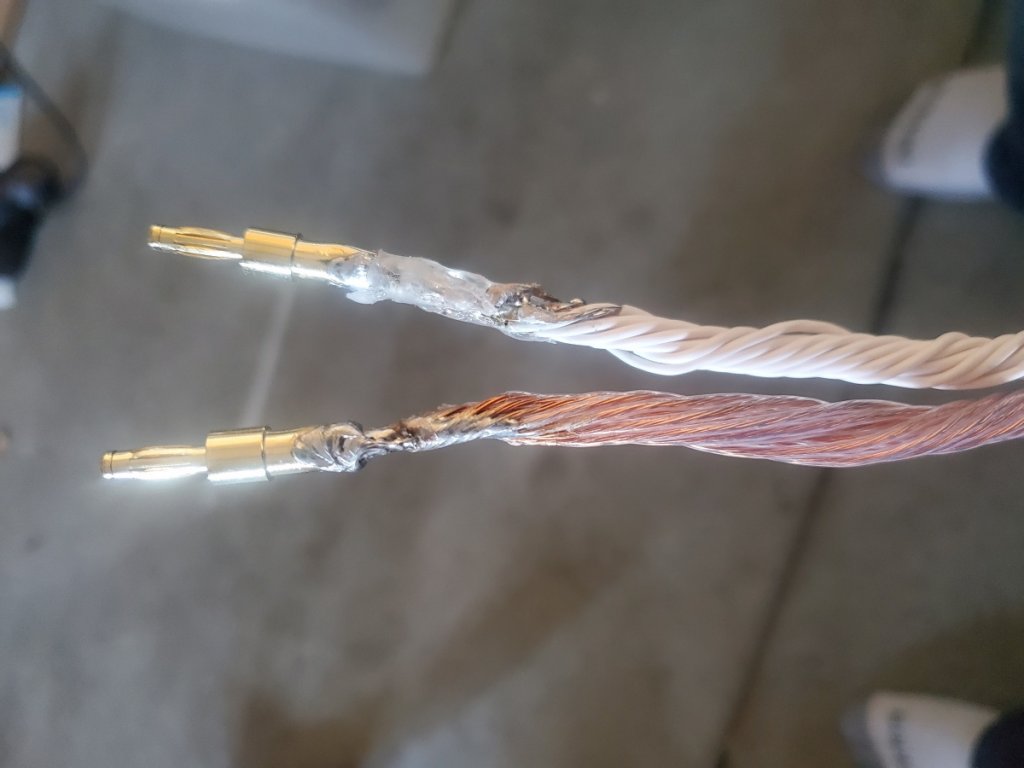
Top two photos show the existing cable tails. I wasn't too excited with the original assembly quality, but I realize how labor intensive these are, so anybody "on the clock" is going to feel rushed. In the end I'm sure performance is the same, I just prefer a more tidy end product.
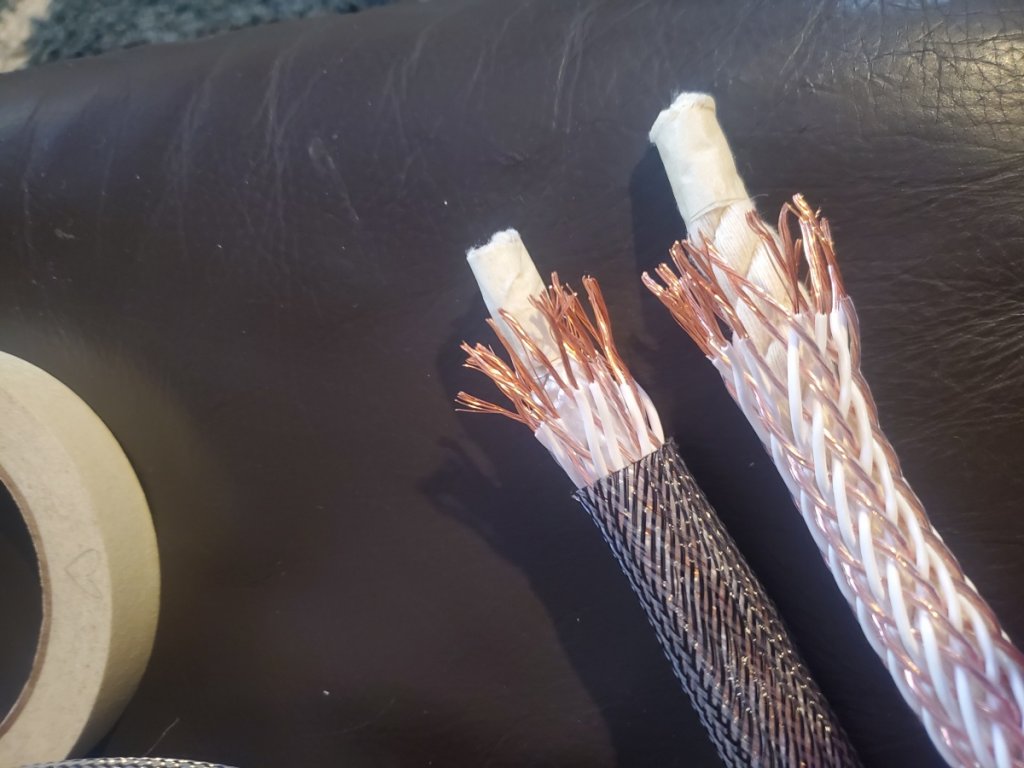
Here's the original cable and the new extension together with each strand stripped for joining.
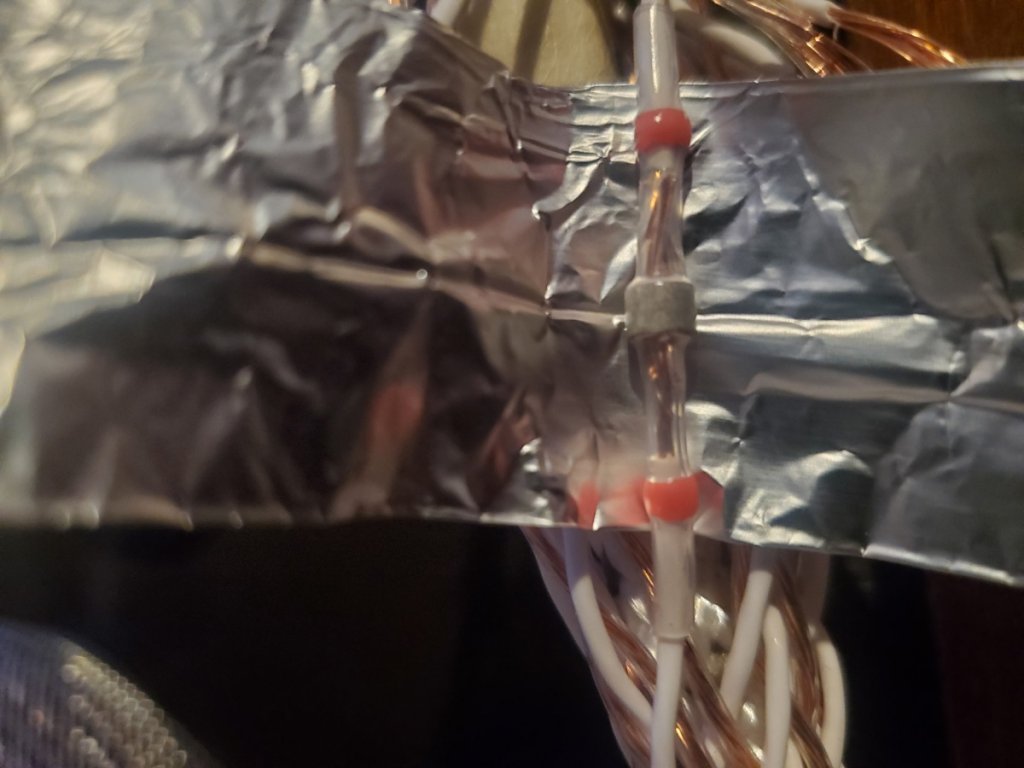
Foil heat shield is used to protect rest of the cable and each strand is joined with a marine type, low heat solder sleeve. The outside ends heat shrink onto their respective wires, the low temp solder in center melts to join the exposed and intertwined strands.
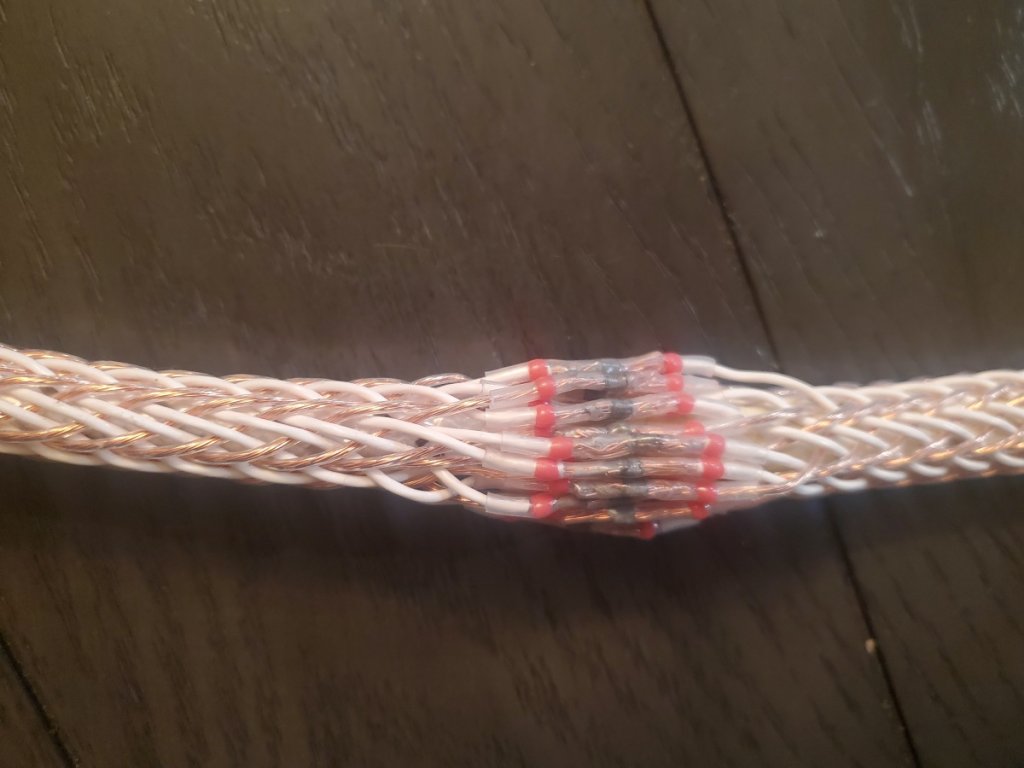
24 solder sleeves later, 2 cables are now 1. There is some labor precision in having the right lengths stripped, then sliding the solder sleeve up into the braid while physically combining the two strands and maintaining proper braid structure. However, it is not overly complicated for anyone attempting the task.
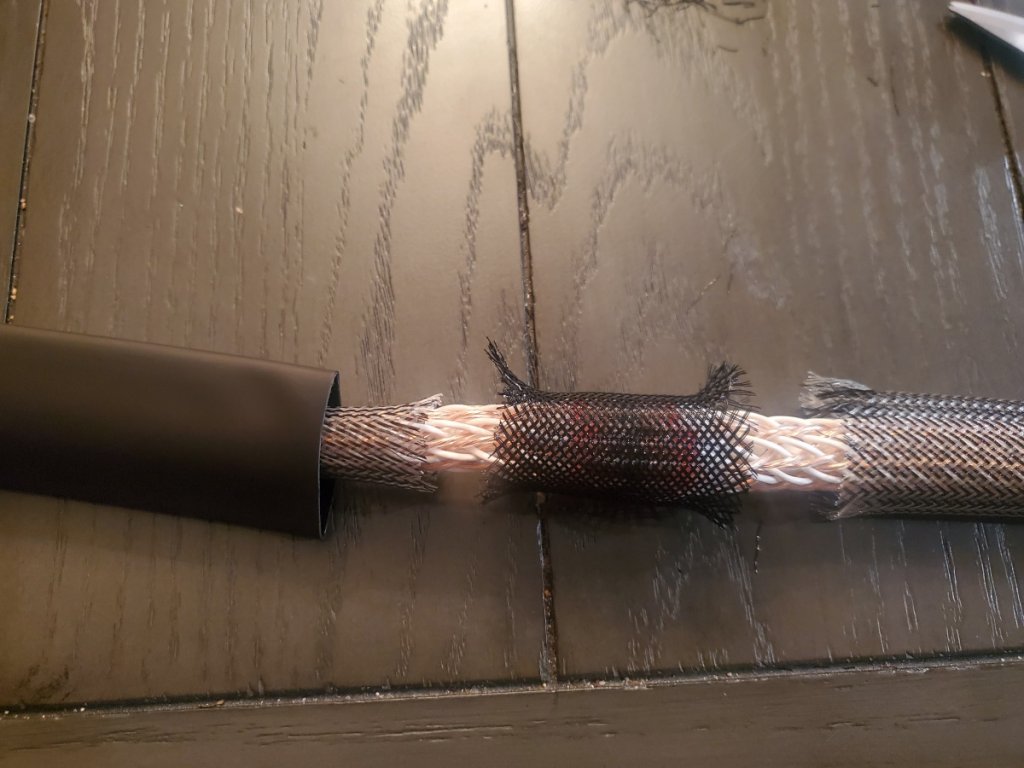
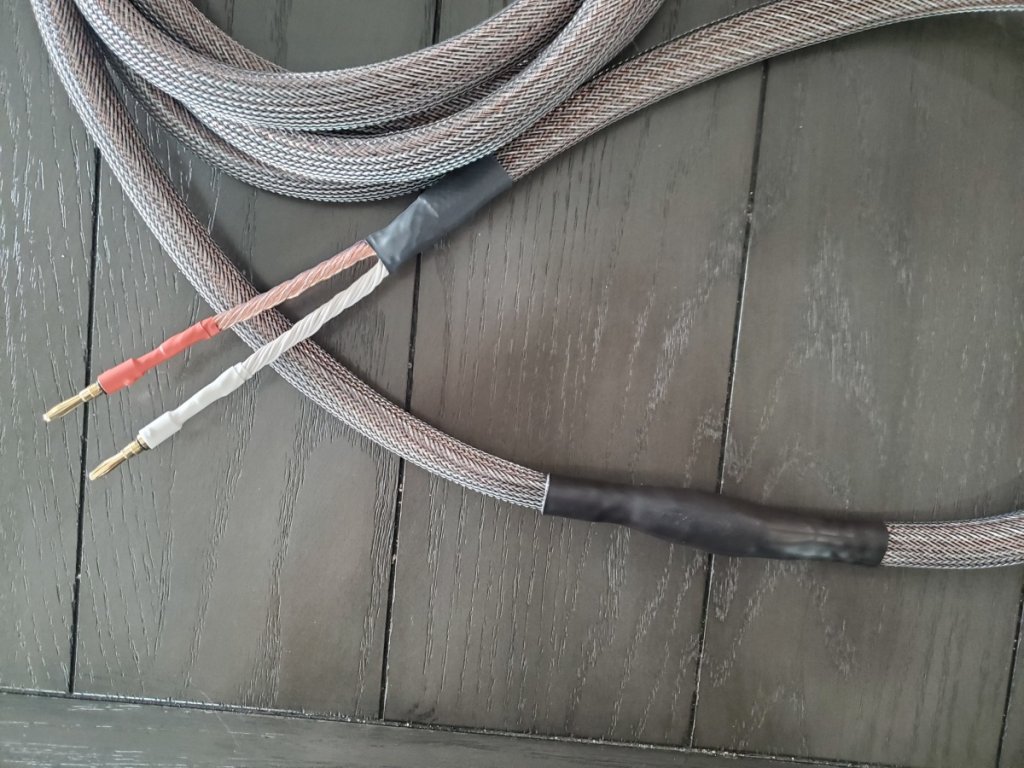
I placed a heavy heat shrink over the joint for protection of the joint itself. The extension is 3 feet long, on the amplifier side so it will not be seen by anyone. Under the heat shrink I used a scrap of expandable sleeving directly over the solder sleeves so they would not adhere to the heatshrink adhesive. The exposed wire braiding on each side of it does allow some adhesion to support the joint on each of its ends. The extension end got terminated with some new banana posts since the originals weren't going to be worth the effort to reuse.
Hopefully if anyone comes across a similar task this will help them out. Happy Saturday everyone. Feel free to reach out if I can be of assistance.
Elon
ezeescrossovers.comElon@ezeescrossovers.com